The heating rate during heat treatment is a critical factor that influences the final quality of the product. It is determined by several variables, including the material properties, part geometry, furnace design, and process requirements. The heating rate must be carefully controlled to ensure uniform temperature distribution, avoid thermal stresses, and achieve the desired metallurgical transformation. Factors such as the surface-to-mass ratio, furnace type, and part placement also play a significant role in determining the optimal heating rate. Understanding these factors helps in selecting the right equipment and process parameters to achieve consistent and high-quality results.
Key Points Explained:
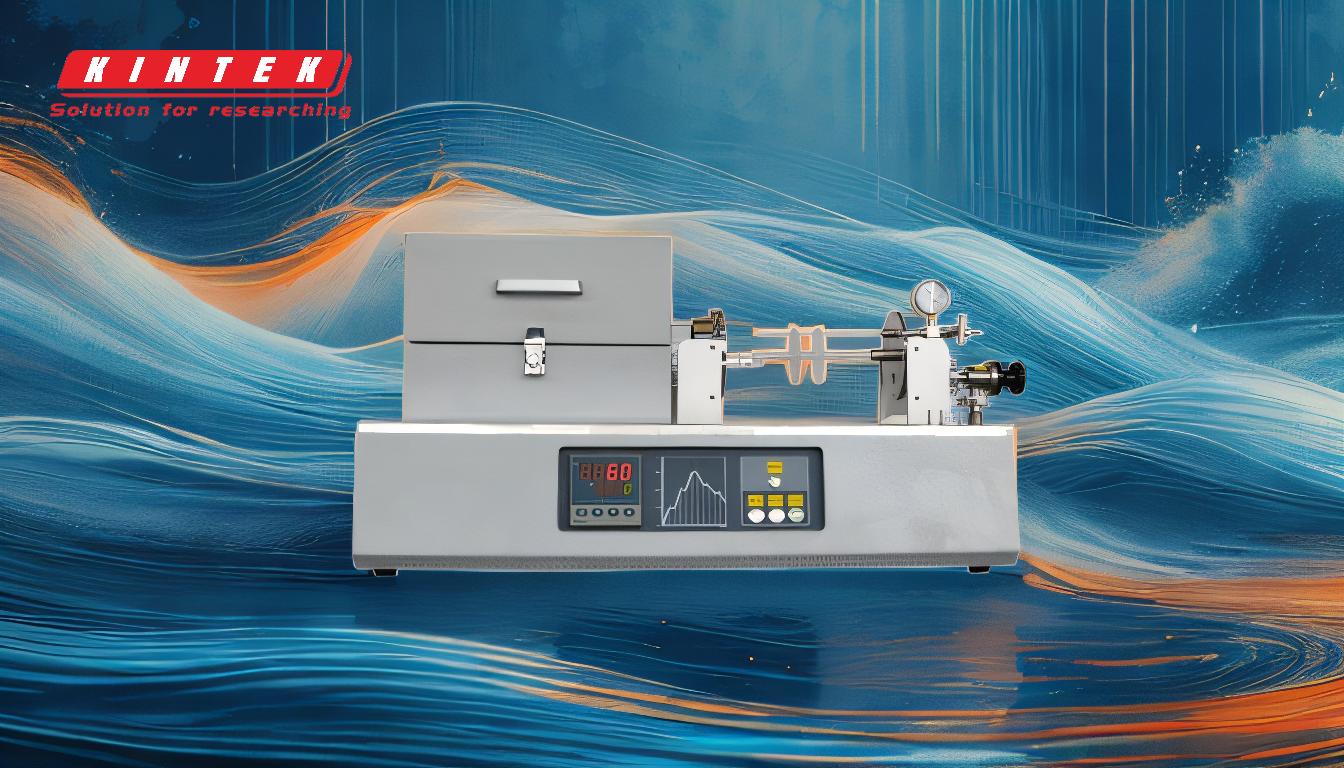
-
Definition of Heating Rate in Heat Treatment:
- The heating rate refers to how quickly a material or workpiece is heated to the desired temperature during the heat treatment process.
