Multi-stage furnaces, particularly two-stage models, are often worth the investment for homeowners looking for long-term energy savings and enhanced comfort. These furnaces operate at two levels of heat output—low and high—which allows them to adjust their energy consumption based on the heating needs of the home. This flexibility not only reduces energy usage during milder weather but also ensures efficient heating during colder periods. Over time, the energy savings can offset the higher initial cost of a multi-stage furnace, making it a cost-effective choice for those planning to stay in their homes for many years.
Key Points Explained:
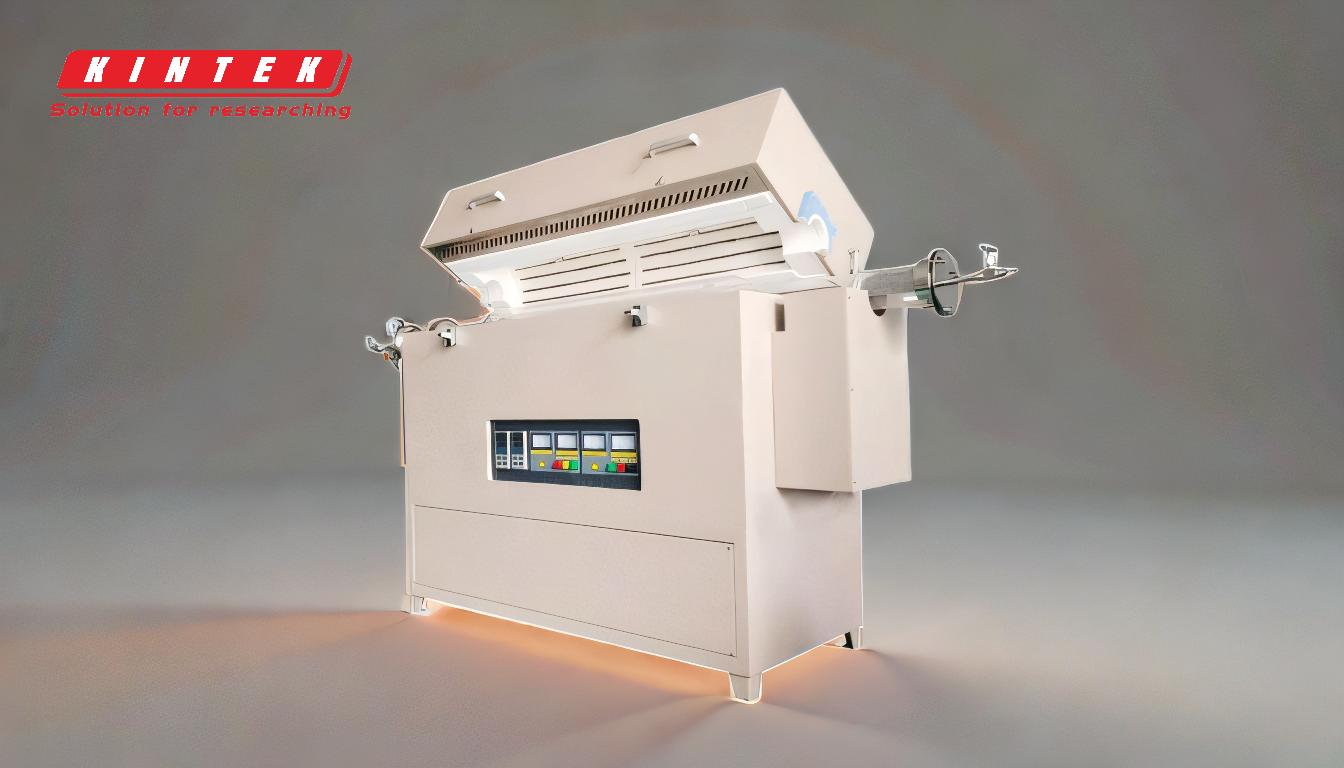
-
Energy Efficiency:
- Multi-stage furnaces operate at two levels of heat output: low and high.
- The low stage is used during milder weather, reducing energy consumption.
- The high stage is activated during colder periods, ensuring efficient heating.
- This dual-stage operation leads to significant energy savings over time.
-
Cost Savings:
- Although multi-stage furnaces have a higher initial cost, their energy efficiency leads to lower operating costs.
- Over many years, the savings on heating bills can amount to hundreds of dollars.
- These savings can eventually offset the higher upfront investment, making multi-stage furnaces a cost-effective option in the long run.
-
Enhanced Comfort:
- Multi-stage furnaces provide more consistent heating by adjusting their output to match the heating needs of the home.
- This results in fewer temperature fluctuations and a more comfortable living environment.
- The ability to operate at a lower stage for longer periods also reduces the frequency of on/off cycling, which can contribute to a quieter and more stable heating system.
-
Long-Term Investment:
- Multi-stage furnaces are particularly beneficial for homeowners who plan to stay in their homes for many years.
- The long-term energy savings and enhanced comfort make them a worthwhile investment for those looking to maximize the value of their heating system.
-
Environmental Impact:
- By using less energy, multi-stage furnaces contribute to lower greenhouse gas emissions.
- This makes them a more environmentally friendly option compared to single-stage furnaces.
- Homeowners who prioritize sustainability may find multi-stage furnaces to be a better choice for reducing their carbon footprint.
In conclusion, multi-stage furnaces offer a range of benefits that make them a worthwhile investment for many homeowners. Their energy efficiency, cost savings, enhanced comfort, and positive environmental impact make them a compelling choice, especially for those planning to stay in their homes for the long term.
Summary Table:
Benefit | Description |
---|---|
Energy Efficiency | Operates at low and high stages, reducing energy use in mild weather and ensuring efficient heating in cold weather. |
Cost Savings | Higher initial cost offset by long-term energy savings, reducing heating bills. |
Enhanced Comfort | Consistent heating with fewer temperature fluctuations and quieter operation. |
Long-Term Investment | Ideal for homeowners planning to stay long-term due to energy savings and comfort. |
Environmental Impact | Reduces greenhouse gas emissions, making it an eco-friendly heating option. |
Ready to upgrade to a multi-stage furnace? Contact us today to learn more and save on energy costs!