Sintering is a critical process in materials science, particularly in the production of ceramics, metals, and composites. The role of pressure in sintering is multifaceted, influencing the densification, grain growth, and overall mechanical properties of the final product. Pressure, often applied in conjunction with heat in a sintering furnace, helps to reduce porosity, enhance particle bonding, and achieve the desired material characteristics. This process is essential for creating high-performance materials used in various industries, including aerospace, automotive, and electronics.
Key Points Explained:
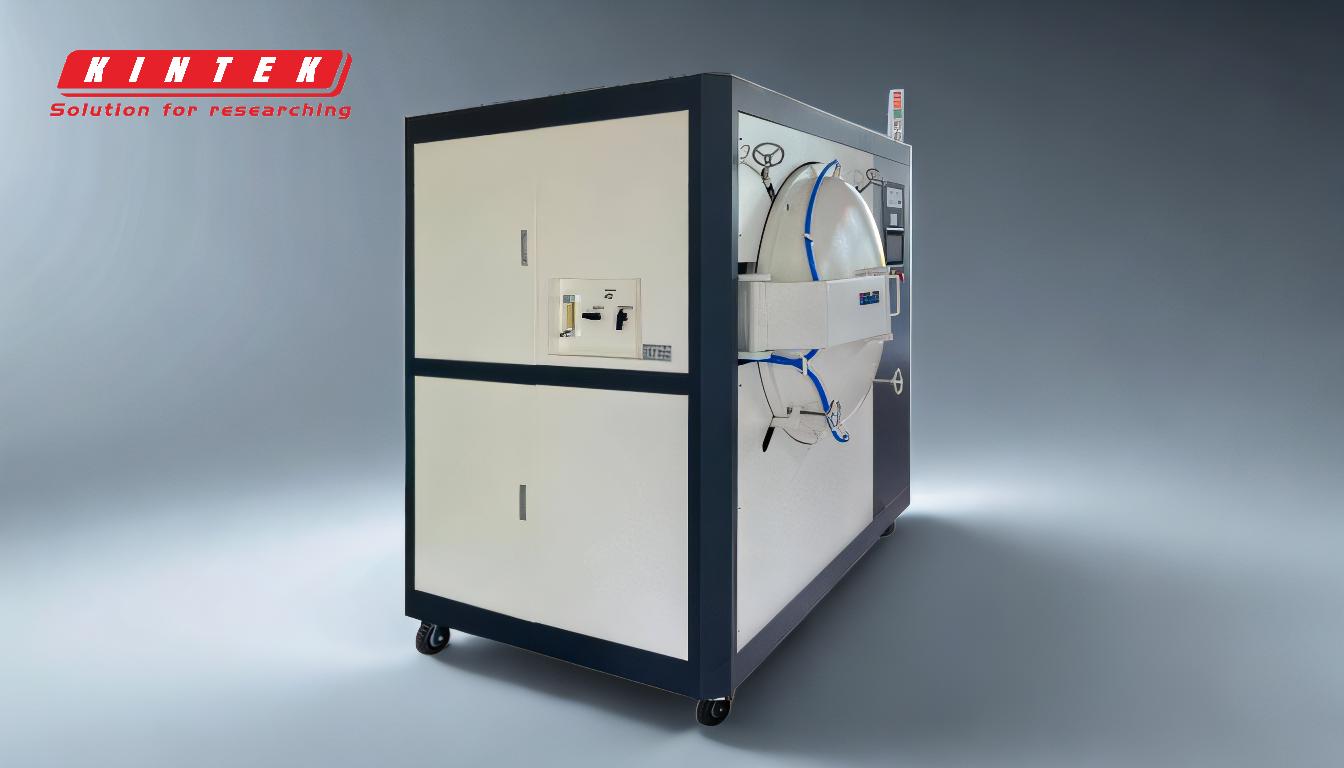
-
Enhancement of Densification:
- Pressure plays a crucial role in reducing the porosity of the material during sintering. By applying external pressure, the particles are forced into closer contact, which facilitates the diffusion process and promotes densification.
- This is particularly important in the production of high-density materials where low porosity is essential for mechanical strength and durability.
-
Acceleration of Particle Bonding:
- The application of pressure in a sintering furnace helps to accelerate the bonding between particles. This is achieved by increasing the contact area between particles, which enhances the diffusion of atoms across particle boundaries.
- As a result, the material achieves better mechanical properties, such as higher strength and toughness.
-
Control of Grain Growth:
- Pressure can influence the grain growth during sintering. By controlling the pressure, it is possible to manage the size and distribution of grains within the material, which directly affects its mechanical and thermal properties.
- Proper control of grain growth is essential for achieving the desired material performance, especially in applications requiring high thermal and mechanical stability.
-
Reduction of Sintering Temperature:
- The application of pressure can reduce the required sintering temperature. This is because pressure lowers the activation energy needed for diffusion, allowing the sintering process to occur at lower temperatures.
- Lower sintering temperatures can lead to energy savings and reduce the risk of undesirable phase transformations or material degradation.
-
Improvement of Material Properties:
- Pressure-assisted sintering can significantly improve the mechanical properties of the final product. This includes increased hardness, wear resistance, and fatigue strength.
- These improvements are critical for materials used in demanding applications, such as cutting tools, bearings, and structural components.
-
Role of Sintering Furnace:
- The sintering furnace is essential for applying the necessary heat and pressure during the sintering process. It provides a controlled environment where temperature and pressure can be precisely regulated to achieve the desired material properties.
- Modern sintering furnaces are equipped with advanced features that allow for precise control over the sintering atmosphere, temperature, and pressure, ensuring consistent and high-quality results.
In summary, pressure is a vital factor in the sintering process, influencing densification, particle bonding, grain growth, and overall material properties. The sintering furnace plays a critical role in applying and controlling these parameters, ensuring the production of high-performance materials tailored to specific industrial applications. For more detailed information on sintering furnaces, you can refer to this resource: sintering furnace.
Summary Table:
Role of Pressure in Sintering | Key Benefits |
---|---|
Enhancement of Densification | Reduces porosity, improves mechanical strength |
Acceleration of Particle Bonding | Increases contact area, enhances strength and toughness |
Control of Grain Growth | Manages grain size, improves thermal and mechanical stability |
Reduction of Sintering Temperature | Lowers energy use, prevents material degradation |
Improvement of Material Properties | Boosts hardness, wear resistance, and fatigue strength |
Role of Sintering Furnace | Provides precise control of heat and pressure for consistent results |
Ready to optimize your sintering process? Contact our experts today to learn more!