Heat treatment of small parts requires precision, controlled environments, and specialized equipment to achieve desired material properties such as hardness, toughness, and durability. The choice of furnace depends on factors like the type of material, the specific heat treatment process, and the required temperature range. Common furnaces used for this purpose include muffle furnaces, vacuum furnaces, and box furnaces, each offering unique advantages for small-scale heat treatment.
Key Points Explained:
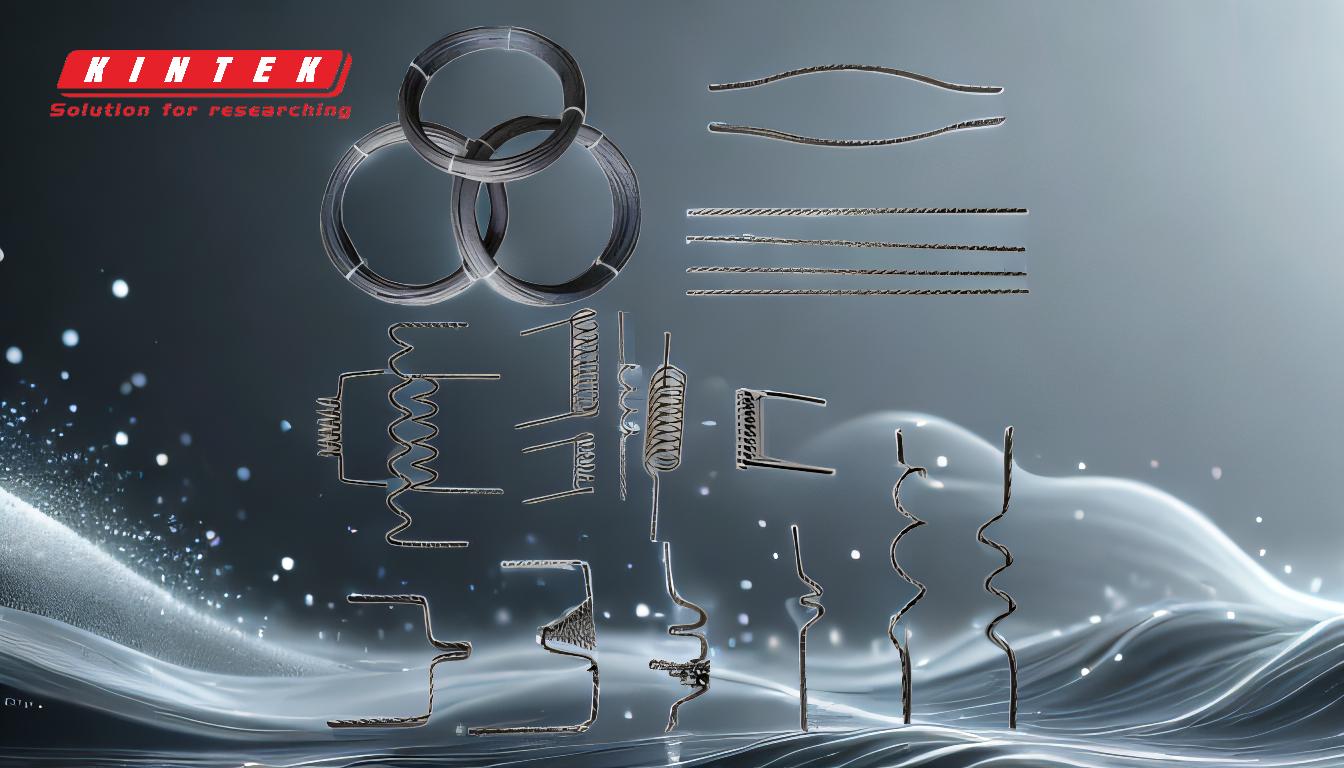
-
Muffle Furnaces
- Muffle furnaces are widely used for heat treatment of small parts due to their ability to provide a controlled, isolated environment. The muffle (a ceramic or metal chamber) separates the heating elements from the workpiece, preventing contamination and ensuring uniform heating.
- These furnaces are ideal for processes like annealing, hardening, and tempering, especially for materials sensitive to oxidation or contamination.
- They are available in various sizes, making them suitable for small parts and laboratory-scale applications.
- The temperature range of muffle furnaces typically spans from 100°C to 1800°C, accommodating a wide variety of materials and processes.
-
Vacuum Furnaces
- Vacuum furnaces are preferred for heat treatment processes requiring an oxygen-free environment, such as brazing, sintering, and annealing of high-precision components.
- These furnaces eliminate oxidation and decarburization, ensuring the integrity and surface quality of small parts.
- They are particularly useful for heat-treating materials like titanium, stainless steel, and superalloys, which are prone to oxidation at high temperatures.
- Vacuum furnaces offer precise temperature control and uniform heating, making them suitable for critical applications in aerospace, medical, and electronics industries.
-
Box Furnaces
- Box furnaces are versatile and cost-effective options for heat treatment of small parts. They are designed with a rectangular chamber, providing ample space for batch processing.
- These furnaces are suitable for processes like annealing, stress relieving, and normalizing, especially for steel and alloy components.
- Box furnaces are available in both air-atmosphere and controlled-atmosphere configurations, allowing flexibility based on the material and process requirements.
- They are commonly used in industries like automotive, tooling, and general manufacturing due to their durability and ease of operation.
-
Factors to Consider When Choosing a Furnace
- Temperature Range: Ensure the furnace can achieve and maintain the required temperatures for the specific heat treatment process.
- Atmosphere Control: Determine whether an inert, vacuum, or air atmosphere is needed to prevent oxidation or contamination.
- Uniformity: Look for furnaces with excellent temperature uniformity to ensure consistent results across all parts.
- Size and Capacity: Choose a furnace that accommodates the size and quantity of parts being treated.
- Energy Efficiency: Consider furnaces with advanced insulation and heating elements to reduce energy consumption.
-
Applications of Small Part Heat Treatment
- Small parts heat treatment is critical in industries like aerospace (for turbine blades and fasteners), medical (for surgical instruments and implants), and electronics (for connectors and sensors).
- The choice of furnace directly impacts the quality, performance, and longevity of these components.
By carefully evaluating the specific requirements of your heat treatment process, you can select the most suitable furnace for small parts, ensuring optimal results and efficient operations.
Summary Table:
Furnace Type | Key Features | Temperature Range | Applications |
---|---|---|---|
Muffle Furnace | Controlled, isolated environment; prevents contamination | 100°C to 1800°C | Annealing, hardening, tempering |
Vacuum Furnace | Oxygen-free environment; prevents oxidation | Up to 1800°C | Brazing, sintering, annealing |
Box Furnace | Versatile, cost-effective; batch processing | Up to 1200°C | Annealing, stress relieving, normalizing |
Need help selecting the right furnace for your small part heat treatment? Contact our experts today for personalized advice!