Electric arc furnaces (EAFs) offer several advantages over blast furnaces, making them a preferred choice in many industrial applications. They are cost-effective, require less space, and provide higher efficiency in terms of temperature control and production speed. EAFs also allow for quicker preparation of work specimens and maintain a high degree of purity. While induction furnaces may heat faster and have higher thermal efficiency, EAFs are still favored for their simplicity and ease of operation. Overall, the benefits of EAFs make them a superior option in various manufacturing processes.
Key Points Explained:
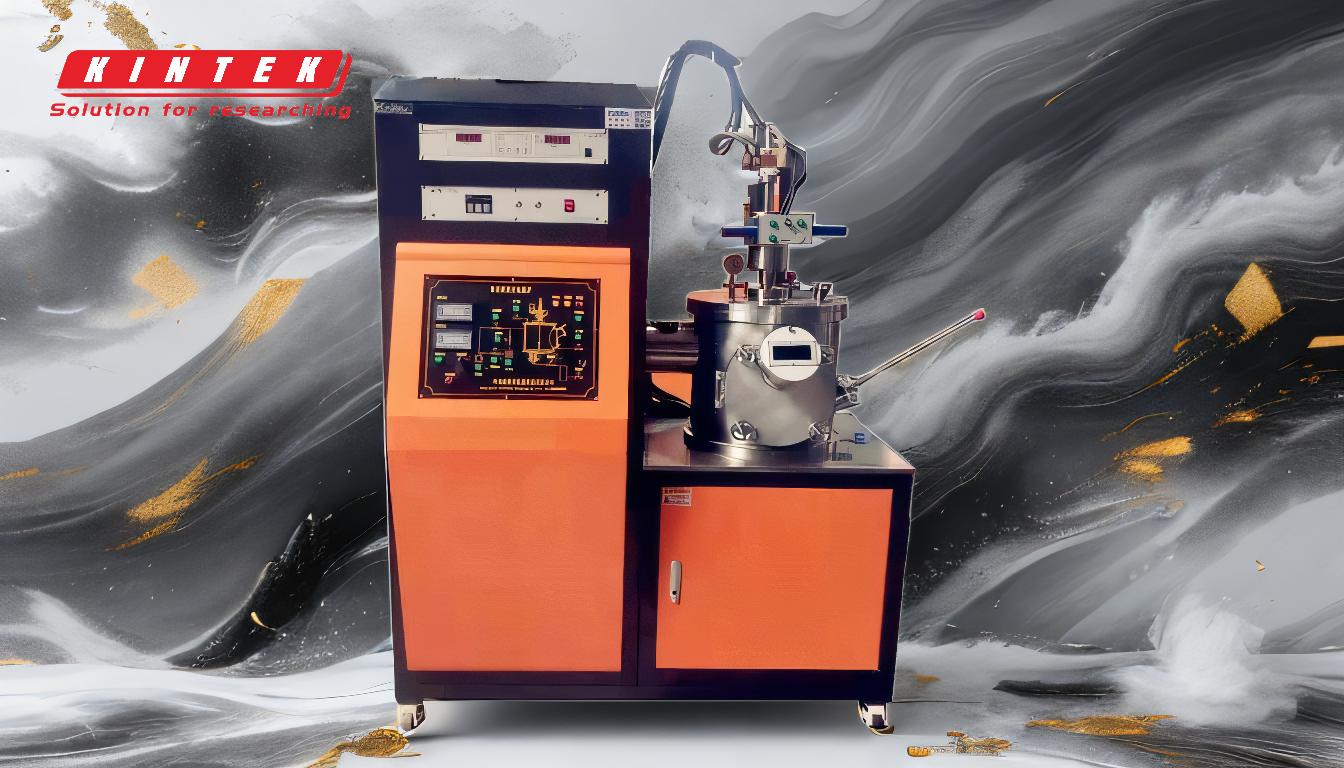
-
Cost Efficiency:
- Lower Initial Cost: EAFs are generally less expensive to install compared to blast furnaces. This makes them more accessible for smaller operations or those with budget constraints.
- Space Saving: EAFs take up less space in a factory, which can be a significant advantage in facilities where space is at a premium.
-
Operational Efficiency:
- Faster Heating: EAFs can reach higher temperatures much faster than blast furnaces. This rapid heating capability allows for quicker melting and production cycles, enhancing overall productivity.
- Precise Temperature Control: EAFs offer more precise control over the temperature, which is crucial for producing high-quality products with consistent properties.
-
Simplicity and Ease of Use:
- Simpler Design: The single arc furnace design is straightforward, making it easier to operate and maintain. This simplicity can reduce downtime and lower maintenance costs.
- Ease of Access: The design allows for easy access into the furnace, facilitating quicker preparation of work specimens and easier maintenance.
-
Purity and Quality:
- High Purity Levels: EAFs maintain a very high degree of purity in the materials being processed. This is essential for industries where material purity is critical, such as in the production of high-grade steels.
- Quick Specimen Preparation: The ability to quickly prepare work specimens is another advantage, allowing for faster turnaround times in production and testing.
-
Comparison with Induction Furnaces:
- Thermal Efficiency: While induction furnaces heat faster and have higher thermal efficiency due to direct heating within the liquid steel, EAFs still hold their own due to their operational simplicity and ease of use.
- Heat Loss: EAFs do lose some heat through the furnace cover and walls, but this is often mitigated by their other advantages, such as cost and space efficiency.
In summary, electric arc furnaces provide a balanced combination of cost efficiency, operational efficiency, simplicity, and high-quality output, making them a better choice than blast furnaces in many scenarios.
Summary Table:
Advantage | Description |
---|---|
Cost Efficiency | Lower initial cost and space-saving design. |
Operational Efficiency | Faster heating and precise temperature control for high-quality output. |
Simplicity and Ease of Use | Simple design, easy access, and reduced maintenance costs. |
Purity and Quality | High material purity and quick specimen preparation for faster production cycles. |
Comparison with Induction Furnaces | Balanced performance despite slightly lower thermal efficiency. |
Ready to upgrade your industrial processes with electric arc furnaces? Contact us today to learn more!