Calcination is a thermal treatment process used to achieve various objectives, primarily involving the removal of volatile impurities, decomposition of compounds, and oxidation of materials. It is widely applied in industries such as metallurgy, cement production, and material synthesis. The process involves heating materials to high temperatures in the presence of limited air or oxygen, typically below their melting points, to induce chemical or physical changes. Key purposes include removing water, volatile gases like carbon dioxide or sulfur dioxide, and oxidizing substances. Calcination is essential for producing materials like cement, refining metal ores, and synthesizing advanced materials such as zeolites.
Key Points Explained:
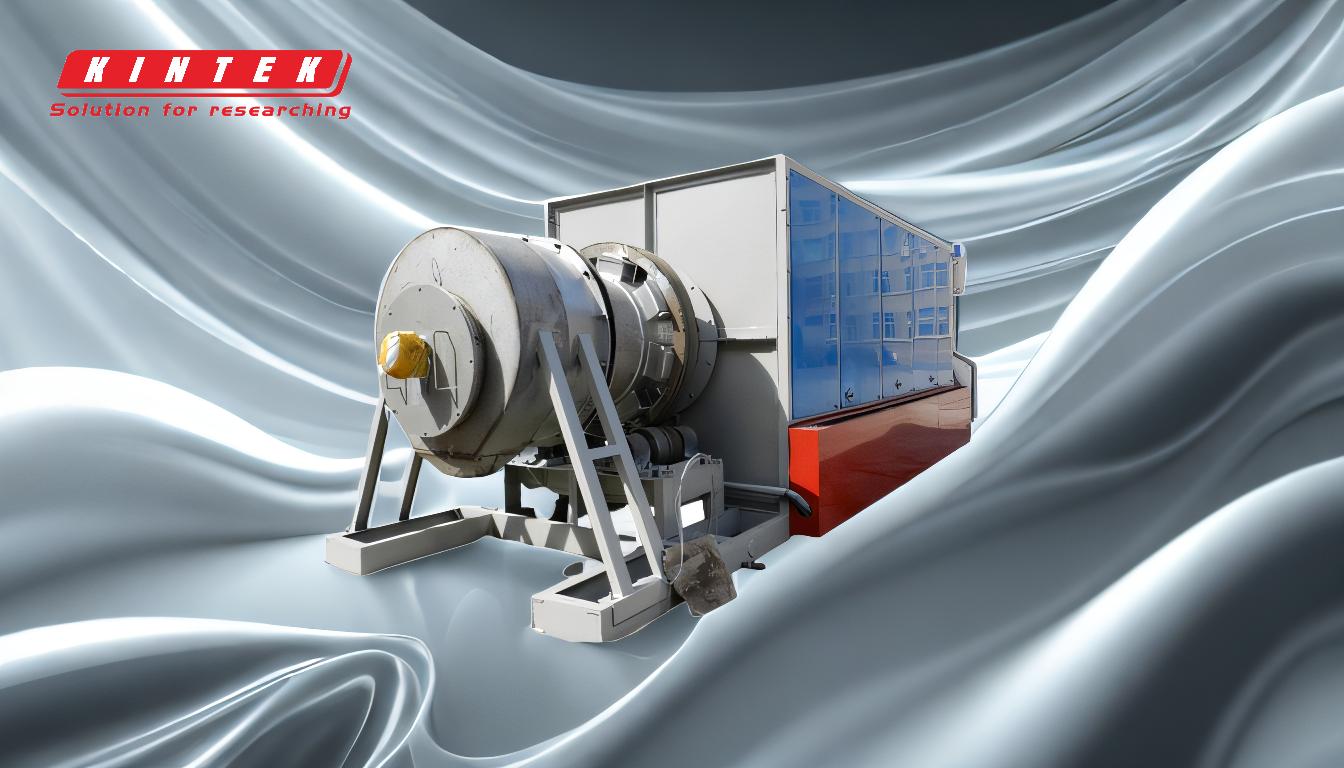
-
Removal of Volatile Impurities:
- Calcination is primarily used to eliminate volatile components from materials. For example, in metal ores, volatile impurities such as water, carbon dioxide, or sulfur dioxide are driven off during the process.
- This step is crucial for refining raw materials, as it enhances the purity and quality of the final product. For instance, in cement production, calcium carbonate decomposes into calcium oxide and carbon dioxide, leaving behind a purer material.
-
Thermal Decomposition:
- The process induces thermal decomposition, breaking down compounds into simpler substances. For example, calcium carbonate decomposes into calcium oxide and carbon dioxide when heated.
- This decomposition is essential in industries like cement manufacturing, where the chemical transformation of raw materials is necessary to achieve the desired product properties.
-
Oxidation of Materials:
- Calcination can also involve oxidizing part or all of a substance. This is particularly important in metallurgy, where metal ores are heated to remove impurities and convert them into oxides.
- Oxidation improves the material's reactivity and prepares it for further processing, such as reduction in smelting operations.
-
Applications in Cement Production:
- One of the most common uses of calcination is in the production of cement. The process involves heating limestone (calcium carbonate) to produce lime (calcium oxide), a key ingredient in cement.
- This step is critical for achieving the chemical composition required for cement to harden and gain strength.
-
Synthesis of Advanced Materials:
- Calcination is used in the synthesis of advanced materials like zeolites, where it helps remove ammonium ions and stabilize the material's structure.
- It is also employed in the devitrification of glass, where it induces phase transformations to improve the material's properties.
-
Removal of Absorbed Moisture:
- Calcination effectively removes absorbed moisture from materials, which is essential for ensuring the stability and performance of products in various applications.
- This is particularly important in industries where moisture can negatively impact the material's properties or processing.
-
Industrial Relevance:
- The process is widely used across industries, including metallurgy, ceramics, and chemical manufacturing, due to its versatility and effectiveness in achieving specific material transformations.
- Its ability to refine raw materials and produce high-quality end products makes it indispensable in modern industrial processes.
In summary, calcination serves as a critical thermal treatment process for refining materials, removing impurities, and inducing chemical transformations. Its applications span multiple industries, making it a cornerstone of material processing and synthesis.
Summary Table:
Key Aspect | Description |
---|---|
Removal of Volatile Impurities | Eliminates water, CO₂, and SO₂ to enhance material purity. |
Thermal Decomposition | Breaks down compounds (e.g., CaCO₃ → CaO + CO₂) for industrial applications. |
Oxidation of Materials | Converts metal ores into oxides, improving reactivity for further processing. |
Cement Production | Heats limestone to produce lime, a critical ingredient in cement manufacturing. |
Advanced Material Synthesis | Used in creating zeolites and improving glass properties through phase changes. |
Moisture Removal | Removes absorbed moisture to ensure material stability and performance. |
Industrial Relevance | Widely applied in metallurgy, ceramics, and chemical manufacturing for material refinement. |
Learn how calcination can optimize your industrial processes—contact our experts today!