Thin film deposition in nanotechnology refers to the process of depositing ultra-thin layers of material, often just a few atoms thick, onto a substrate. This technique is fundamental in nanotechnology for creating nano-scale structures and coatings that enhance material properties. It involves methods like physical vapor deposition (PVD) and chemical vapor deposition (CVD), which are used to produce thin films with specific mechanical, electrical, optical, or chemical properties. These thin films are critical in applications such as semiconductor devices, integrated circuits, optical coatings, and advanced materials like carbon nanotubes and nanocomposites. Thin film deposition enables the creation of high-performance materials with improved oxidation resistance, wear resistance, and mechanical strength, making it a cornerstone of modern nanotechnology and its applications across various industries.
Key Points Explained:
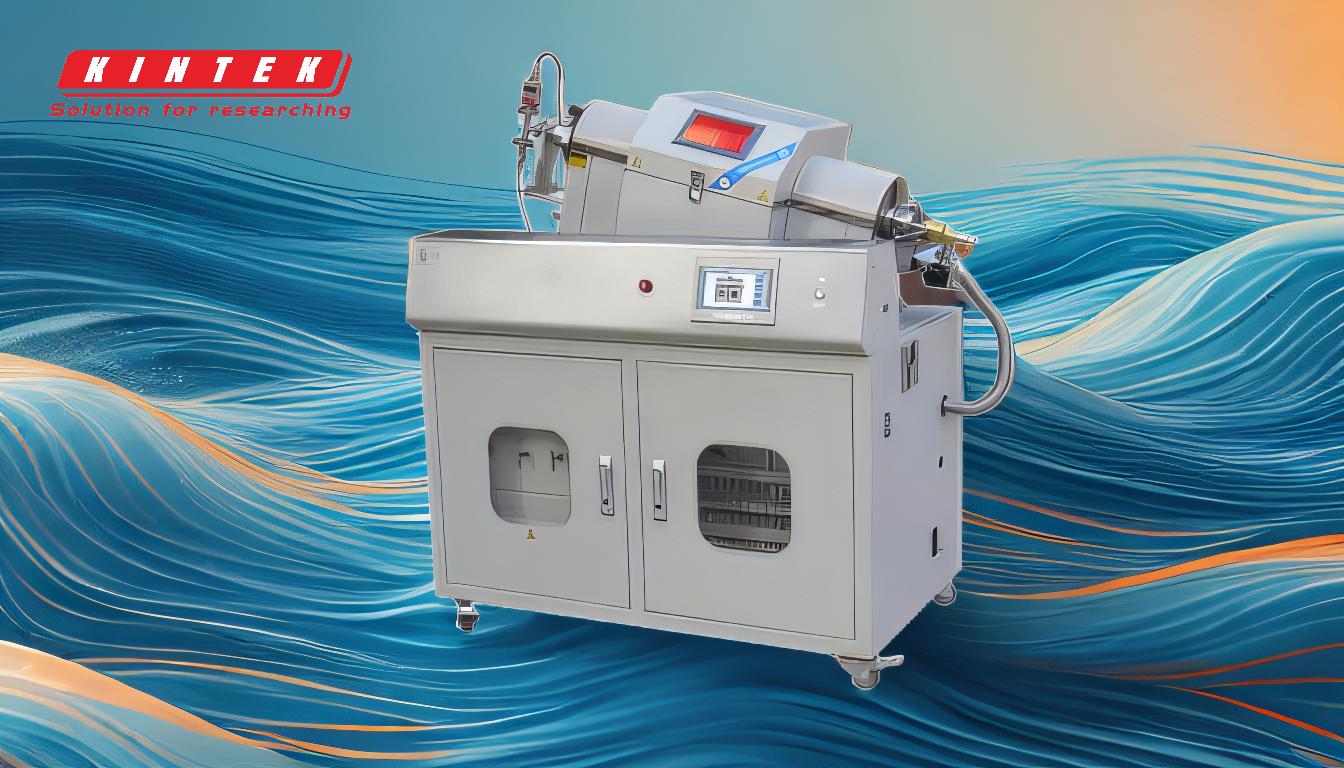
-
Definition of Thin Film Deposition in Nanotechnology:
- Thin film deposition is the process of applying an extremely thin layer of material (nanometer to micrometer thickness) onto a substrate. This technique is essential in nanotechnology for creating nano-scale structures and functional coatings.
