Rotary kilns are a critical component in industrial processes such as cement production, where chains play a vital role in optimizing the efficiency and functionality of the kiln. These chains are strategically placed inside the kiln to address several operational challenges, including moisture removal, material transport, and temperature regulation. By understanding the purpose of these chains, we can appreciate their importance in maintaining the kiln's performance and ensuring the quality of the final product.
Key Points Explained:
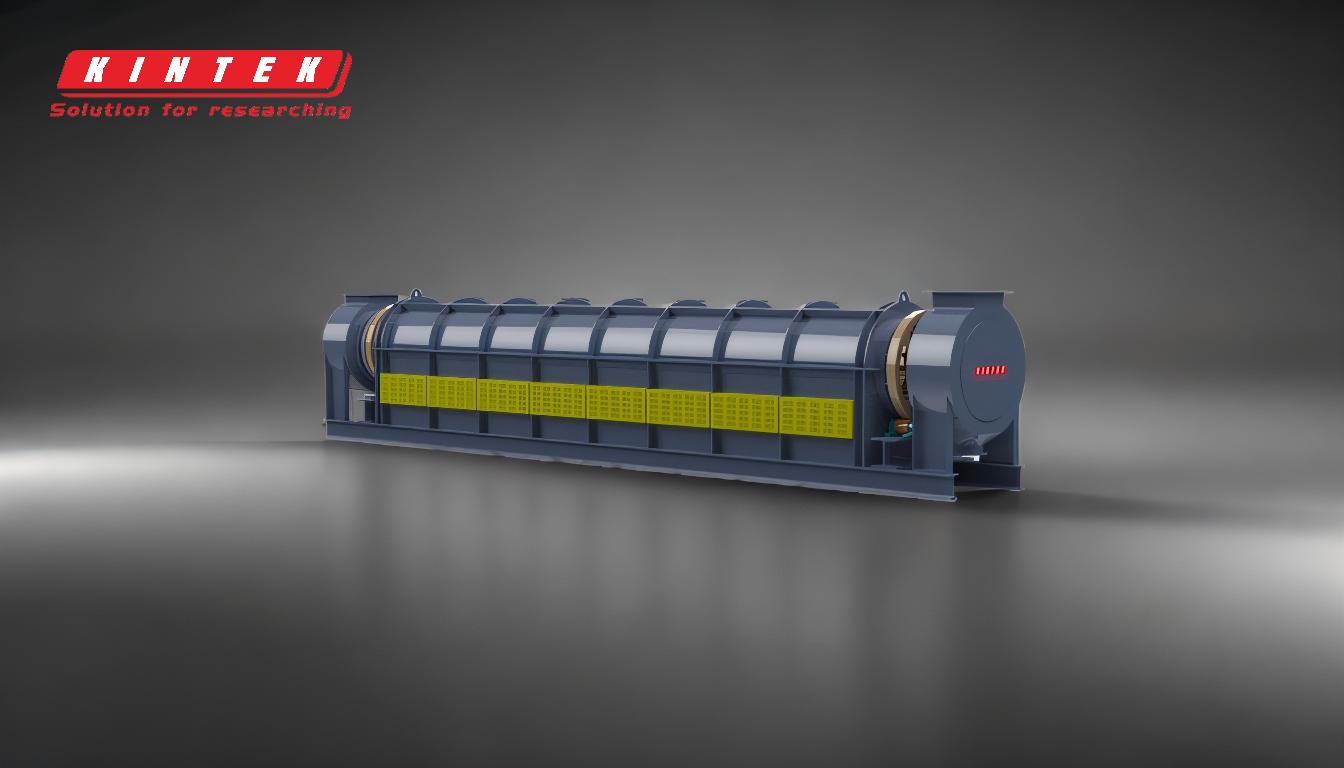
-
Moisture Removal from Raw Materials:
- In wet and long-dry rotary kilns, raw cement materials (often referred to as "mud") contain significant moisture that must be removed before the material can undergo further processing.
- Chains inside the kiln act as heat exchangers, increasing the surface area exposed to the hot gases. This accelerates the evaporation of moisture from the raw materials, ensuring they are sufficiently dry before reaching the high-temperature zones of the kiln.
-
Cleaning the Kiln Shell:
- As the kiln rotates, the chains scrape against the inner shell, preventing the buildup of material deposits. This self-cleaning mechanism reduces the risk of blockages and ensures consistent heat transfer throughout the kiln.
- By keeping the kiln shell clean, the chains help maintain optimal thermal efficiency and prevent uneven heating, which could compromise the quality of the final product.
-
Transporting Materials:
- The chains assist in moving the raw materials through the kiln. As the kiln rotates, the chains lift and drop the material, promoting mixing and ensuring uniform exposure to heat.
- This tumbling action is crucial for achieving consistent chemical reactions and physical changes in the material, such as the formation of clinker in cement production.
-
Crushing Mud Rings:
- Mud rings are hardened deposits that can form inside the kiln, obstructing material flow and reducing efficiency. The chains help break up these rings, preventing them from causing operational disruptions.
- This function is particularly important in maintaining the kiln's throughput and ensuring uninterrupted production.
-
Reducing Dust Amount:
- The chains help agglomerate fine particles into larger clumps, reducing the amount of dust carried out of the kiln by the exhaust gases.
- This not only improves the quality of the exhaust gases but also minimizes material loss, enhancing the overall efficiency of the process.
-
Reducing Kiln Exit Gas Temperature:
- By increasing the heat transfer efficiency, the chains help lower the temperature of the gases exiting the kiln. This reduces energy waste and ensures that more heat is utilized in the process.
- Lower exit gas temperatures also reduce the thermal load on downstream equipment, such as exhaust fans and pollution control systems.
-
Enhancing Thermal Efficiency:
- The chains improve the kiln's thermal efficiency by ensuring that heat is evenly distributed and effectively transferred to the raw materials.
- This is critical for achieving the precise temperature profiles required for chemical reactions, such as the calcination of limestone in cement production.
-
Supporting the Kiln's Rotational Dynamics:
- The chains contribute to the kiln's rotational dynamics by helping to distribute the material evenly across the cross-section of the drum.
- This even distribution prevents localized overheating or underheating, ensuring consistent product quality.
In summary, the chains inside a rotary kiln serve multiple functions that are essential for the efficient and effective operation of the kiln. From moisture removal and material transport to temperature regulation and dust reduction, these chains play a critical role in maintaining the kiln's performance and ensuring the quality of the final product. Understanding their purpose helps equipment and consumable purchasers appreciate the importance of selecting the right chains for their specific kiln applications.
Summary Table:
Function | Purpose |
---|---|
Moisture Removal | Accelerates evaporation of moisture from raw materials. |
Cleaning the Kiln Shell | Prevents material buildup and ensures consistent heat transfer. |
Transporting Materials | Promotes mixing and uniform heat exposure for consistent reactions. |
Crushing Mud Rings | Breaks up hardened deposits to maintain material flow and efficiency. |
Reducing Dust Amount | Agglomerates fine particles to minimize dust and material loss. |
Reducing Kiln Exit Gas Temperature | Lowers gas temperature, reducing energy waste and thermal load. |
Enhancing Thermal Efficiency | Ensures even heat distribution for precise chemical reactions. |
Supporting Rotational Dynamics | Distributes material evenly to prevent overheating or underheating. |
Looking to optimize your rotary kiln's performance? Contact our experts today to find the right chains for your needs!