Resistance furnaces are specialized heating installations designed to generate and maintain high temperatures for various industrial and laboratory applications. They utilize the Joule effect, where electrical energy is converted into heat through resistors located on the furnace walls. This heat is then transferred to the workpiece primarily through radiation and convection. Resistance furnaces are widely used in fields such as ceramics, metallurgy, electronics, and materials science, offering precise temperature control and reliability for processes like sintering, annealing, and heat treatment.
Key Points Explained:
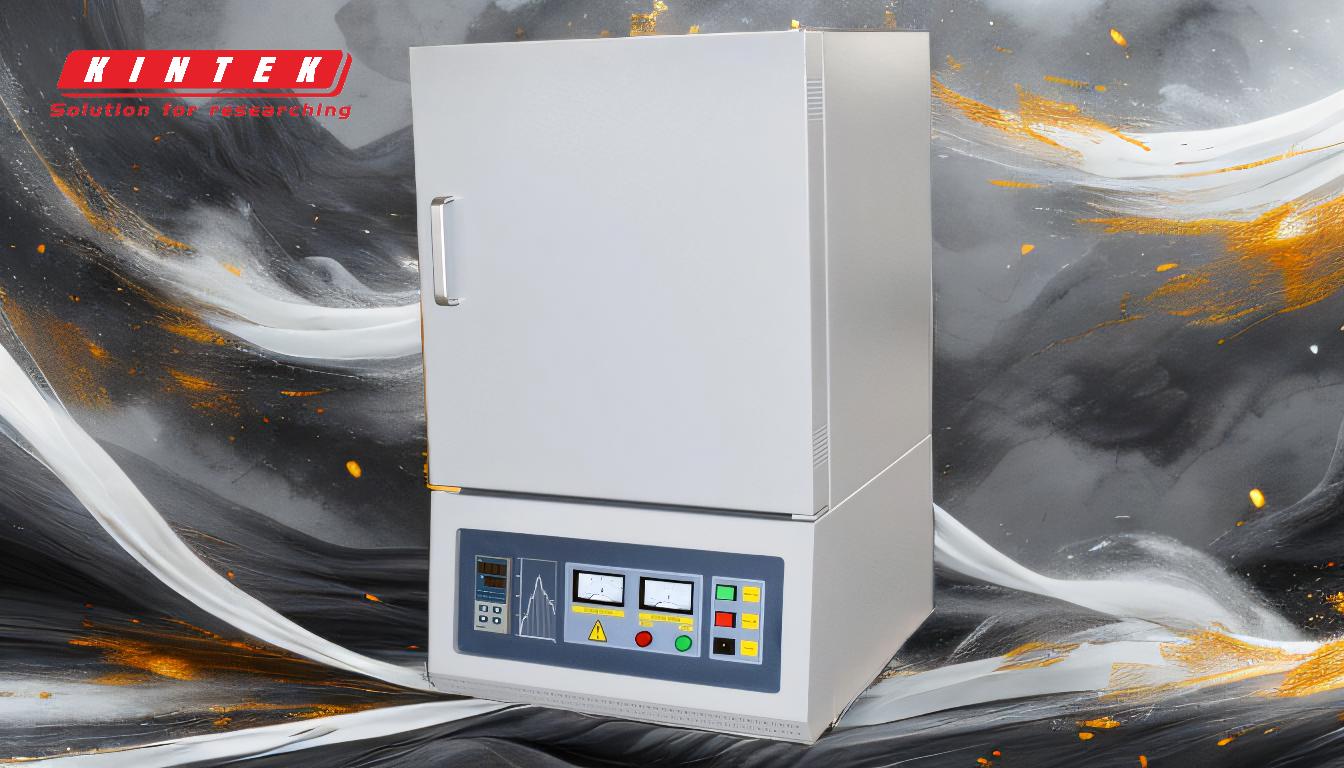
-
Principle of Operation:
- Resistance furnaces operate on the Joule effect, where electrical energy is converted into heat. This is achieved by passing an electric current through resistors, which are typically made of materials like nichrome or silicon carbide.
- The heat generated by these resistors is then transferred to the workpiece inside the furnace chamber, primarily through radiation and convection.
-
Types of Resistance Furnaces:
- Box Furnaces: These are versatile and can be used for a wide range of applications, including annealing, hardening, and stress relieving.
- Tube Furnaces: Designed for heating materials in a controlled atmosphere, often used in research and development.
- Muffle Furnaces: These have a separate chamber to isolate the material from combustion gases, making them ideal for processes requiring a clean environment.
-
Applications:
- Material Processing: Resistance furnaces are used for sintering, annealing, and heat treatment of materials such as metals, ceramics, and composites.
- Laboratory Research: They are essential in research labs for high-temperature experiments and material testing.
- Industrial Manufacturing: Used in industries like electronics, metallurgy, and ceramics for processes that require precise temperature control.
-
Advantages:
- Precision: Resistance furnaces offer excellent temperature control, making them suitable for processes that require specific thermal profiles.
- Versatility: They can be used for a wide range of applications, from simple heating to complex material processing.
- Reliability: These furnaces are known for their durability and consistent performance, even under high-temperature conditions.
-
Components:
- Heating Elements: Typically made of high-resistance materials like nichrome or silicon carbide, these elements are crucial for generating heat.
- Insulation: High-quality insulation materials are used to minimize heat loss and improve energy efficiency.
- Control Systems: Advanced control systems allow for precise temperature regulation and monitoring, ensuring optimal performance.
-
Maintenance and Safety:
- Regular maintenance is essential to ensure the longevity and efficiency of resistance furnaces. This includes checking the heating elements, insulation, and control systems.
- Safety precautions, such as proper ventilation and protective gear, are necessary when operating these furnaces to prevent accidents and ensure a safe working environment.
In summary, resistance furnaces are indispensable tools in both industrial and laboratory settings, offering precise temperature control and reliability for a wide range of high-temperature processes. Their versatility and efficiency make them a preferred choice for material processing, research, and manufacturing applications.
Summary Table:
Aspect | Details |
---|---|
Principle of Operation | Converts electrical energy into heat via resistors (Joule effect). |
Types | Box, Tube, and Muffle Furnaces for varied applications. |
Applications | Material processing, lab research, and industrial manufacturing. |
Advantages | Precision, versatility, and reliability in high-temperature processes. |
Key Components | Heating elements, insulation, and advanced control systems. |
Maintenance & Safety | Regular checks and safety precautions ensure efficiency and safe operation. |
Discover how resistance furnaces can optimize your processes—contact us today for expert advice!