Physical Vapor Deposition (PVD) is a sophisticated method used to create thin film coatings on substrates by transferring material from a solid target to the substrate surface. The process involves converting the solid target material into a vapor phase, which then travels through a reaction chamber and condenses onto the substrate, forming a thin film. PVD is divided into sub-methods such as thermal evaporation and sputtering, each offering unique advantages for creating durable, corrosion-resistant, and high-temperature-tolerant coatings. The process is carried out in a controlled environment, often in a vacuum chamber, to ensure precise control over the thickness and quality of the deposited film.
Key Points Explained:
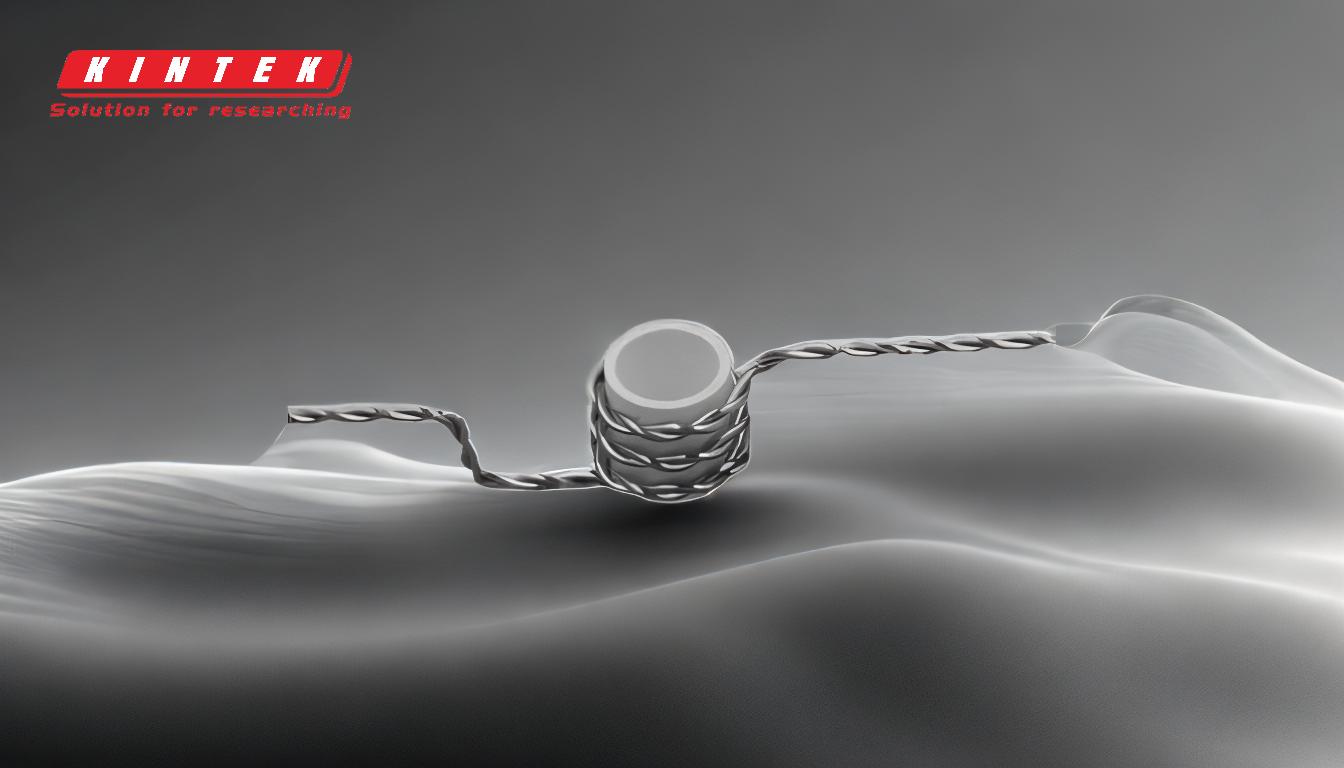
-
Definition and Purpose of PVD:
- PVD is a technique used to deposit thin films of material onto a substrate.
- The primary goal is to create coatings that are durable, corrosion-resistant, and capable of withstanding high temperatures.
-
Process Overview:
- Solid to Vapor Transition: The target material, which is initially in a solid state, is converted into a vapor phase. This can be achieved through methods such as thermal evaporation or sputtering.
- Vapor Transport: The vaporized material travels through a reaction chamber.
- Condensation: The vapor condenses onto the substrate, forming a thin film.
-
Sub-Methods of PVD:
- Thermal Evaporation: Involves heating the target material until it evaporates. The vapor then condenses onto the substrate.
- Sputtering: Involves bombarding the target material with high-energy particles, causing atoms to be ejected and deposited onto the substrate.
-
Environmental Control:
- Vacuum Chamber: The process is typically carried out in a vacuum to minimize contamination and control the deposition environment.
- Temperature Control: The chamber is maintained at temperatures ranging from 50 to 600 degrees Celsius, depending on the material and desired film properties.
-
Thickness and Morphology Control:
- Rate of Supply: The rate at which atoms are supplied to the deposition region affects the thickness and morphology of the film.
- Energy Removal: The rate at which energy is removed from the saturated atoms also plays a crucial role in determining the film's characteristics.
- Nucleation Rate: The rate at which recent nucleation is removed can influence the final film quality.
-
Equipment and Monitoring:
- Quartz Crystal Rate Monitor: Used to control the rate and thickness of the film deposition.
- Pumping-Down Chambers: These are used to reduce background gases, preventing them from chemically reacting with the intended film process.
-
Advantages of PVD:
- Good Adhesion: PVD films typically exhibit excellent adhesion to the substrate.
- High Melting Point Materials: PVD can handle materials with high melting points, making it versatile for various applications.
- Durability and Resistance: The coatings produced are highly durable and resistant to corrosion and high temperatures.
-
Applications:
- Industrial Coatings: Used for tools, molds, and machinery to enhance durability and performance.
- Electronics: Applied in the production of semiconductors and electronic components.
- Optics: Used to create reflective and anti-reflective coatings on lenses and mirrors.
By understanding these key points, one can appreciate the complexity and precision involved in the PVD process, making it a valuable technique in various industries requiring high-performance thin film coatings.
Summary Table:
Aspect | Details |
---|---|
Definition | PVD deposits thin films onto substrates via vapor-phase material transfer. |
Sub-Methods | Thermal evaporation, sputtering. |
Key Advantages | Durable, corrosion-resistant, high-temperature-tolerant coatings. |
Process Environment | Controlled vacuum chamber with precise temperature regulation. |
Applications | Industrial tools, electronics, optics. |
Discover how PVD can enhance your product performance—contact our experts today!