Hot forging is a metalworking process that involves shaping metal at high temperatures, typically above its recrystallization temperature. This process allows the metal to deform plastically without increasing its strength, making it easier to shape. The temperature range for hot forging varies depending on the type of metal being forged, but it generally falls between 950°C to 1250°C for most steels. The exact temperature is crucial as it affects the metal's flow properties, grain structure, and final mechanical properties. Hot forging is widely used in industries such as automotive, aerospace, and construction due to its ability to produce strong, durable components with complex shapes.
Key Points Explained:
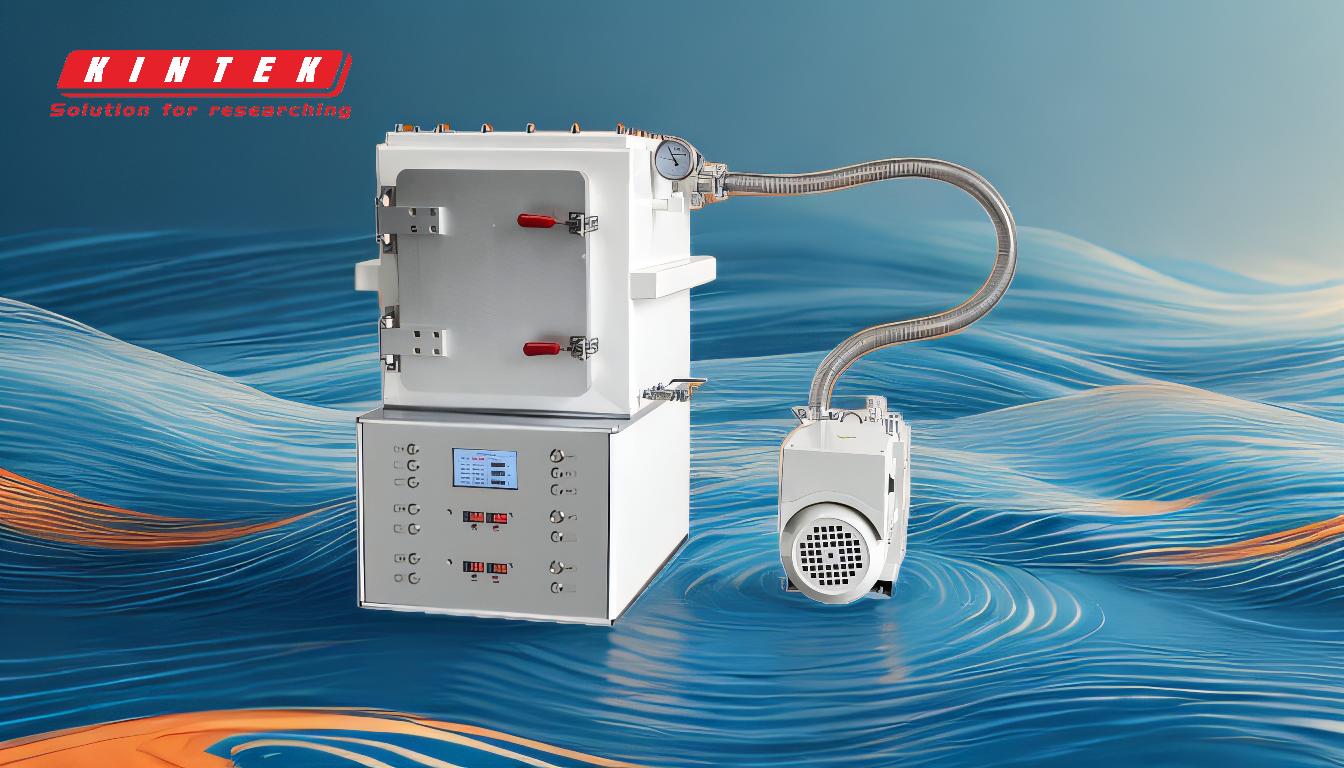
-
Definition of Hot Forging:
- Hot forging is a manufacturing process where metal is heated to a temperature above its recrystallization point and then shaped using compressive forces. This high-temperature environment allows the metal to be more malleable, reducing the risk of cracking or other defects during the forging process.
-
Temperature Range for Hot Forging:
- The temperature for hot forging typically ranges from 950°C to 1250°C for most steels. This range ensures that the metal remains in a plastic state, allowing it to be easily deformed without breaking. The exact temperature depends on the specific alloy being forged, as different metals have different recrystallization temperatures.
-
Importance of Temperature Control:
- Maintaining the correct temperature is critical in hot forging. If the temperature is too low, the metal will not deform properly and may develop cracks. If the temperature is too high, the metal may become too soft, leading to dimensional inaccuracies and a weakened final product. Precise temperature control ensures optimal material flow and desired mechanical properties.
-
Recrystallization Temperature:
- The recrystallization temperature is the point at which the metal's internal grain structure begins to reform, eliminating work hardening and making the metal more ductile. For most steels, this temperature is around 0.5 to 0.6 times the melting point in Kelvin. This is why hot forging is performed at temperatures well above this threshold.
-
Types of Metals Commonly Forged:
- Hot forging is commonly used for metals such as carbon steel, alloy steel, stainless steel, and some non-ferrous metals like aluminum and titanium. Each metal has a specific temperature range for optimal forging, which is determined by its chemical composition and physical properties.
-
Advantages of Hot Forging:
- Hot forging offers several advantages, including improved mechanical properties, better surface finish, and the ability to produce complex shapes. The process also refines the grain structure of the metal, enhancing its strength and durability. Additionally, hot forging reduces the need for secondary machining operations, saving time and costs.
-
Applications of Hot Forging:
- Hot forging is widely used in industries that require high-strength components, such as automotive (e.g., crankshafts, connecting rods), aerospace (e.g., turbine blades, landing gear), and construction (e.g., bolts, fasteners). The process is also used in the production of tools, machinery parts, and heavy equipment.
-
Equipment Used in Hot Forging:
- Hot forging requires specialized equipment, including furnaces for heating the metal, forging presses or hammers for shaping, and dies to form the desired shape. The furnace must be capable of reaching and maintaining the high temperatures required for the process.
-
Challenges in Hot Forging:
- One of the main challenges in hot forging is managing the high temperatures, which can lead to issues such as oxidation, scaling, and thermal fatigue. Proper lubrication and die design are essential to minimize these problems and ensure a successful forging process.
-
Future Trends in Hot Forging:
- Advances in technology are leading to more efficient and precise hot forging processes. Innovations such as computer-controlled forging presses, advanced die materials, and improved heating techniques are helping to reduce costs and improve the quality of forged components. Additionally, there is a growing focus on sustainability, with efforts to reduce energy consumption and waste in the forging process.
In summary, hot forging is a critical process in metalworking that relies on precise temperature control to produce high-strength, durable components. The temperature range for hot forging is typically between 950°C to 1250°C, depending on the metal being forged. Understanding the principles and challenges of hot forging is essential for producing high-quality components in various industries.
Summary Table:
Aspect | Details |
---|---|
Temperature Range | 950°C to 1250°C for most steels |
Key Metals | Carbon steel, alloy steel, stainless steel, aluminum, titanium |
Importance | Ensures plastic deformation, prevents cracking, and enhances grain structure |
Applications | Automotive, aerospace, construction, machinery parts |
Equipment | Furnaces, forging presses, hammers, dies |
Challenges | Oxidation, scaling, thermal fatigue, precise temperature control |
Interested in optimizing your hot forging process? Contact us today for expert guidance!