Heat treatment processes such as hardening, annealing, and tempering are essential for modifying the mechanical properties of machine parts, including hardness, strength, and ductility. These processes typically involve heating materials to specific temperatures in controlled environments to achieve desired outcomes. The type of heating used depends on the material, the specific heat treatment process, and the required precision. Common heating methods include electric heating, gas heating, and induction heating, often carried out in specialized furnaces like chamber furnaces, atmosphere furnaces, and vacuum furnaces. The choice of heating elements, such as resistance wires, silicon carbon rods, or molybdenum bands, is also critical, as each element has specific temperature ranges and properties suited to different applications.
Key Points Explained:
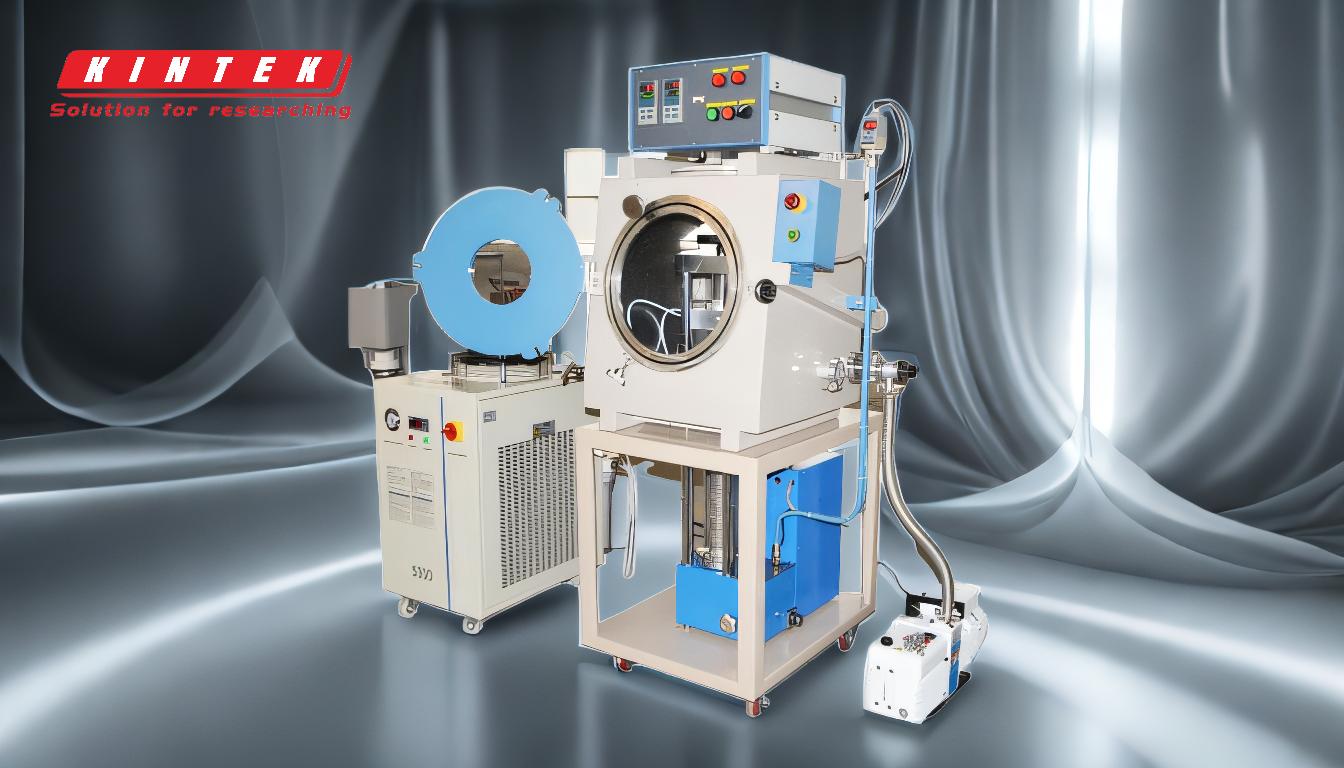
-
Common Heat Treatment Processes:
- Heat treatment processes like hardening, annealing, and tempering are used to alter the mechanical properties of machine parts.
- Hardening increases hardness and strength, annealing improves ductility and reduces internal stresses, and tempering reduces brittleness while maintaining hardness.
- These processes require precise temperature control and often involve elevated furnace temperatures.
-
Types of Heating Methods:
- Electric Heating: Commonly used due to its precision and controllability. Bright annealing furnaces, for example, are often electrically heated and designed for specific applications like annealing carbon steel tubes.
- Gas Heating: Utilized in some industrial applications for its cost-effectiveness and ability to reach high temperatures.
- Induction Heating: Suitable for localized heating and rapid processing, often used in case hardening.
-
Furnace Types for Heat Treatment:
- Chamber Furnaces: Used for batch processing of parts, providing uniform heating in a controlled environment.
- Atmosphere Furnaces: Designed to control the atmosphere (e.g., inert gases) to prevent oxidation or decarburization during heat treatment.
- Vacuum Furnaces: Ideal for processes requiring a completely oxygen-free environment, such as bright annealing or brazing.
-
Heating Elements:
- Heating elements like resistance wires, silicon carbon rods, and molybdenum bands are chosen based on their temperature ranges and properties.
- For example, silicon carbon rods are suitable for high-temperature applications, while resistance wires are often used in lower-temperature processes.
-
Importance of Controlled Environments:
- Oxygen and other reactive gases can adversely affect the surface of materials during heat treatment, leading to oxidation or scaling.
- Bright annealing, for instance, requires an oxygen-free environment to maintain the material's surface finish and properties.
-
Applications and Customization:
- Furnaces and heating systems are often custom-designed for specific applications, such as bright annealing of carbon steel tubes with precise dimensions.
- The choice of heating method and furnace type depends on the material, the desired outcome, and production requirements.
By understanding these key points, equipment and consumable purchasers can make informed decisions about the heating methods and furnaces best suited for their specific heat treatment needs.
Summary Table:
Heating Method | Key Features | Applications |
---|---|---|
Electric Heating | Precise, controllable | Bright annealing, carbon steel tubes |
Gas Heating | Cost-effective, high temperatures | Industrial applications |
Induction Heating | Localized, rapid processing | Case hardening |
Furnace Types | Environment | Use Cases |
Chamber Furnaces | Uniform heating | Batch processing |
Atmosphere Furnaces | Controlled atmosphere | Oxidation prevention |
Vacuum Furnaces | Oxygen-free | Bright annealing, brazing |
Need help selecting the right heating method or furnace for your heat treatment processes? Contact our experts today!