A rotary furnace operates on the principle of rotating a barrel-shaped chamber around its axis while heating materials inside. The furnace is slightly tilted to allow the material to move from one end to the other as it rotates. This rotation ensures thorough mixing and uniform heating of the materials. Hot gases flow through the chamber, either in the same or opposite direction of the material, depending on the application. The furnace is versatile, capable of handling various fuels and materials, and is used in processes like heat treatment, smelting, and manufacturing of specialized products like lenses and mirrors.
Key Points Explained:
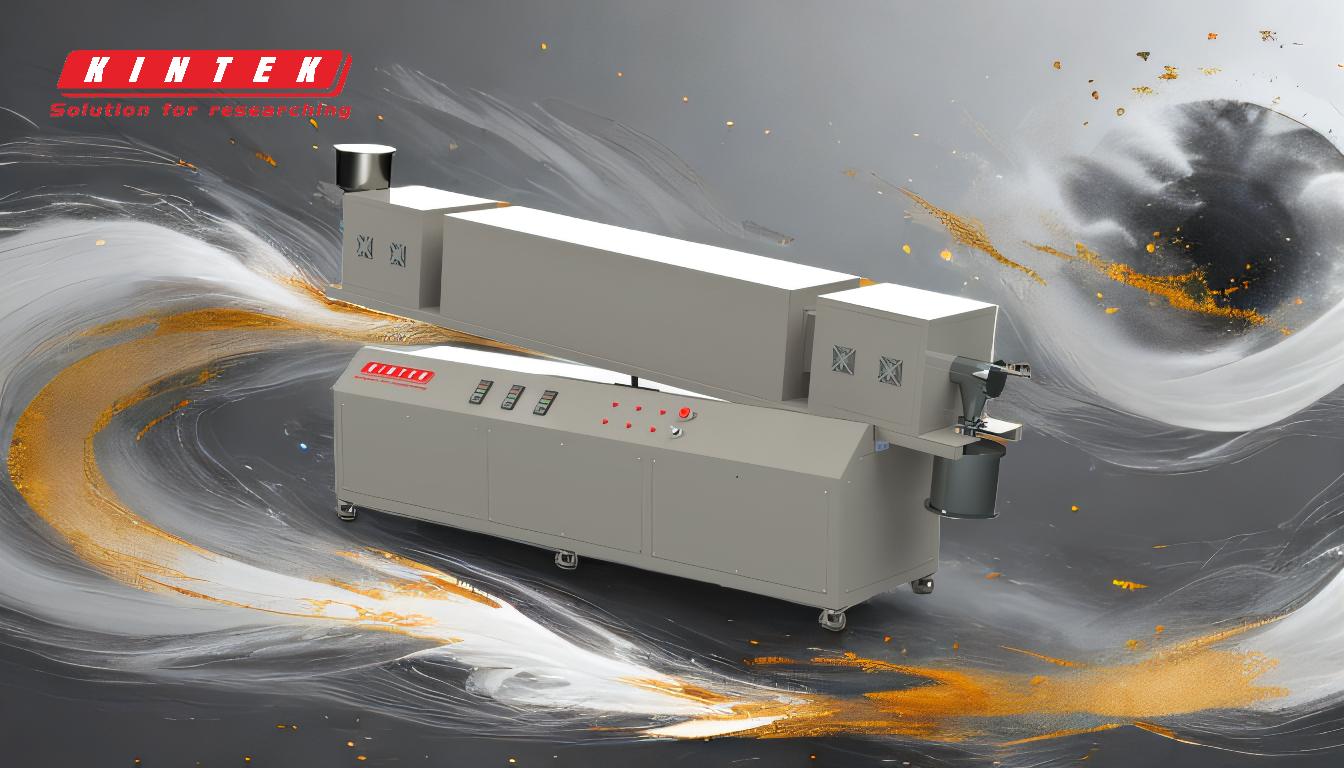
-
Barrel-Shaped Design and Rotation:
- The rotary furnace is designed as a barrel-shaped chamber that rotates around its central axis. This rotation ensures that the material inside is constantly mixed and exposed to heat uniformly.
- The rotation also helps in transporting the material from one end of the furnace to the other, especially when the furnace is slightly tilted.
-
Tilting Mechanism:
- The furnace is tilted slightly to facilitate the movement of the material through the chamber. This tilt, combined with the rotation, ensures that the material flows smoothly from the input end to the output end.
- The angle of tilt can be adjusted depending on the specific requirements of the process, such as the desired residence time of the material in the furnace.
-
Heating and Mixing:
- As the furnace rotates, the materials inside are continuously mixed, which promotes uniform heating and chemical reactions if required.
- The mixing action is particularly important in processes where homogeneity of the material is crucial, such as in the production of alloys or the treatment of mineral ores.
-
Hot Gas Flow:
- Hot gases are introduced into the furnace chamber to provide the necessary heat for the process. These gases can flow in the same direction as the material (co-current) or in the opposite direction (counter-current).
- The direction of gas flow can be chosen based on the specific application. For example, counter-current flow is often used to maximize heat transfer efficiency.
-
Versatility in Fuel and Material Handling:
- Rotary furnaces can be operated using various types of fuel, including pulverized solid fuels, gaseous fuels, or liquid fuels. This flexibility allows the furnace to be used in a wide range of industrial applications.
- The furnace can handle different types of materials, from mineral ores to liquid metals, making it suitable for processes like smelting, heat treatment, and even the production of specialized optical components.
-
Centrifugal Force in Specialized Applications:
- In some specialized applications, such as the manufacturing of lenses and mirrors, the rotary furnace is used to create a paraboloid shape in the molten material. The furnace is spun on its horizontal axis, and the centrifugal force acting on the liquid metal gives it the desired shape.
- Once the material solidifies upon cooling, it retains the shape formed by the centrifugal force, resulting in high-precision optical components.
-
Operational Simplicity:
- Rotary furnaces are designed to be operated by relatively unskilled workers. The process typically involves charging the furnace with a batch of material, heating it for a specified period (usually 4–6 hours), and then tapping the furnace to remove the processed material.
- This simplicity in operation makes rotary furnaces cost-effective and easy to maintain, especially in large-scale industrial settings.
-
Applications:
- Rotary furnaces are used in a variety of industries, including metallurgy, materials science, and optics. They are particularly useful for processes that require uniform heating, mixing, and controlled cooling of materials.
- Specific applications include the smelting of metals, the heat treatment of mineral ores, and the production of lenses and mirrors using liquid metals or low-melting alloys.
In summary, the rotary furnace is a versatile and efficient tool for heat treatment and material processing. Its design, which includes rotation, tilting, and controlled gas flow, ensures uniform heating and mixing of materials, making it suitable for a wide range of industrial applications.
Summary Table:
Key Feature | Description |
---|---|
Barrel-Shaped Design | Rotates to mix and heat materials uniformly, ensuring consistent processing. |
Tilting Mechanism | Facilitates material flow with adjustable tilt for precise control. |
Heating and Mixing | Continuous rotation promotes uniform heating and chemical reactions. |
Hot Gas Flow | Co-current or counter-current flow for efficient heat transfer. |
Fuel and Material Handling | Compatible with solid, liquid, or gaseous fuels and diverse materials. |
Centrifugal Force | Used in specialized applications like lens and mirror production. |
Operational Simplicity | Easy to operate and maintain, ideal for large-scale industrial use. |
Applications | Smelting, heat treatment, alloy production, and optical component manufacturing. |
Discover how a rotary furnace can optimize your material processing—contact our experts today!