Arc melting is a process used in metallurgy to melt metals using an electric arc, which is a high-temperature plasma generated by an electric current. The process involves creating an electric arc between an electrode and the metal to be melted, or between two electrodes. This arc generates intense heat, capable of melting metals like scrap steel without altering their chemical properties. The main component of an arc melting furnace is an electric welder, which converts standard voltage (220V or 380V) into low voltage and high current. The arc is initiated by a short circuit between the positive and negative poles and is self-sustaining, maintaining stable combustion until the process is complete.
Key Points Explained:
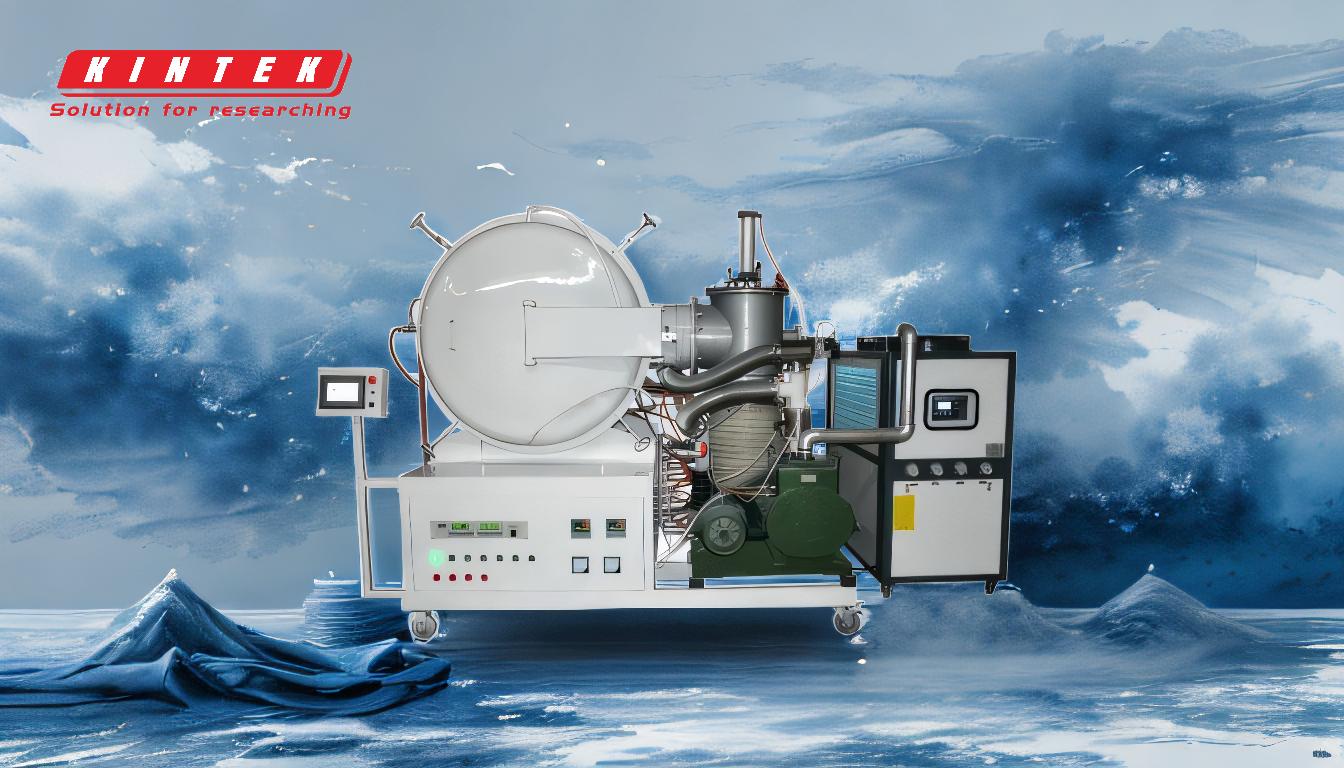
-
Definition and Purpose of Arc Melting:
- Arc melting is an electrothermal metallurgical method that uses electric energy to generate an electric arc.
- The primary purpose is to melt metals, such as scrap steel, without changing their chemical composition.
- This method is particularly useful in recycling and manufacturing industries where the integrity of the metal's properties must be preserved.
-
Components of an Arc Melting Furnace:
- Electric Welder: The core component that converts standard electrical voltage (220V or 380V) into low voltage and high current, necessary for generating the arc.
- Electrodes: These are the conductors through which the electric current passes to create the arc. They can be made of materials like graphite or tungsten, depending on the application.
- Furnace Chamber: The enclosed space where the metal is placed and melted. It is designed to withstand extreme temperatures and contain the molten metal.
-
Process of Generating the Electric Arc:
- Initiation: The arc is triggered by an instantaneous short circuit between the positive and negative poles of the electrode. This short circuit creates a plasma discharge, which is the electric arc.
- Sustaining the Arc: Once initiated, the arc is self-sustaining. It maintains stable combustion without extinguishing, thanks to the continuous flow of electric current.
- Heat Generation: The electric arc reaches extremely high temperatures, often exceeding 3000°C, which is sufficient to melt most metals.
-
Steps in the Arc Melting Process:
- Preparation: The metal to be melted is placed inside the furnace chamber. The electrodes are positioned appropriately to ensure efficient arc generation.
- Arc Initiation: The electric welder is activated, creating a short circuit between the electrodes or between an electrode and the metal, initiating the arc.
- Melting: The intense heat from the arc melts the metal. The molten metal is then collected or further processed as needed.
- Cooling and Solidification: Once the desired melting is achieved, the arc is turned off, and the molten metal is allowed to cool and solidify, either in molds or as part of a continuous casting process.
-
Applications of Arc Melting:
- Recycling: Arc melting is widely used in the recycling industry to melt scrap metal, allowing it to be reused in manufacturing processes.
- Alloy Production: The process is also used in the production of alloys, where precise control over the melting process is required to achieve specific material properties.
- Research and Development: In laboratories, arc melting is used to create small batches of specialized metals or alloys for experimental purposes.
-
Advantages of Arc Melting:
- High Efficiency: The process is highly efficient, with the ability to reach very high temperatures quickly.
- Precision: Arc melting allows for precise control over the melting process, which is crucial in applications where the chemical composition of the metal must remain unchanged.
- Versatility: It can be used with a wide range of metals and alloys, making it a versatile tool in metallurgy.
-
Safety Considerations:
- High Temperatures: The extreme heat generated by the arc requires robust safety measures, including protective gear for operators and proper insulation of the furnace.
- Electrical Hazards: Given the high currents involved, electrical safety is paramount. Proper grounding and insulation are essential to prevent accidents.
- Ventilation: The process can produce fumes and gases, so adequate ventilation is necessary to protect operators and the environment.
In summary, arc melting is a highly efficient and precise method for melting metals, widely used in industries ranging from recycling to advanced metallurgical research. The process relies on generating and maintaining an electric arc, which provides the necessary heat to melt metals without altering their chemical properties. Proper safety measures and equipment are essential to ensure the process is conducted safely and effectively.
Summary Table:
Aspect | Details |
---|---|
Definition | Electrothermal method using an electric arc to melt metals. |
Purpose | Melts metals like scrap steel without altering chemical properties. |
Key Components | Electric welder, electrodes, furnace chamber. |
Process | Arc initiation, sustaining, heat generation, melting, cooling. |
Applications | Recycling, alloy production, research and development. |
Advantages | High efficiency, precision, versatility. |
Safety Considerations | High temperatures, electrical hazards, ventilation. |
Discover how arc melting can revolutionize your metal processing—contact our experts today!