The vacuum coating process is a sophisticated method used to apply thin, protective layers of materials onto substrates, typically metals, in a controlled vacuum environment. This process is widely used in industries to enhance surface properties such as hardness, wear resistance, and corrosion resistance. The key steps include creating a vacuum, preparing the substrate, evaporating or sputtering the coating material, depositing it onto the substrate, and cooling the chamber. Vacuum coating technologies, such as Physical Vapor Deposition (PVD) and Chemical Vapor Deposition (CVD), are employed to achieve precise, nanoscale coatings with superior properties.
Key Points Explained:
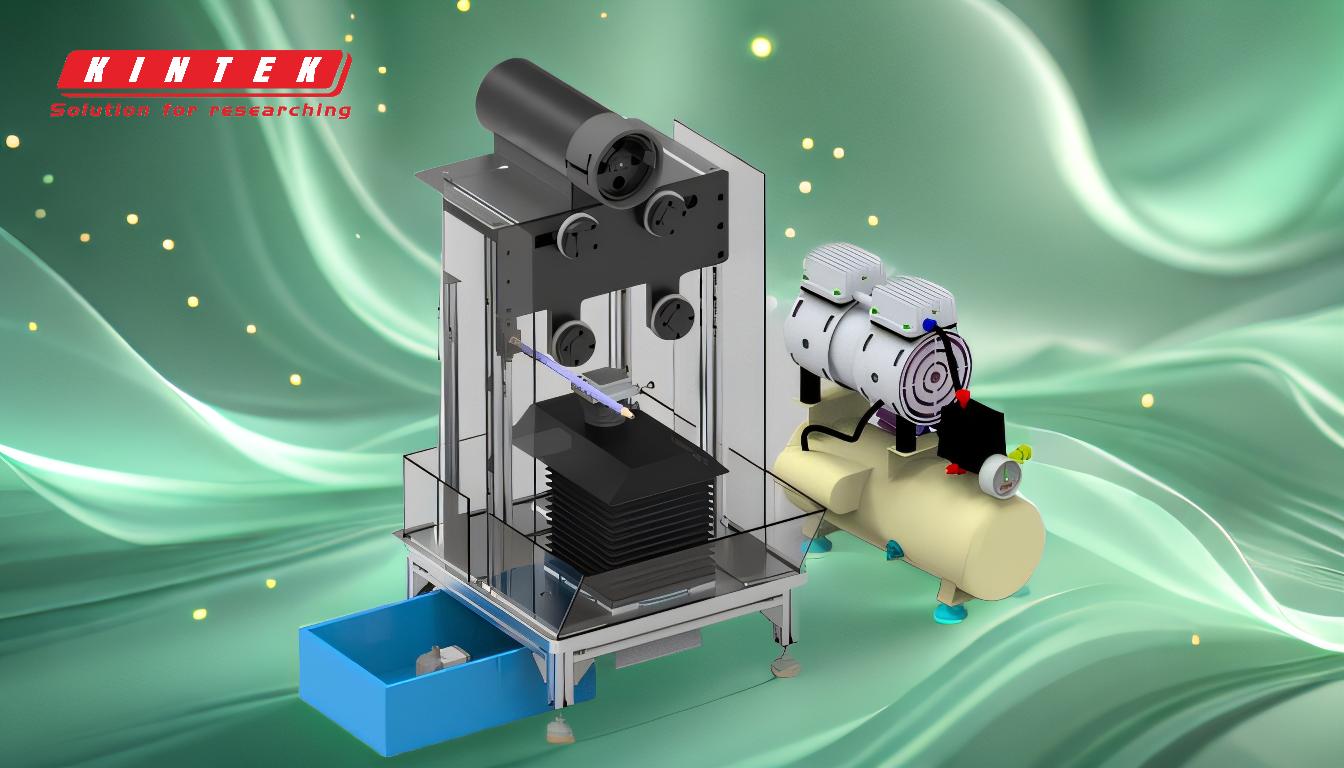
-
Creating a Vacuum Environment:
- The process begins by evacuating air and gases from the coating chamber to create a sub-atmospheric pressure environment. This step is crucial to prevent contamination and ensure the purity of the coating material.
- A vacuum environment eliminates interference from atmospheric gases, allowing for precise control over the deposition process.
-
Substrate Preparation:
- Before placing the substrate (the material to be coated) in the chamber, it undergoes thorough cleaning or surface treatment. This step ensures that the surface is free from contaminants, oils, or oxides that could hinder adhesion.
- Common cleaning methods include abrasive cleaning with liquids, ultrasonic cleaning, or plasma treatment.
-
Evaporation or Sputtering of Coating Material:
- The coating material, often a metal or ceramic, is vaporized or ionized within the vacuum chamber. This can be achieved through:
- Thermal Evaporation: The material is heated until it turns into vapor.
- Sputtering: High-energy ions bombard a target material, knocking off atoms that then deposit onto the substrate.
- These methods ensure the coating material is in a gaseous state, ready for deposition.
- The coating material, often a metal or ceramic, is vaporized or ionized within the vacuum chamber. This can be achieved through:
-
Deposition of Coating Material:
- The vaporized or ionized coating material is directed toward the substrate, where it condenses to form a thin, uniform layer.
- The deposition process is controlled to achieve precise thickness, often at the nanoscale, ensuring the desired properties of the coating.
-
Cooling and Venting:
- After the deposition is complete, the chamber is cooled to stabilize the newly formed coating.
- The chamber is then vented to return to atmospheric pressure, and the coated substrate is removed.
-
Types of Vacuum Coating Technologies:
- Physical Vapor Deposition (PVD): Involves physical processes like evaporation or sputtering to deposit materials. PVD is known for producing hard, wear-resistant coatings.
- Chemical Vapor Deposition (CVD): Uses chemical reactions to deposit materials, often resulting in high-purity coatings with excellent adhesion.
-
Applications and Benefits:
- Vacuum coating is used in industries such as aerospace, automotive, electronics, and medical devices to enhance surface properties.
- Benefits include improved hardness, wear resistance, corrosion resistance, and the ability to create coatings with specific optical or electrical properties.
By following these steps, the vacuum coating process ensures the creation of high-quality, durable coatings that meet the stringent requirements of modern industries.
Summary Table:
Step | Description |
---|---|
Creating a Vacuum | Evacuate air and gases to prevent contamination and ensure precise deposition. |
Substrate Preparation | Clean the substrate to remove contaminants and improve coating adhesion. |
Evaporation or Sputtering | Vaporize or ionize the coating material using thermal evaporation or sputtering. |
Deposition | Deposit the coating material onto the substrate in a controlled, uniform layer. |
Cooling and Venting | Cool the chamber and vent to stabilize the coating and remove the substrate. |
Technologies | PVD and CVD for hard, wear-resistant, and high-purity coatings. |
Applications | Aerospace, automotive, electronics, and medical devices for enhanced surfaces. |
Discover how vacuum coating can transform your materials—contact our experts today!