Heat treating metal is a critical process in metallurgy, but it can lead to several problems if not carefully controlled. These issues include oxidation, distortion, cracking, and changes in mechanical properties. Oxidation occurs when metals react with oxygen at high temperatures, forming oxides that can degrade the material's surface quality. Distortion and cracking are often the result of uneven heating or cooling, leading to internal stresses that can deform or fracture the metal. Additionally, improper heat treatment can alter the metal's mechanical properties, such as hardness, toughness, and ductility, potentially making it unsuitable for its intended application. Understanding these potential problems is essential for ensuring the quality and performance of heat-treated metals.
Key Points Explained:
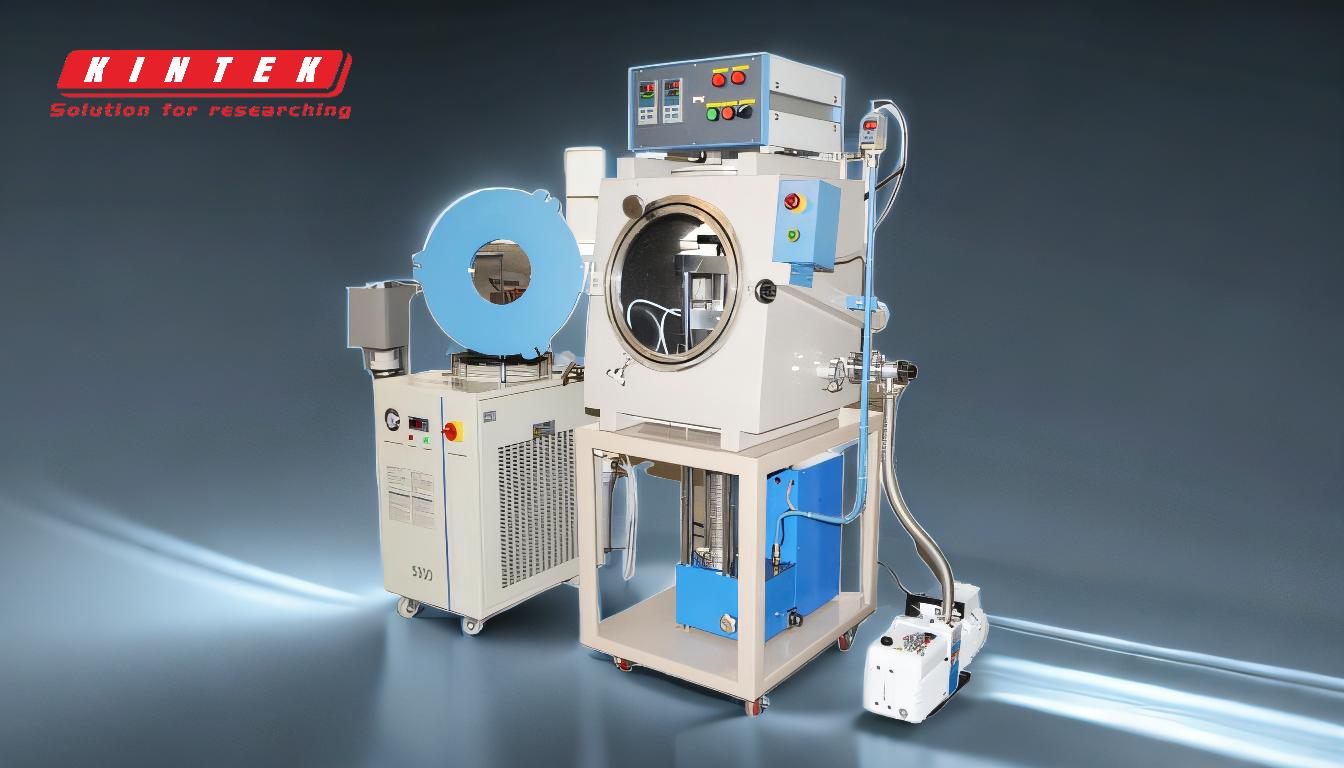
-
Oxidation:
- Description: When metals are heated to high temperatures, they can react with oxygen in the air, forming oxides on the surface. This oxidation can degrade the metal's surface quality and reduce its effectiveness in applications where a clean, smooth surface is required.
- Impact: Oxidation can lead to a loss of material, surface roughness, and the formation of scale, which may require additional processing to remove. In some cases, the oxide layer can also affect the metal's ability to bond with other materials, such as in coatings or adhesives.
-
Distortion:
- Description: Uneven heating or cooling during the heat treatment process can cause internal stresses within the metal, leading to distortion. This can result in warping, bending, or twisting of the metal part.
- Impact: Distortion can make the metal part unfit for its intended use, especially in precision applications where tight tolerances are required. It may also necessitate additional machining or straightening processes to correct the shape, increasing production time and costs.
-
Cracking:
- Description: Rapid cooling or quenching can introduce significant thermal stresses in the metal, which may lead to cracking. This is particularly common in metals that are brittle or have high hardenability.
- Impact: Cracking can compromise the structural integrity of the metal part, making it unsafe or unusable. It can also lead to catastrophic failure in critical applications, such as in aerospace or automotive components.
-
Changes in Mechanical Properties:
- Description: Heat treatment can alter the metal's mechanical properties, such as hardness, toughness, and ductility. For example, excessive heating can make the metal too soft, while rapid cooling can make it too brittle.
- Impact: Changes in mechanical properties can render the metal unsuitable for its intended application. For instance, a metal that is too brittle may not be able to withstand impact or stress, while a metal that is too soft may wear out quickly under load.
-
Preventive Measures:
- Description: To mitigate these problems, it is essential to control the heat treatment process carefully. This includes using controlled atmospheres or vacuum furnaces to prevent oxidation, ensuring uniform heating and cooling to avoid distortion and cracking, and selecting appropriate heat treatment parameters to achieve the desired mechanical properties.
- Impact: Proper control of the heat treatment process can significantly improve the quality and performance of the metal part, reducing the likelihood of defects and ensuring that it meets the required specifications.
By understanding these potential problems and implementing appropriate preventive measures, manufacturers can ensure that heat-treated metals meet the necessary quality standards and perform reliably in their intended applications.
Summary Table:
Problem | Description | Impact |
---|---|---|
Oxidation | Metals react with oxygen at high temps, forming oxides that degrade surface quality. | Loss of material, surface roughness, and bonding issues. |
Distortion | Uneven heating/cooling causes internal stresses, leading to warping or bending. | Parts may become unfit for use, requiring costly corrections. |
Cracking | Rapid cooling introduces thermal stresses, causing cracks, especially in brittle metals. | Compromised structural integrity, risking catastrophic failure. |
Mechanical Property Changes | Heat treatment alters hardness, toughness, and ductility. | Metal may become too soft or brittle, making it unsuitable for its purpose. |
Preventive Measures | Control heating/cooling, use controlled atmospheres, and select proper parameters. | Ensures quality, performance, and reliability of heat-treated metals. |
Ensure your heat-treated metals meet quality standards—contact our experts today for tailored solutions!