The hardening process is a heat treatment technique used to increase the hardness and strength of metals, particularly steel. It involves heating the metal to a specific temperature, holding it at that temperature to allow structural changes, and then rapidly cooling it (quenching) to lock in the desired properties. This process alters the metal's microstructure, making it harder and more resistant to wear and deformation. However, hardening can also make the metal more brittle, so it is often followed by tempering to reduce brittleness while maintaining strength. The process is widely used in manufacturing tools, machinery parts, and other components that require high durability.
Key Points Explained:
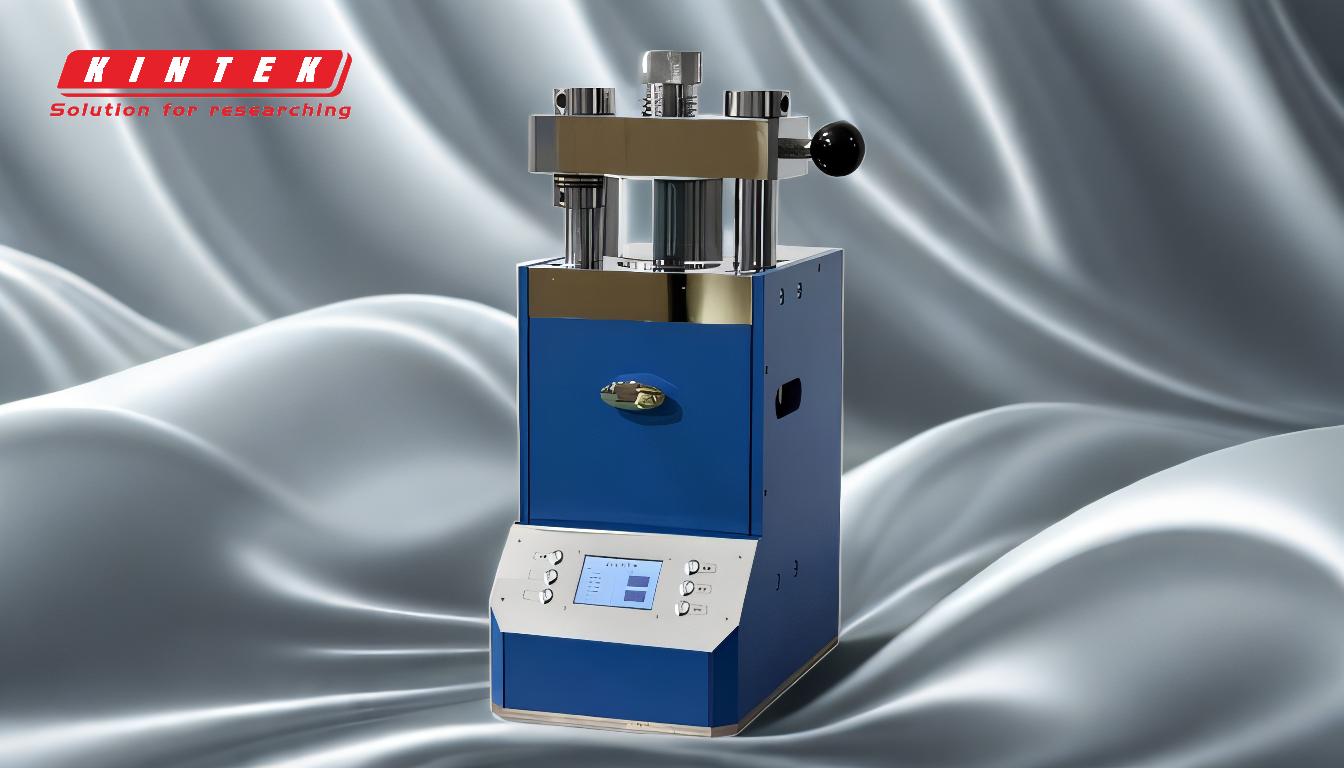
-
Purpose of Hardening:
- The primary goal of hardening is to increase the hardness and strength of metals, especially steel. This makes the material more resistant to wear, deformation, and mechanical stress. Hardening is essential for components that undergo high stress or friction, such as cutting tools, gears, and bearings.
-
Steps in the Hardening Process:
- Heating: The metal is heated to a specific temperature, known as the austenitizing temperature, which varies depending on the type of metal. For steel, this is typically between 800°C and 900°C.
- Holding: The metal is held at this temperature for a period to ensure uniform heating and allow the microstructure to transform into austenite, a high-temperature phase of steel.
- Quenching: The metal is rapidly cooled, usually by immersing it in water, oil, or air. This rapid cooling locks the austenite into a harder structure called martensite, which is responsible for the increased hardness.
-
Microstructural Changes:
- During heating, the metal's microstructure changes from ferrite and pearlite (soft phases) to austenite. Quenching transforms austenite into martensite, a very hard and brittle structure. This transformation is key to achieving the desired hardness.
-
Effects of Hardening:
- Increased Hardness: The metal becomes significantly harder, making it suitable for applications requiring high wear resistance.
- Increased Brittleness: While hardness improves, the metal may become more brittle, which can lead to cracking or failure under impact or stress.
-
Tempering:
- To address brittleness, hardened metals are often tempered. Tempering involves reheating the metal to a lower temperature (typically 150°C to 650°C) and then cooling it slowly. This process reduces brittleness while retaining much of the hardness and strength.
-
Applications of Hardening:
- Hardening is widely used in industries to manufacture tools (e.g., drills, knives), machinery parts (e.g., gears, shafts), and components that require high durability and resistance to wear.
-
Factors Affecting Hardening:
- Material Composition: The type and amount of alloying elements in the metal influence the hardening process.
- Quenching Medium: The choice of quenching medium (water, oil, or air) affects the cooling rate and final properties.
- Temperature Control: Precise control of heating and cooling temperatures is crucial to achieving the desired hardness and avoiding defects.
By understanding these key points, one can appreciate how the hardening process enhances the properties of metals, making them suitable for demanding applications.
Summary Table:
Key Aspect | Details |
---|---|
Purpose | Increases hardness and strength of metals, especially steel. |
Steps | 1. Heating to austenitizing temperature (800°C–900°C for steel). |
2. Holding to allow microstructure transformation. | |
3. Rapid cooling (quenching) to form martensite. | |
Microstructural Change | Transforms ferrite/pearlite to austenite, then martensite via quenching. |
Effects | - Increased hardness and wear resistance. |
- Increased brittleness (addressed by tempering). | |
Tempering | Reheating to 150°C–650°C to reduce brittleness while retaining strength. |
Applications | Tools (drills, knives), machinery parts (gears, shafts), and durable components. |
Factors | Material composition, quenching medium, and temperature control. |
Discover how the hardening process can enhance your metal components—contact our experts today for tailored solutions!