Tempering is a critical heat treatment process used to enhance the mechanical properties of metals, particularly steel, after hardening. It involves reheating the metal to a temperature below its transformation range and then cooling it to achieve a balance between hardness, toughness, and ductility. This process reduces brittleness, relieves internal stresses caused by rapid cooling during quenching, and improves the metal's ability to withstand deformation and energy absorption. Tempering is essential in applications where the material must be both strong and durable, such as in tools, automotive components, and structural parts.
Key Points Explained:
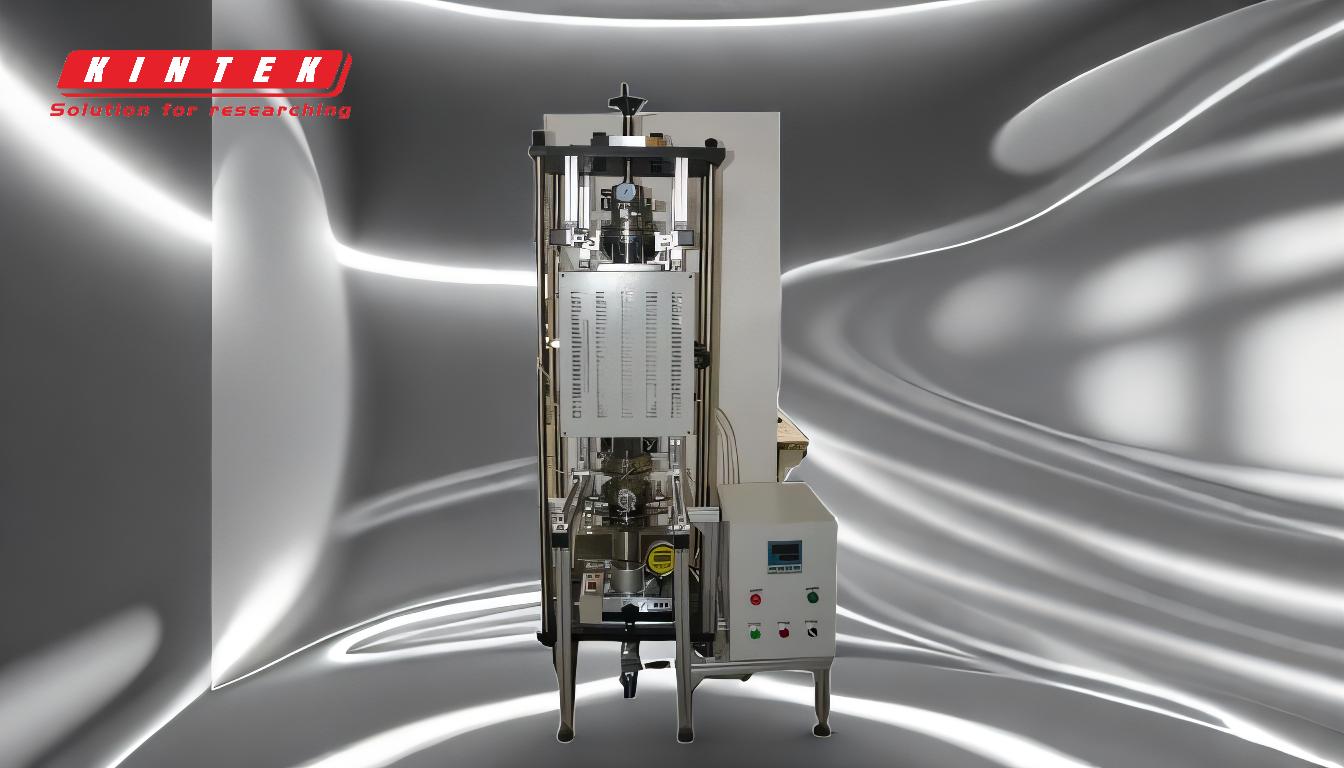
-
Purpose of Tempering:
- Reduction of Brittleness: Tempering reduces the brittleness of hardened steel, making it less prone to cracking or breaking under stress.
- Stress Relief: It removes internal strains caused by sudden cooling during quenching, ensuring the material is more stable and less likely to fail.
-
Process of Tempering:
- Heating: The metal is heated to a specific temperature below its transformation range, typically between 150°C to 650°C, depending on the desired properties.
- Cooling: After heating, the metal is cooled, which can be done in air, oil, or water, depending on the material and the required properties.
-
Benefits of Tempering:
- Improved Toughness: Tempering increases the toughness of the metal, allowing it to absorb more energy before fracturing.
- Enhanced Ductility: The process improves the ductility of the metal, making it more flexible and less brittle.
- Balanced Hardness and Toughness: Tempering helps achieve an optimal balance between hardness and toughness, which is crucial for many applications.
-
Types of Structures Formed:
- Troostite: A softer and tougher structure formed during tempering, which provides a good balance between hardness and toughness.
- Sorbite: A weaker but more ductile structure, which is beneficial in applications where flexibility is more important than strength.
-
Applications of Tempering:
- Tools and Dies: Tempering is commonly used in the manufacturing of tools and dies to ensure they are hard enough to cut or shape other materials but also tough enough to resist breaking.
- Automotive Components: Many automotive parts, such as gears and axles, undergo tempering to enhance their durability and resistance to wear.
- Structural Parts: Tempering is also used in structural components to improve their ability to withstand loads and stresses without failing.
-
Specialized Tempering Processes:
- Vacuum Tempering: This process involves precise heating and rapid cooling in a vacuum environment, which is used to create hard steel that can withstand extreme applications. The steel is then reheated to balance hardness with ductility.
In summary, tempering is a vital process in metallurgy that enhances the mechanical properties of metals, making them more suitable for demanding applications. By carefully controlling the heating and cooling processes, manufacturers can achieve the desired balance of hardness, toughness, and ductility, ensuring the longevity and reliability of the final product.
Summary Table:
Aspect | Details |
---|---|
Purpose | Reduces brittleness, relieves internal stresses, balances hardness/toughness |
Process | Heating (150°C–650°C) followed by controlled cooling (air, oil, or water) |
Benefits | Improved toughness, enhanced ductility, balanced mechanical properties |
Structures Formed | Troostite (hardness-toughness balance), Sorbite (flexibility-focused) |
Applications | Tools, automotive components (gears, axles), structural parts |
Specialized Processes | Vacuum tempering for extreme applications |
Discover how tempering can optimize your metal components—contact our experts today!