The sintering process of coating involves heating the material, typically a powder, to a temperature below its melting point to facilitate particle bonding and densification, resulting in a cohesive and durable coating. This process is widely used in various industries to create protective or functional coatings on components. The key steps include powder preparation, compaction, heating, and cooling, with specific techniques like liquid phase sintering or vacuum sintering employed depending on the material and application. The process ensures the formation of a uniform, dense, and mechanically robust coating.
Key Points Explained:
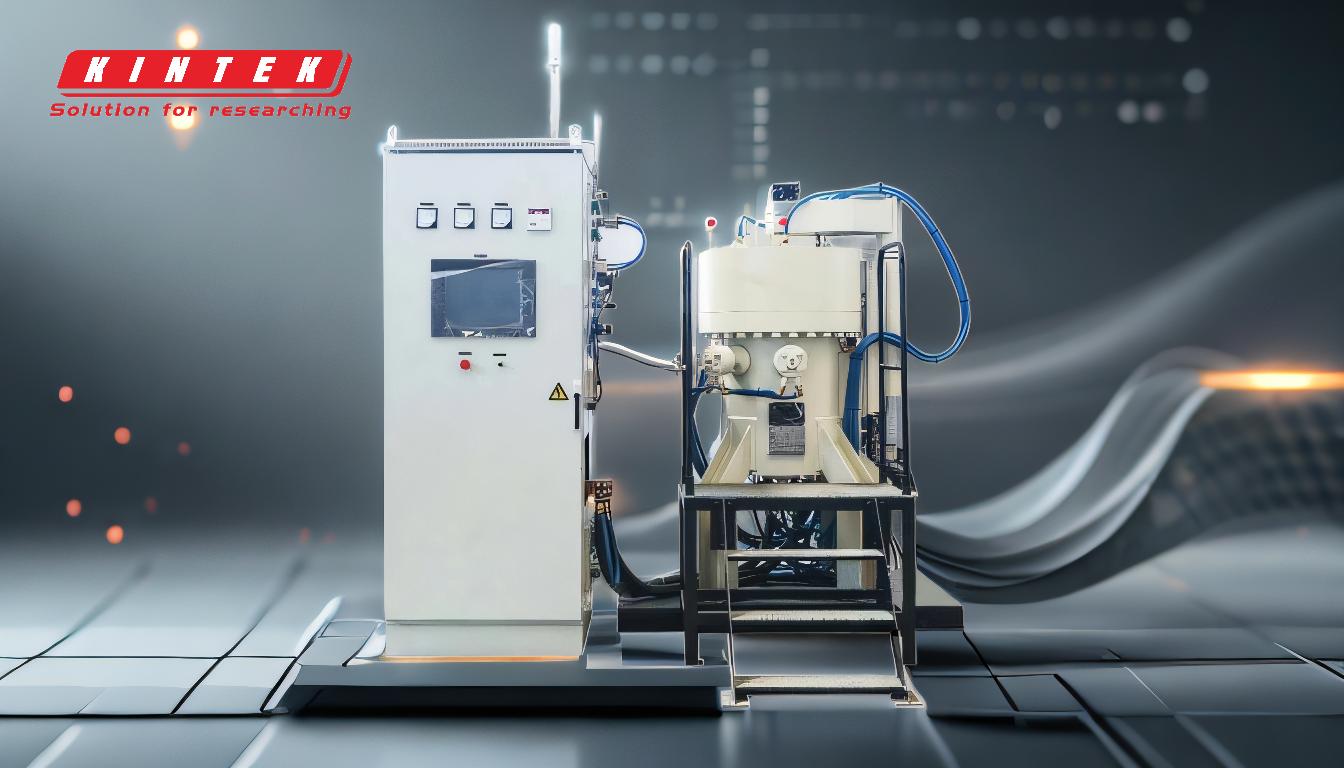
-
Preparation of Powder or Material:
- The process begins with the preparation of the material, often in powder form. This powder can be a single metal, alloy, or composite material.
- The powder may be mixed with additives, binders, or alloying elements to enhance properties like strength, wear resistance, or thermal conductivity.
- For coatings, the powder is applied to the substrate using methods like spraying, dipping, or electrostatic deposition.
-
Compaction:
- After application, the powder is compacted to ensure uniformity and eliminate voids. This can be done using mechanical pressure, pressing tools, or atmospheric pressure in a controlled environment.
- Compaction helps in achieving the desired shape and density of the coating, ensuring it adheres well to the substrate.
-
Heating and Sintering:
- The compacted material is then heated in a sintering furnace to a temperature just below its melting point. This temperature is critical as it allows particles to bond without causing complete melting.
- During heating, particles undergo diffusion, leading to neck formation and densification. This stage is crucial for achieving the desired mechanical properties and reducing porosity.
- Techniques like liquid phase sintering (LPS) or vacuum sintering may be used to accelerate particle bonding and improve the quality of the coating.
-
Cooling and Solidification:
- After sintering, the material is cooled gradually to allow it to solidify into a rigid and cohesive structure.
- Controlled cooling prevents cracking or warping and ensures the coating retains its desired properties.
-
Post-Processing:
- Depending on the application, the sintered coating may undergo additional post-processing steps such as machining, polishing, or surface treatment to enhance its performance or appearance.
-
Applications and Benefits:
- The sintering process is widely used in industries like automotive, aerospace, and electronics to create coatings that provide corrosion resistance, thermal insulation, or electrical conductivity.
- The process offers benefits such as high material utilization, the ability to create complex shapes, and the production of coatings with excellent mechanical properties.
By following these steps, the sintering process ensures the creation of high-quality coatings that meet the stringent requirements of modern industrial applications.
Summary Table:
Step | Description |
---|---|
Powder Preparation | Prepare material in powder form, often mixed with additives for enhanced properties. |
Compaction | Compact powder to ensure uniformity and eliminate voids for better adhesion. |
Heating & Sintering | Heat material below melting point to bond particles, using techniques like LPS. |
Cooling | Cool gradually to solidify the coating and prevent cracking or warping. |
Post-Processing | Apply additional treatments like machining or polishing for enhanced performance. |
Applications | Used in automotive, aerospace, and electronics for corrosion resistance, etc. |
Discover how sintering can enhance your coatings—contact our experts today for tailored solutions!