- It is typically measured in degrees Celsius per minute (°C/min) or degrees Fahrenheit per minute (°F/min).
-
Importance of Heating Rate:
- Uniform Temperature Distribution: A controlled heating rate ensures that the entire workpiece reaches the target temperature uniformly, preventing thermal gradients that can lead to distortion or cracking.
- Metallurgical Transformation: The rate at which a material is heated affects its microstructure and properties. For example, rapid heating may lead to incomplete transformation, while slow heating may cause excessive grain growth.
- Energy Efficiency: Optimizing the heating rate can reduce energy consumption and process time without compromising quality.
-
Factors Influencing Heating Rate:
-
Material Properties:
- Different materials have varying thermal conductivities and specific heat capacities, which affect how quickly they can absorb heat.
- For example, thin and large parts with a high surface-to-mass ratio heat up faster than thicker parts due to greater surface area for heat transfer.
-
Part Geometry and Surface Finish:
- Complex shapes or parts with varying cross-sections may require tailored heating rates to avoid uneven heating.
- Surface finish (e.g., polished vs. rough) can influence heat absorption and radiation.
-
Furnace Type and Design:
- In vacuum furnaces, heating rates are influenced by radiation and convection, while in rotary tube furnaces, factors like tube inclination and rotational speed play a role.
-
Furnace Loading:
- The arrangement and density of parts in the furnace affect heat distribution and the overall heating rate.
-
Process Requirements:
- Some heat treatment processes, such as annealing or hardening, may require specific heating rates to achieve the desired material properties.
-
Material Properties:
-
Practical Considerations for Equipment and Consumable Purchasers:
-
Furnace Selection:
- Choose a furnace with precise temperature control and adjustable heating rates to accommodate different materials and part geometries.
-
Monitoring and Control Systems:
- Invest in advanced control systems that allow for real-time monitoring and adjustment of heating rates.
-
Energy Efficiency:
- Consider furnaces with features like insulation and efficient heating elements to minimize energy consumption.
-
Maintenance and Downtime:
- Select equipment that is easy to maintain and has a low risk of downtime, ensuring consistent production quality.
-
Furnace Selection:
-
Examples of Heating Rates in Different Processes:
- Annealing: Typically involves slow heating rates to allow for uniform temperature distribution and stress relief.
- Hardening: May require faster heating rates to achieve the desired hardness, followed by controlled cooling.
- Vacuum Heat Treatment: Heating rates are often slower due to the reliance on radiation for heat transfer, but they can be optimized based on part geometry and material.
-
Challenges and Solutions:
-
Thermal Stress:
- Rapid heating can cause thermal stress, leading to part distortion or cracking. This can be mitigated by using controlled heating rates and preheating stages.
-
Inconsistent Results:
- Variations in heating rates can lead to inconsistent material properties. Implementing precise control systems and standardized processes can address this issue.
-
Equipment Limitations:
- Some furnaces may not be capable of achieving the required heating rates for specific materials or processes. In such cases, upgrading to more advanced equipment may be necessary.
-
Thermal Stress:
By understanding and optimizing the heating rate during heat treatment, manufacturers can achieve consistent product quality, reduce energy consumption, and minimize production downtime. This makes it a critical consideration for both equipment selection and process design.
Summary Table:
Key Factor | Impact on Heating Rate |
---|---|
Material Properties | Thermal conductivity and specific heat capacity affect heat absorption rates. |
Part Geometry | Complex shapes or varying cross-sections may require tailored heating rates. |
Furnace Type | Radiation, convection, and design (e.g., vacuum or rotary furnaces) influence heating. |
Furnace Loading | Part arrangement and density affect heat distribution and overall heating rate. |
Process Requirements | Annealing, hardening, or vacuum heat treatment may require specific heating rates. |
Ready to optimize your heat treatment process? Contact our experts today for tailored solutions!