Operating a furnace, whether it's a muffle furnace, vacuum furnace, or hydrogen reduction furnace, requires strict adherence to safety precautions to prevent accidents, ensure equipment longevity, and maintain operational efficiency. Key precautions include avoiding overloading, maintaining proper cooling procedures, ensuring electrical safety, and keeping the furnace environment clean and free from hazards. Regular inspections, proper handling of materials, and adherence to operational limits are critical to safe and effective furnace use.
Key Points Explained:
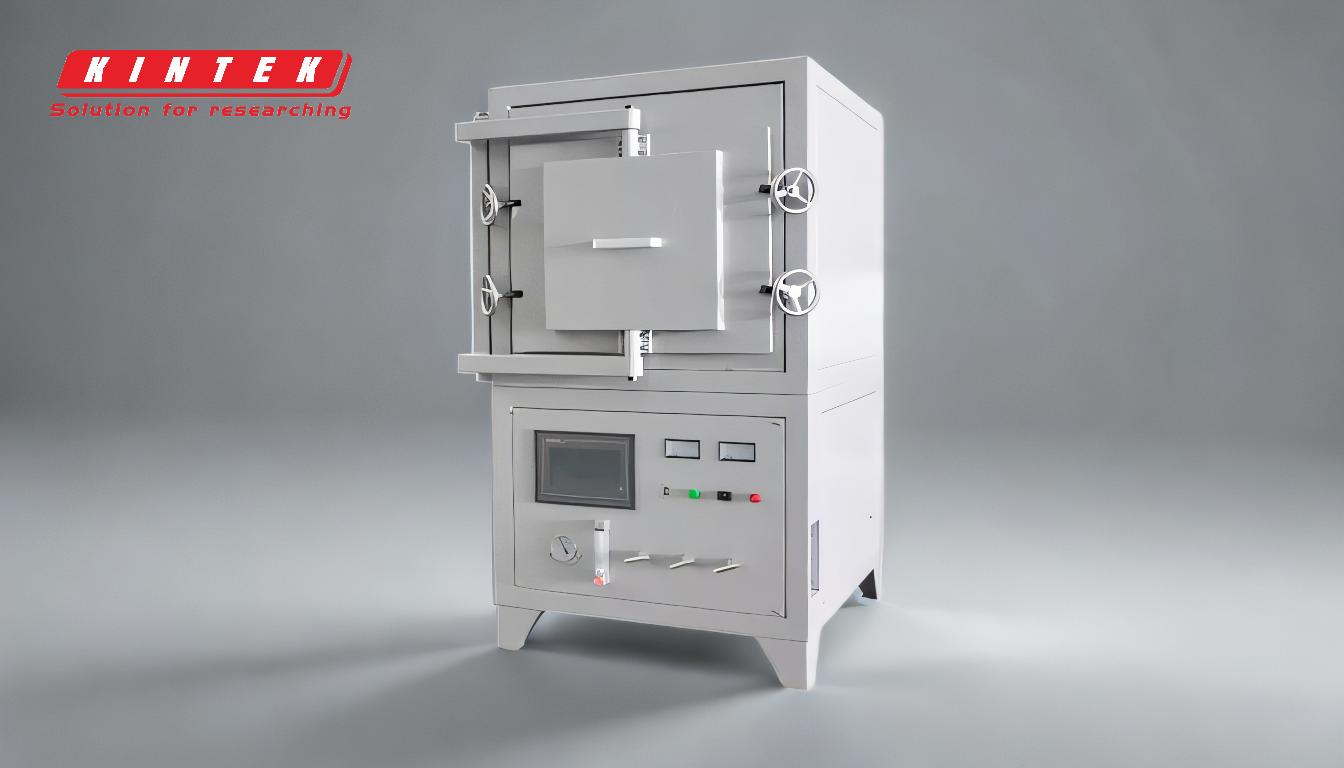
-
Avoid Overloading the Furnace:
- Never exceed the rated power or temperature of the furnace. Overloading can lead to equipment failure, overheating, or even fires.
- Operate the furnace below its maximum temperature (typically 50°C lower) to extend its lifespan and prevent damage to heating elements.
-
Proper Cooling Procedures:
- Allow the furnace to cool below 300°C before opening it to prevent thermal shock and burns.
- Avoid rapid cooling, especially in vacuum furnaces, as it can damage the furnace lining and components.
- For muffle furnaces, do not open the furnace door when the temperature exceeds 600°C to prevent heat-related injuries and equipment damage.
-
Electrical Safety:
- Regularly inspect electrical connections, wires, plugs, and components to ensure they are in good condition.
- Ensure the furnace and controller operate in environments with relative humidity below 85%, free from conductive dust, explosive gases, or corrosive gases.
- Always ground the furnace to prevent electrical hazards.
-
Material Handling:
- Avoid infusing the furnace with liquids or easily soluble metals, as they can damage the heating elements or create hazardous conditions.
- Use appropriate crucible clamps and handle samples carefully to prevent burns or damage to the furnace.
- For vacuum furnaces, use vacuum quenching oil with low saturated vapor pressure and avoid using nitrogen as a cooling gas when processing titanium alloys to prevent the formation of titanium nitride.
-
Environmental Precautions:
- Keep the furnace environment free from flammable, explosive, or corrosive substances.
- Ensure proper ventilation to prevent the buildup of harmful gases, especially in hydrogen reduction furnaces, where hydrogen leakage can lead to explosions.
- Do not place flammable materials inside or around the furnace.
-
Regular Maintenance and Cleaning:
- Clean the furnace regularly to remove debris, oxides, and other contaminants that could affect its performance.
- Inspect and maintain the furnace components, such as thermocouples, heating elements, and refractory linings, to ensure they function properly.
- Oven-dry the furnace before its first use or after long-term deactivation to remove moisture.
-
Operational Training and Procedures:
- Familiarize yourself with the furnace's operating procedures and safety guidelines.
- Wear appropriate protective equipment, such as heat-resistant gloves and safety goggles, when operating the furnace.
- Follow the recommended heating program and avoid private modifications to the furnace.
-
Emergency Preparedness:
- Have a rapid cooling device for vacuum tempering furnaces to handle emergencies.
- Turn off the power and close the furnace door when not in use to protect the refractory from moisture and other environmental factors.
- Stop using the furnace immediately in case of malfunction and address the issue before resuming operations.
By following these precautions, operators can minimize risks, ensure the safe operation of furnaces, and extend the lifespan of the equipment. Regular training, adherence to safety protocols, and proactive maintenance are essential for safe and efficient furnace use.
Summary Table:
Precaution | Key Details |
---|---|
Avoid Overloading | Operate below maximum temperature; prevent overheating and equipment failure. |
Proper Cooling Procedures | Cool below 300°C before opening; avoid rapid cooling in vacuum furnaces. |
Electrical Safety | Inspect connections; ensure humidity <85%; ground the furnace. |
Material Handling | Avoid liquids/soluble metals; use crucible clamps; handle samples carefully. |
Environmental Precautions | Keep flammable/corrosive substances away; ensure proper ventilation. |
Regular Maintenance | Clean regularly; inspect components; oven-dry before use. |
Operational Training | Follow safety guidelines; wear protective gear; avoid unauthorized modifications. |
Emergency Preparedness | Use rapid cooling devices; turn off power when not in use; address malfunctions. |
Ensure your furnace operates safely and efficiently—contact our experts today for personalized advice and support!