Thermal Vapor Deposition (TVD) is a thin-film deposition technique where a material is heated to its vaporization point, causing it to transition into the gas phase. This vaporized material then condenses on a substrate to form a thin film. TVD is a subset of Physical Vapor Deposition (PVD) techniques and is widely used in industries requiring precise and high-quality coatings, such as electronics, optics, and decorative applications. The process is known for its ability to produce uniform, high-purity films with controlled properties, making it suitable for applications ranging from semiconductor manufacturing to decorative coatings.
Key Points Explained:
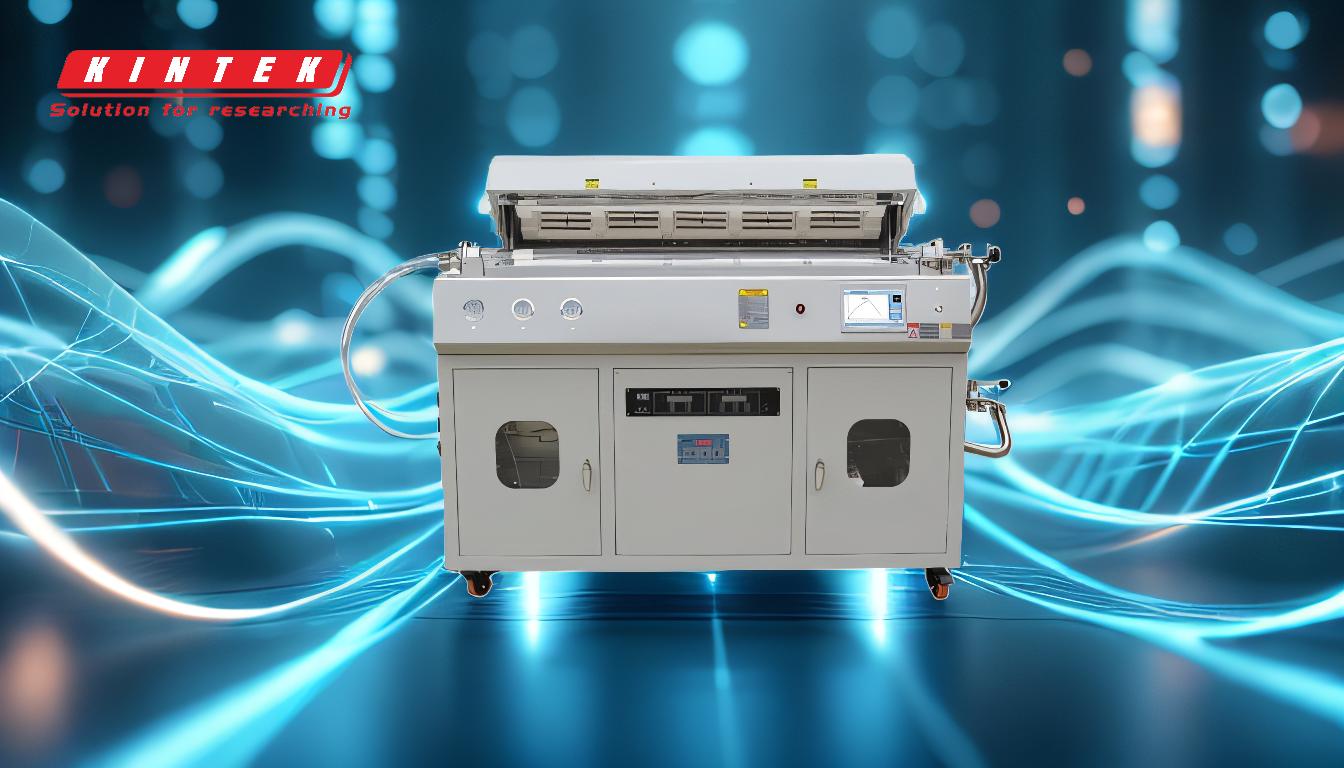
-
Basic Principle of Thermal Vapor Deposition:
- In TVD, the material to be deposited is heated using an electric heater until it vaporizes. The vaporized material then travels through a vacuum or low-pressure environment and condenses on a cooler substrate, forming a thin film.
- This process is purely physical, meaning no chemical reactions occur between the material and the substrate.
-
Comparison with Other PVD Techniques:
- Unlike sputtering deposition, where high-energy ions bombard a target to release material, TVD relies solely on thermal energy to vaporize the material.
- TVD is often simpler and more cost-effective than techniques like Chemical Vapor Deposition (CVD), which involves chemical reactions to form the film.
-
Applications of TVD:
- Decorative Coatings: TVD is widely used in the manufacturing of jewelry, door and window hardware, kitchen and bathroom fixtures, and other decorative products. It provides a durable and aesthetically pleasing metallic finish.
- Functional Coatings: TVD is used in industries requiring thin films for mechanical, optical, chemical, or electronic functions. Examples include semiconductor devices, thin-film solar panels, and glass coatings.
-
Advantages of TVD:
- High Purity: Since the process is purely physical, the deposited films are of high purity.
- Uniformity: TVD can produce highly uniform films, even on complex-shaped surfaces.
- Controlled Properties: By adjusting deposition parameters such as temperature and pressure, the properties of the film (e.g., thickness, crystal structure) can be precisely controlled.
-
Limitations of TVD:
- Material Limitations: Not all materials can be easily vaporized using thermal energy, limiting the range of materials that can be deposited.
- High Temperatures: The process often requires high temperatures, which may not be suitable for temperature-sensitive substrates.
-
Comparison with Chemical Vapor Deposition (CVD):
- While TVD is a physical process, CVD involves chemical reactions to form the film. CVD can deposit a wider variety of materials, including metals, non-metals, alloys, and ceramics, and offers better wrap-around properties for complex surfaces.
- However, CVD typically requires higher temperatures and more complex equipment compared to TVD.
-
Future Trends in TVD:
- Nanotechnology: TVD is increasingly being used in the deposition of nanomaterials, which have applications in electronics, energy storage, and biomedical devices.
- Sustainability: Efforts are being made to reduce the energy consumption and environmental impact of TVD processes, making them more sustainable.
In summary, Thermal Vapor Deposition is a versatile and widely used technique for depositing thin films with high purity and uniformity. Its applications range from decorative coatings to functional layers in advanced technologies. While it has some limitations, ongoing advancements are expanding its capabilities and making it more efficient and environmentally friendly.
Summary Table:
Aspect | Details |
---|---|
Basic Principle | Material is heated to vaporize, then condenses on a substrate to form a film. |
Key Advantages | High purity, uniformity, controlled film properties. |
Applications | Decorative coatings, semiconductor devices, solar panels, glass coatings. |
Limitations | Material limitations, high-temperature requirements. |
Comparison with CVD | Simpler and more cost-effective but less versatile than CVD. |
Future Trends | Nanotechnology applications and sustainability improvements. |
Discover how Thermal Vapor Deposition can enhance your projects—contact us today for expert advice!