- The process is typically carried out in a vacuum chamber to ensure precision and control over the deposition process.
-
Techniques for Thin Film Deposition:
-
Physical Vapor Deposition (PVD):
- Involves vaporizing a source material in a vacuum environment and depositing it onto a substrate.
- Common PVD methods include thermal evaporation, sputtering, and ion beam deposition.
-
Chemical Vapor Deposition (CVD):
- Uses chemical precursors that react at the substrate surface to form a thin film.
- CVD is widely used for growing carbon nanotubes and creating nanocomposite coatings.
-
Physical Vapor Deposition (PVD):
-
Applications in Nanotechnology:
-
Semiconductor Industry:
- Thin film deposition is critical for manufacturing integrated circuits and semiconductor devices, enabling improved conductance or insulation.
-
Optical Coatings:
- Used to enhance the transmission, refraction, and reflection properties of lenses and plate glass.
-
Advanced Materials:
- Enables the creation of nanocomposite layers with improved mechanical properties, such as oxidation resistance, wear resistance, and higher toughness.
-
Energy and Electronics:
- Applied in the development of thin-film batteries, photovoltaic solar cells, and quantum computers.
-
Biomedical:
- Used in drug delivery systems and biocompatible coatings.
-
Semiconductor Industry:
-
Benefits of Thin Film Deposition:
-
Enhanced Material Properties:
- Thin films improve mechanical, electrical, and optical properties due to the "size effect," resulting in high adherence, low thermal conductivity, and wear resistance.
-
Versatility:
- The technique is applicable across a wide range of industries, from electronics to energy and healthcare.
-
Precision:
- Allows for the creation of ultra-small structures and coatings with nanometer-scale precision.
-
Enhanced Material Properties:
-
Challenges and Considerations:
-
Layer Thickness Debate:
- Some argue that merely achieving nanometer-scale thickness does not constitute true nanotechnology, but thin film deposition is increasingly contributing to the development of advanced nanotechnologies.
-
Process Complexity:
- Techniques like CVD and PVD require specialized equipment and controlled environments, making the process technically demanding.
-
Material Compatibility:
- The choice of materials and deposition methods must be carefully tailored to the specific application and substrate.
-
Layer Thickness Debate:
-
Future Prospects:
- Thin film deposition is paving the way for the next generation of nanotechnology applications, including ultra-small sensors, integrated circuitry, and complex designs.
- Its relevance continues to grow as industries demand materials with superior performance and miniaturized components.
In summary, thin film deposition is a cornerstone of nanotechnology, enabling the creation of advanced materials and devices with enhanced properties. Its applications span multiple industries, and its techniques continue to evolve, driving innovation in modern technology.
Summary Table:
Aspect | Details |
---|---|
Definition | Depositing ultra-thin layers (nanometer to micrometer) onto a substrate. |
Key Techniques | - Physical Vapor Deposition (PVD) |
- Chemical Vapor Deposition (CVD) | |
Applications | - Semiconductors |
- Optical Coatings
- Advanced Materials
- Energy & Electronics
- Biomedical | | Benefits | Enhanced mechanical, electrical, and optical properties; precision; versatility. | | Challenges | Process complexity, material compatibility, and layer thickness debate. | | Future Prospects | Ultra-small sensors, integrated circuitry, and next-gen nanotechnology. |
Ready to explore how thin film deposition can revolutionize your projects? Contact our experts today for tailored solutions!