Rapid quenching in water, while effective for hardening certain materials, can lead to significant disadvantages, particularly in terms of material integrity and performance. The primary disadvantage is the high risk of cracking or warping due to the extreme thermal stress caused by the rapid cooling process. This is especially critical for materials like fine ceramics, which are brittle and less tolerant of sudden temperature changes. Additionally, rapid quenching can result in uneven cooling, leading to internal stresses that may compromise the structural integrity of the part. These issues can be mitigated by using controlled cooling methods or alternative quenching media, but the trade-offs must be carefully considered based on the material and application.
Key Points Explained:
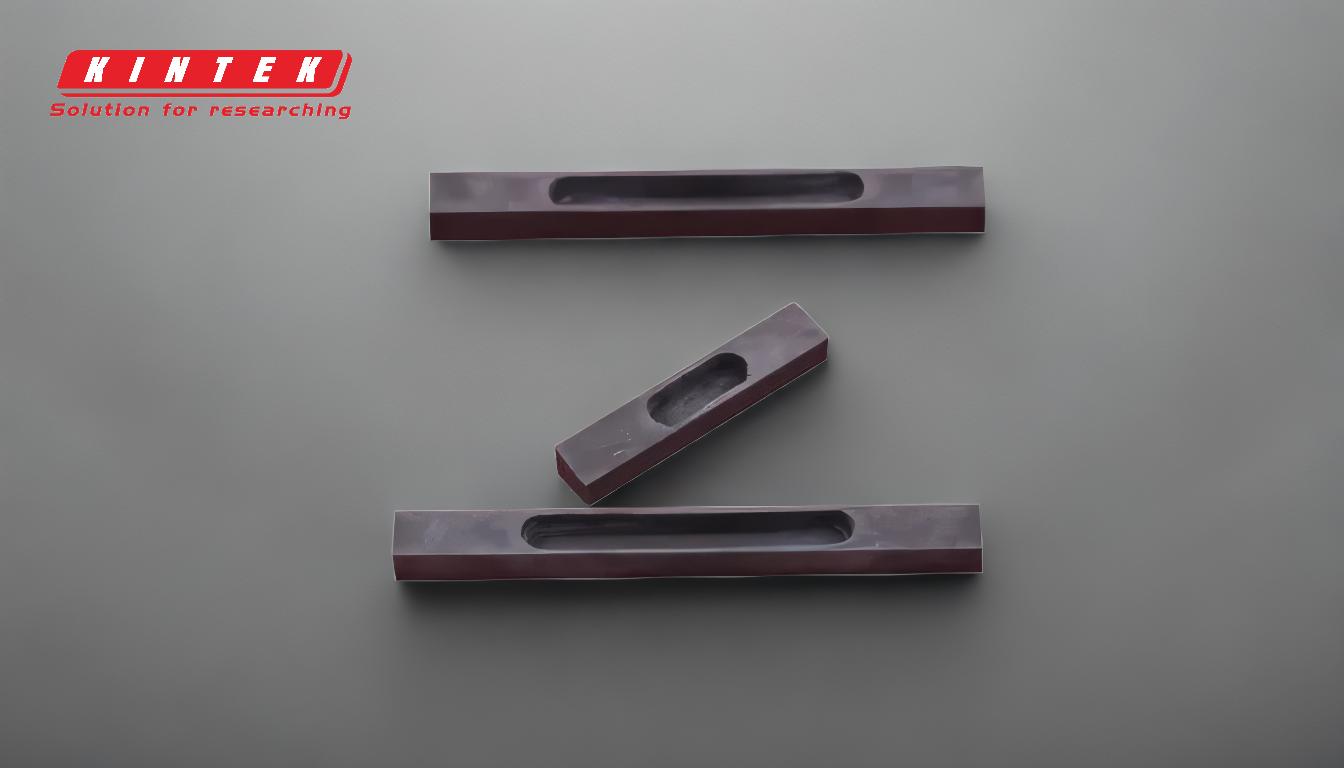
-
High Risk of Cracking or Warping:
- Rapid quenching in water causes extreme thermal stress, which can lead to cracking or warping of the part. This is particularly problematic for brittle materials like fine ceramics, which are less capable of withstanding sudden temperature changes.
- The rapid cooling process creates a steep temperature gradient within the material, leading to uneven contraction and expansion, which can result in structural failures.
-
Internal Stresses and Structural Integrity:
- Uneven cooling during rapid quenching can introduce internal stresses within the material. These stresses may not be immediately apparent but can compromise the long-term structural integrity of the part.
- Internal stresses can lead to premature failure, especially in parts subjected to cyclic loading or harsh operating conditions.
-
Material-Specific Challenges:
- Materials like fine ceramics are particularly susceptible to the disadvantages of rapid quenching due to their inherent brittleness and low thermal shock resistance.
- For such materials, alternative quenching methods or controlled cooling rates are often necessary to avoid damage.
-
Mitigation Strategies:
- To minimize the risks associated with rapid quenching, controlled cooling methods such as air cooling, oil quenching, or the use of specialized quenching media can be employed.
- Preheating the quenching medium or using stepped cooling processes can also help reduce thermal stress and improve the uniformity of cooling.
-
Application-Specific Considerations:
- The choice of quenching method should be tailored to the specific material and application. For instance, in applications where dimensional stability is critical, slower and more controlled cooling methods may be preferable.
- Understanding the thermal and mechanical properties of the material is essential for selecting the appropriate quenching process.
In summary, while rapid quenching in water can achieve desired hardness levels, the associated risks of cracking, warping, and internal stresses make it less suitable for certain materials and applications. Careful consideration of material properties and alternative quenching methods is essential to ensure the integrity and performance of the final product.
Summary Table:
Key Disadvantages | Description |
---|---|
Cracking or Warping | Extreme thermal stress from rapid cooling causes structural failures. |
Internal Stresses | Uneven cooling introduces stresses, compromising long-term structural integrity. |
Material-Specific Challenges | Brittle materials like fine ceramics are highly susceptible to damage. |
Mitigation Strategies | Use controlled cooling methods or alternative quenching media to reduce risks. |
Application-Specific Considerations | Tailor quenching methods to material properties and application requirements. |
Need help selecting the right quenching method for your materials? Contact our experts today for tailored solutions!