Electron beam deposition (EBD) is a physical vapor deposition (PVD) technique used to create thin films on substrates. The process involves generating a focused electron beam that heats and vaporizes a source material, which then condenses onto a substrate to form a thin, uniform coating. The method is highly precise, allowing for controlled deposition of materials like metals and ceramics. Key components include a high-vacuum environment, electron beam generation, and a crucible containing the source material. The process can be enhanced with ion beams to improve coating adhesion and density. EBD is widely used in industries requiring high-quality optical and reflective coatings.
Key Points Explained:
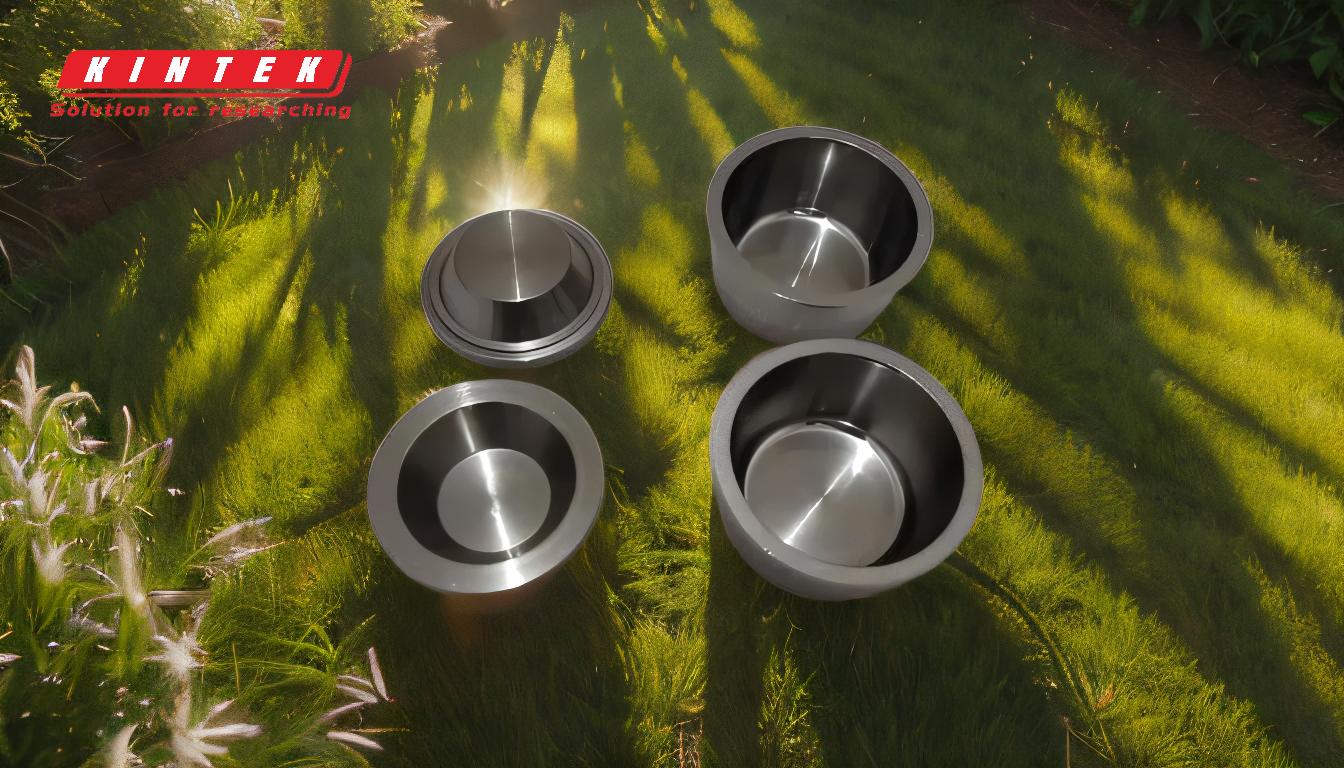
-
Principle of Electron Beam Generation:
- A magnet focuses electrons into a high-energy beam.
- The electron beam is directed toward a crucible containing the source material (e.g., metals or ceramics).
- The energy from the beam heats the material, causing it to evaporate or sublimate.
-
Material Vaporization:
- Metals (e.g., aluminum) typically melt before evaporating.
- Ceramics sublimate directly from solid to vapor.
- The vaporized material travels out of the crucible in a high-vacuum environment.
-
Deposition on Substrate:
- The vaporized material condenses onto the substrate, forming a thin film.
- The substrate's position, rotation, and temperature are precisely controlled to ensure uniform coating thickness.
-
High-Vacuum Environment:
- The process occurs in a vacuum chamber to prevent contamination and ensure efficient material transport.
- Vacuum conditions minimize interactions with air molecules, allowing for clean and precise deposition.
-
Enhancements with Ion Beam Assistance:
- An ion beam can be used to bombard the substrate during deposition.
- This increases adhesion energy, resulting in denser, more robust coatings with reduced internal stress.
-
Applications and Advantages:
- Used in industries requiring high-quality optical coatings, reflective surfaces, and thin films.
- Offers excellent control over coating thickness and uniformity.
- Suitable for depositing a wide range of materials, including metals, ceramics, and compounds.
-
Process Control and Automation:
- Precision computer control ensures consistent results by managing heating, vacuum levels, substrate positioning, and rotation.
- Automation allows for repeatable and scalable production of coatings with pre-specified properties.
By combining these elements, electron beam deposition provides a versatile and precise method for creating high-performance thin films, making it invaluable in advanced manufacturing and research applications.
Summary Table:
Key Aspect | Description |
---|---|
Principle | Electron beam heats and vaporizes source material in a high-vacuum environment. |
Material Vaporization | Metals melt before evaporating; ceramics sublimate directly. |
Deposition | Vaporized material condenses onto a substrate, forming a uniform thin film. |
High-Vacuum Environment | Ensures clean, precise deposition by minimizing contamination. |
Ion Beam Assistance | Enhances coating adhesion and density for robust, stress-free films. |
Applications | Optical coatings, reflective surfaces, and thin films for advanced industries. |
Process Control | Automated systems ensure consistent, repeatable, and scalable production. |
Discover how electron beam deposition can elevate your manufacturing process—contact our experts today!