The effect of temperature on thin film deposition is profound and multifaceted. Temperature influences the quality, density, and composition of the deposited film, as well as the rate of deposition and the presence of defects such as pinholes. Higher temperatures generally result in denser, higher-quality films with fewer defects, as they enhance surface reactions and improve film composition. However, the application and substrate material often impose temperature limits, as excessively high temperatures can alter the film's properties or damage the substrate. In processes like Plasma-Enhanced Chemical Vapor Deposition (PECVD), higher temperatures (typically 250-400°C) yield films with lower hydrogen content and slower etch rates, while lower temperatures may lead to films with more pinholes and reduced quality. Proper temperature control is thus critical to achieving desired film properties and performance.
Key Points Explained:
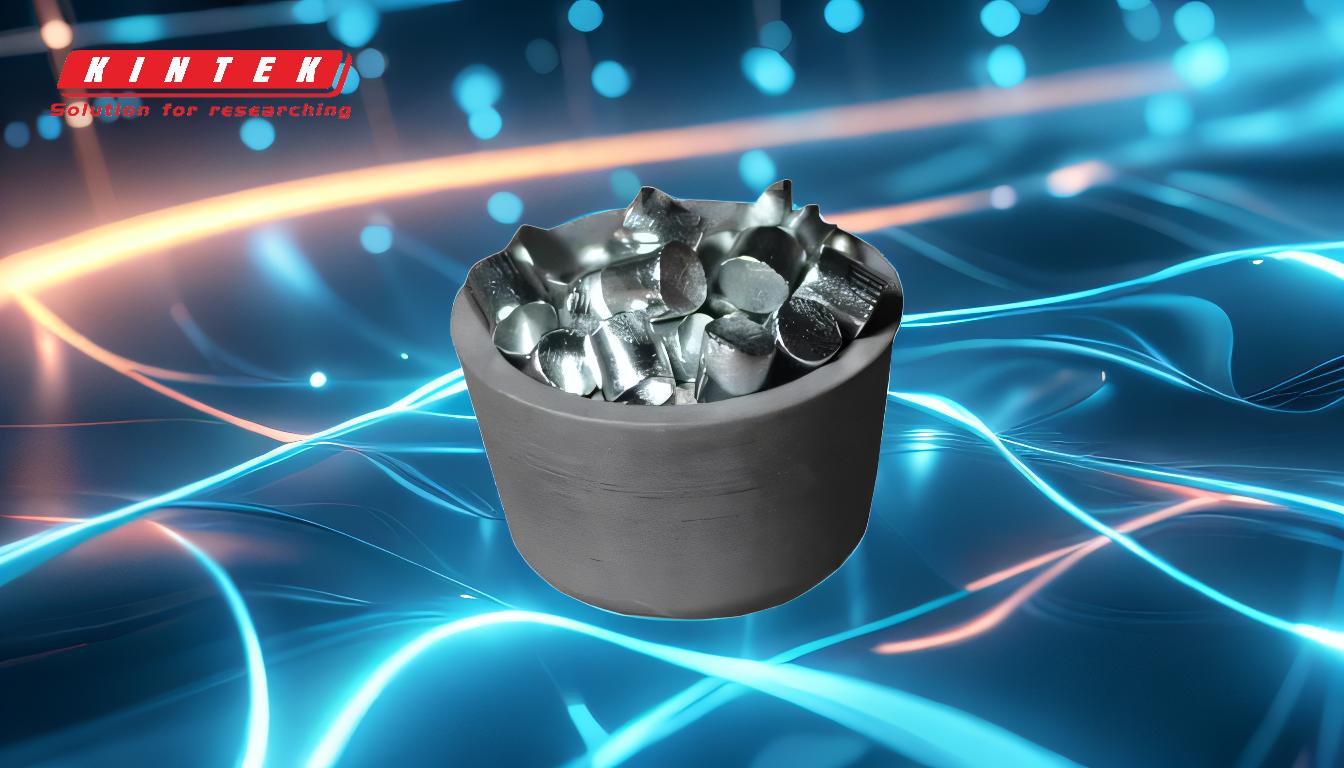
-
Impact on Film Quality and Density:
- Higher temperatures during thin film deposition generally lead to denser and higher-quality films. This is because elevated temperatures enhance surface reactions, allowing for better film composition and fewer defects.
- In PECVD, for example, higher temperatures (typically 250-400°C) result in films with lower hydrogen content and slower etch rates, which are indicators of higher quality.
- Lower temperatures, on the other hand, can lead to films that are more prone to defects such as pinholes, reducing their overall quality and performance.
-
Influence on Deposition Rate:
- While substrate temperature has little impact on the deposition rate, it significantly affects the quality of the film. This means that while the speed at which the film is deposited may not change much with temperature, the characteristics of the film (such as density and defect concentration) will be influenced.
- This distinction is crucial for optimizing the deposition process, as it allows for the adjustment of temperature to improve film quality without necessarily slowing down production.
-
Temperature Limits and Application Constraints:
- The application and substrate material often impose limits on the temperature that can be used during deposition. Higher temperatures may alter the film's properties or damage the substrate, making it essential to balance temperature with the specific requirements of the application.
- For instance, in PECVD, the highest temperature typically ranges between 350 to 400°C. Exceeding these limits could degrade the film or substrate, while staying within them ensures optimal film quality.
-
Historical Trends in Deposition Temperatures:
- Thin film deposition temperatures have decreased significantly over time, from over 1000°C in furnace-based processes to 250-350°C in modern PECVD processes. This reduction in temperature has been driven by the need to protect temperature-sensitive substrates and materials while still achieving high-quality films.
- Lower deposition temperatures also reduce energy consumption and operational costs, making the process more efficient and environmentally friendly.
-
Role of Temperature in Different Deposition Techniques:
- In evaporative deposition, for example, the temperature and pressure conditions during the process, along with the purity of the source material and substrate preparation, are critical factors affecting film quality. Proper control of these parameters, including temperature, is essential to achieve the desired film properties.
- In PECVD, temperature directly influences the chemical reactions occurring on the substrate surface, affecting the film's hydrogen content, etch rate, and overall quality.
-
Practical Considerations for Equipment and Consumable Purchasers:
- When selecting thin film deposition equipment, it is important to consider the temperature range and control capabilities of the system. Systems that offer precise temperature control within the desired range (e.g., 250-400°C for PECVD) are essential for producing high-quality films.
- Additionally, purchasers should consider the energy efficiency and operational costs associated with maintaining the required deposition temperatures, as these factors can significantly impact the overall cost-effectiveness of the process.
In summary, temperature is a critical parameter in thin film deposition, influencing film quality, density, and composition. While higher temperatures generally improve film quality, they must be balanced against the constraints imposed by the application and substrate material. Proper temperature control, along with consideration of other factors such as source material purity and substrate preparation, is essential for achieving high-quality thin films with desired properties.
Summary Table:
Aspect | Impact of Temperature |
---|---|
Film Quality & Density | Higher temperatures yield denser, higher-quality films with fewer defects. |
Deposition Rate | Temperature has minimal impact on deposition rate but significantly affects film quality. |
Temperature Limits | Application and substrate constraints dictate safe temperature ranges (e.g., 250-400°C). |
Historical Trends | Deposition temperatures have decreased from >1000°C to 250-350°C for efficiency. |
Deposition Techniques | Temperature influences chemical reactions in PECVD and evaporative deposition processes. |
Equipment Considerations | Precise temperature control is critical for achieving high-quality films. |
Need help optimizing your thin film deposition process? Contact our experts today for tailored solutions!