Brazed joints are subjected to fatigue failure due to several factors, including stress concentration, material properties, and environmental conditions. Fatigue failure occurs when a material undergoes repeated cyclic stresses below its ultimate tensile strength, leading to the initiation and propagation of cracks over time. In brazed joints, the interface between the base metal and the filler material often acts as a stress concentrator, making it susceptible to fatigue. Additionally, the differences in thermal expansion coefficients between the base metal and the filler material can induce residual stresses, further exacerbating the likelihood of fatigue failure. Environmental factors such as temperature fluctuations and corrosive conditions can also accelerate the fatigue process.
Key Points Explained:
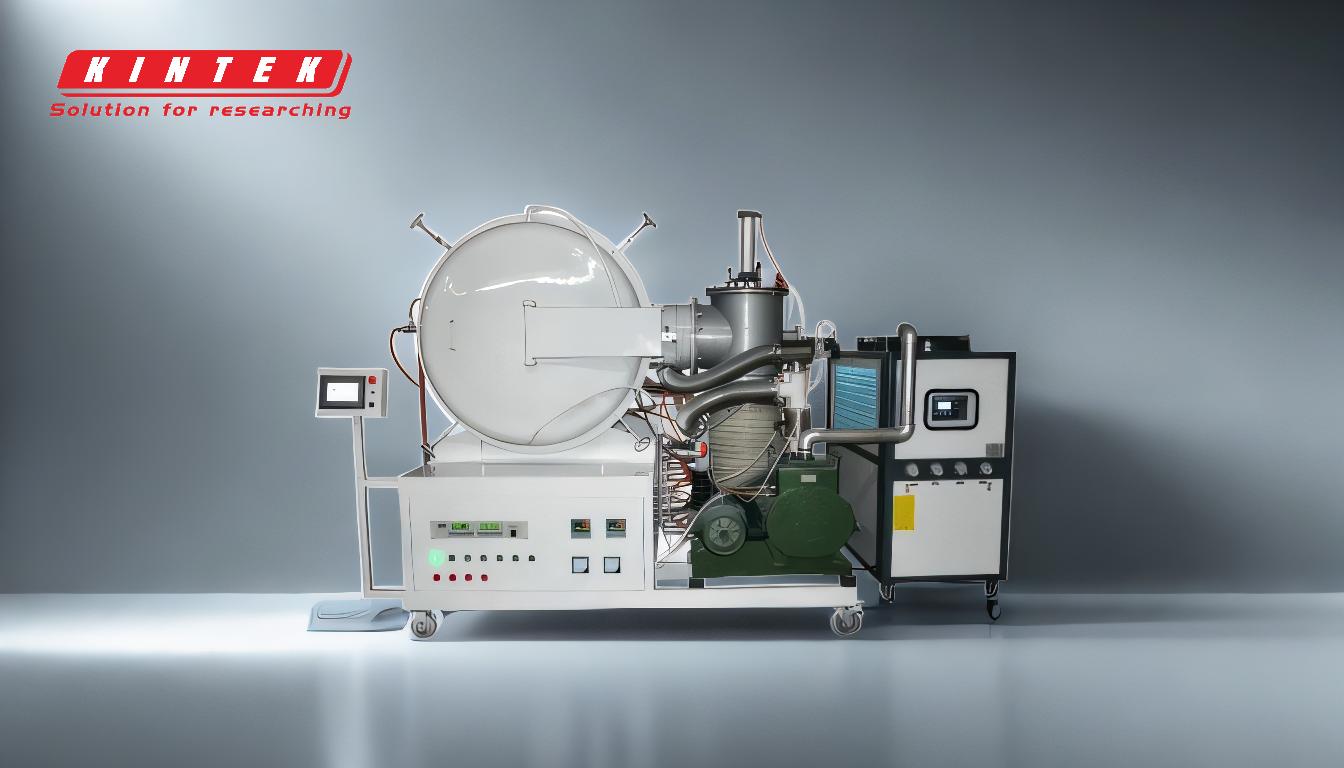
-
Stress Concentration in Brazed Joints:
- Brazed joints often have geometric discontinuities, such as fillets or gaps, which act as stress concentrators. These areas experience higher localized stresses under cyclic loading, making them prone to crack initiation.
- The interface between the base metal and the filler material can also be a weak point, as the bond may not be as strong as the base material itself, leading to stress concentration at the joint.
-
Material Properties and Residual Stresses:
- The base metal and the filler material used in brazing often have different thermal expansion coefficients. During the cooling phase of the brazing process, these differences can lead to the development of residual stresses within the joint.
- Residual stresses can reduce the fatigue strength of the joint, as they add to the applied cyclic stresses, making the joint more susceptible to fatigue failure.
-
Cyclic Loading and Fatigue Mechanisms:
- Fatigue failure occurs due to the repeated application of cyclic stresses, even if these stresses are below the material's ultimate tensile strength. Over time, microcracks initiate at stress concentrators and propagate through the material, leading to eventual failure.
- In brazed joints, the cyclic loading can cause the initiation of cracks at the interface or within the filler material, which then propagate through the joint, leading to fatigue failure.
-
Environmental Factors:
- Temperature fluctuations can cause thermal cycling, which induces additional stresses in the brazed joint. These thermal stresses can accelerate the fatigue process by promoting crack initiation and growth.
- Corrosive environments can also contribute to fatigue failure by causing surface degradation or pitting, which can act as stress concentrators and initiate cracks.
-
Design and Manufacturing Considerations:
- The design of the brazed joint plays a crucial role in its fatigue resistance. Joints with smooth transitions and minimal stress concentrators are less likely to fail due to fatigue.
- Proper control of the brazing process, including temperature, time, and filler material selection, is essential to minimize residual stresses and ensure a strong bond between the base metal and the filler material.
-
Prevention and Mitigation Strategies:
- To mitigate fatigue failure in brazed joints, it is important to design joints with smooth geometries and avoid sharp corners or abrupt changes in cross-section.
- Using filler materials with thermal expansion coefficients closely matching those of the base metal can help reduce residual stresses.
- Post-brazing treatments, such as stress relief annealing, can be employed to reduce residual stresses and improve the fatigue life of the joint.
- Regular inspection and maintenance can help detect early signs of fatigue cracking, allowing for timely intervention before catastrophic failure occurs.
In summary, fatigue failure in brazed joints is a complex phenomenon influenced by stress concentration, material properties, cyclic loading, and environmental conditions. Understanding these factors and implementing appropriate design and manufacturing strategies can significantly enhance the fatigue resistance of brazed joints.
Summary Table:
Key Factors | Impact on Fatigue Failure |
---|---|
Stress Concentration | Geometric discontinuities and weak interfaces act as stress concentrators, promoting cracks. |
Material Properties | Mismatched thermal expansion coefficients induce residual stresses, reducing fatigue strength. |
Cyclic Loading | Repeated stresses below tensile strength cause crack initiation and propagation. |
Environmental Conditions | Temperature fluctuations and corrosion accelerate fatigue by inducing additional stresses. |
Design & Manufacturing | Poor joint design and improper brazing processes increase susceptibility to fatigue. |
Prevention Strategies | Smooth geometries, matching materials, stress relief, and regular inspections mitigate risks. |
Need help enhancing the fatigue resistance of your brazed joints? Contact our experts today for tailored solutions!