Vacuum coating is a versatile technology used across various industries for enhancing the properties of materials such as glass, metal, and plastics. Its applications range from decorative purposes to functional improvements like durability, energy efficiency, and corrosion resistance. Key uses include low-emissivity glass for energy savings, hard coatings for engine components, ophthalmic coatings for lenses, and thin-film applications in electronics and solar cells. Additionally, vacuum coating is employed in aerospace, automotive, and medical industries for advanced material properties, such as wear resistance, conductivity, and optical performance. This technology plays a critical role in modern manufacturing, enabling innovations in energy conservation, electronics, and industrial durability.
Key Points Explained:
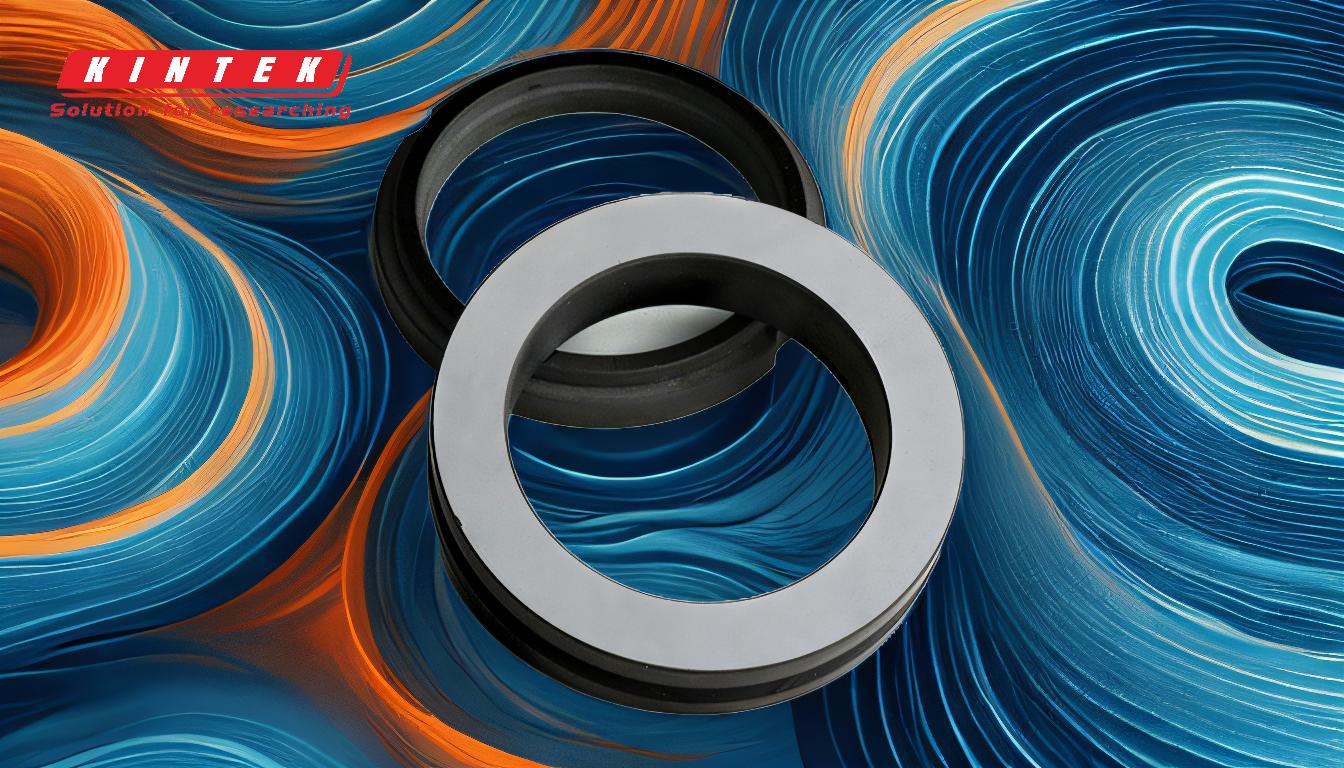
-
Decorative and Functional Applications:
- Vacuum coating is used to enhance the aesthetic appeal of materials like glass, metal, and plastics. For example, decorative coatings are applied to consumer products for a polished or reflective finish.
- Functional improvements include durability and energy efficiency. For instance, low-emissivity (Low-E) glass coatings reduce heat transfer, improving energy conservation in buildings.
-
Industrial and Automotive Uses:
- In the automotive industry, vacuum coating is applied to carbon fiber composites and engine components to improve wear resistance and durability.
- Hard coatings are used on engine parts to withstand high temperatures and friction, extending the lifespan of critical components.
-
Electronics and Semiconductor Manufacturing:
- Vacuum deposition is essential in producing microchips, LEDs, and solar cells. It coats metal patterns that are critical for the functionality of electronic devices.
- Thin-film transistors, used in flexible displays and sensors, are manufactured using vacuum coating processes, enabling advancements in consumer electronics.
-
Energy Efficiency and Solar Technology:
- Thin-film solar cells rely on vacuum coating to enhance conductivity and light absorption, improving the efficiency and durability of solar panels.
- Reflective and optical coatings are used in energy conservation applications, such as mirrors and windows, to optimize light utilization.
-
Corrosion and Wear Resistance:
- Vacuum coating provides corrosion-resistant layers on substrates, protecting materials used in harsh environments, such as marine or industrial settings.
- Wear-resistant coatings are applied to tools and machinery to reduce friction and extend operational life.
-
Medical and Aerospace Applications:
- In the medical field, vacuum coating is used to create biocompatible and wear-resistant surfaces for implants and surgical tools.
- Aerospace applications include coatings for components that require high strength, thermal stability, and resistance to environmental stressors.
-
Optical and Reflective Coatings:
- Optical interference coatings and mirror coatings are used in lenses, telescopes, and other optical devices to enhance light transmission and reflection.
- These coatings are critical in applications like laser systems, cameras, and scientific instruments.
-
Flexible Packaging and Barrier Films:
- Vacuum coating is used to create permeation barrier films on flexible packaging materials, preventing moisture and gas exchange to preserve food and pharmaceuticals.
- This application is vital for extending the shelf life of perishable products.
-
Magnetic and Conductive Films:
- Magnetic films produced through vacuum coating are used in data storage devices and sensors.
- Electrically conducting films are applied in touchscreens, displays, and other electronic interfaces.
-
Innovative and Emerging Applications:
- Vacuum coating is enabling advancements in flexible electronics, such as foldable screens and wearable devices.
- It is also being explored for next-generation applications in renewable energy, nanotechnology, and advanced materials.
By leveraging vacuum coating technology, industries can achieve enhanced material performance, energy efficiency, and innovative product designs, making it a cornerstone of modern manufacturing and engineering.
Summary Table:
Application | Key Benefits |
---|---|
Decorative & Functional | Aesthetic appeal, durability, energy efficiency (e.g., Low-E glass) |
Industrial & Automotive | Wear resistance, durability (e.g., engine components) |
Electronics & Solar | Enhanced conductivity, light absorption (e.g., solar cells, microchips) |
Corrosion & Wear Resistance | Protection in harsh environments, extended operational life |
Medical & Aerospace | Biocompatibility, thermal stability, wear resistance |
Optical & Reflective Coatings | Improved light transmission, reflection (e.g., lenses, mirrors) |
Flexible Packaging | Barrier films for moisture and gas protection |
Magnetic & Conductive Films | Data storage, touchscreens, electronic interfaces |
Emerging Applications | Foldable screens, wearable devices, renewable energy advancements |
Unlock the potential of vacuum coating for your industry—contact our experts today!