The traditional sintering process is a thermal treatment method used to fuse materials, such as zirconia, into a solid mass without melting them. This process involves heating the material to a high temperature, allowing particles to bond through densification and intergranular neck growth, which reduces porosity and increases density. The result is a strong, dense final product with improved mechanical properties. A zirconia sintering furnace is essential for this process, as it provides precise temperature control, even heat distribution, and efficient air circulation to achieve the desired properties of the sintered zirconia. The process typically includes heating, sintering, and cooling phases, ensuring the material reaches its final hardness and structural integrity.
Key Points Explained:
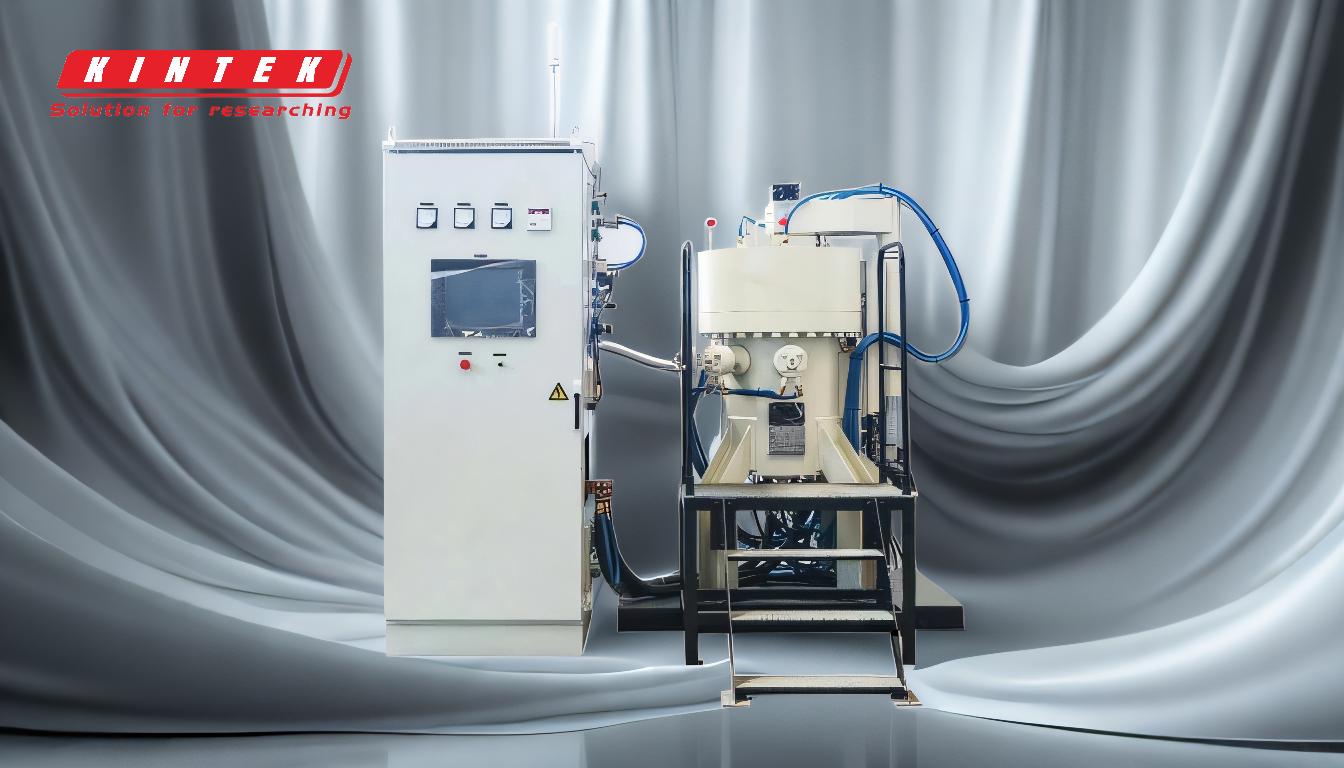
-
Definition of Traditional Sintering:
- Traditional sintering is a process where materials, such as zirconia, are fused together using heat without reaching a liquid state. This method relies on thermal treatment and sometimes pressurization to achieve densification and intergranular neck growth, which enhances the structural integrity of the final product.
-
Phases of the Sintering Process:
- Heating Phase: The material is gradually heated to a high temperature, allowing heat to transfer from the surface to the core.
- Sintering Phase: At the target temperature, particles bond through densification and intergranular neck growth, reducing porosity and increasing density.
- Cooling Phase: The material is slowly cooled to room temperature, ensuring it retains its strength and density.
-
Role of a Zirconia Sintering Furnace:
- A zirconia sintering furnace is specifically designed to handle the sintering process for zirconia. Key features include:
- High-precision temperature control (e.g., PID intelligent temperature control system with ±1℃ accuracy).
- Advanced heating elements for even heat distribution.
- Efficient air circulation to maintain optimal oxygen levels and achieve desired color and surface finish.
- A zirconia sintering furnace is specifically designed to handle the sintering process for zirconia. Key features include:
-
Benefits of Sintering for Zirconia:
- Improved Mechanical Strength: Sintering reduces porosity and increases density, resulting in a final product with superior hardness and durability.
- Enhanced Surface Finish: The process ensures a smooth and consistent surface, which is crucial for applications like dental restorations.
- Efficiency: Modern sintering furnaces, such as those used for zirconia, can complete the process in as little as 65 minutes, including heating, sintering, and cooling phases.
-
Advanced Features of Modern Sintering Furnaces:
- Fast Sintering Programs: Some furnaces offer rapid sintering cycles, reducing production time.
- High Capacity: Furnaces can stack multiple layers of crucibles, allowing for the sintering of up to 150 units in a single cycle.
- Environmental and Safety Features: Use of green, pollution-free materials and memory functions that resume operations after power interruptions.
-
Applications of Sintered Zirconia:
- Sintered zirconia is widely used in industries such as dentistry, where its strength, durability, and aesthetic properties are highly valued. The sintering process ensures that zirconia restorations meet the required standards for fit, function, and appearance.
By understanding the traditional sintering process and the role of advanced equipment like the zirconia sintering furnace, manufacturers can produce high-quality zirconia products with consistent properties and performance.
Summary Table:
Aspect | Details |
---|---|
Definition | Fuses materials like zirconia into a solid mass without melting, enhancing structural integrity. |
Phases | Heating, sintering, and cooling phases to ensure strength and density. |
Key Equipment | Zirconia sintering furnace with precise temperature control and even heat distribution. |
Benefits | Improved mechanical strength, enhanced surface finish, and high efficiency. |
Applications | Widely used in dentistry for durable and aesthetically pleasing zirconia restorations. |
Ready to optimize your sintering process? Contact us today to learn more about our advanced zirconia sintering furnaces!