Sintered parts, particularly those made from powder metals like sintered steel, can indeed be machined, but they are generally considered less machinable compared to their wrought counterparts. This is due to their porous structure, which can lead to challenges such as tool wear, surface finish issues, and dimensional inaccuracies. However, advancements in powder metallurgy and machining techniques are continuously improving the machinability of sintered parts, making them more competitive in terms of machining costs and performance.
Key Points Explained:
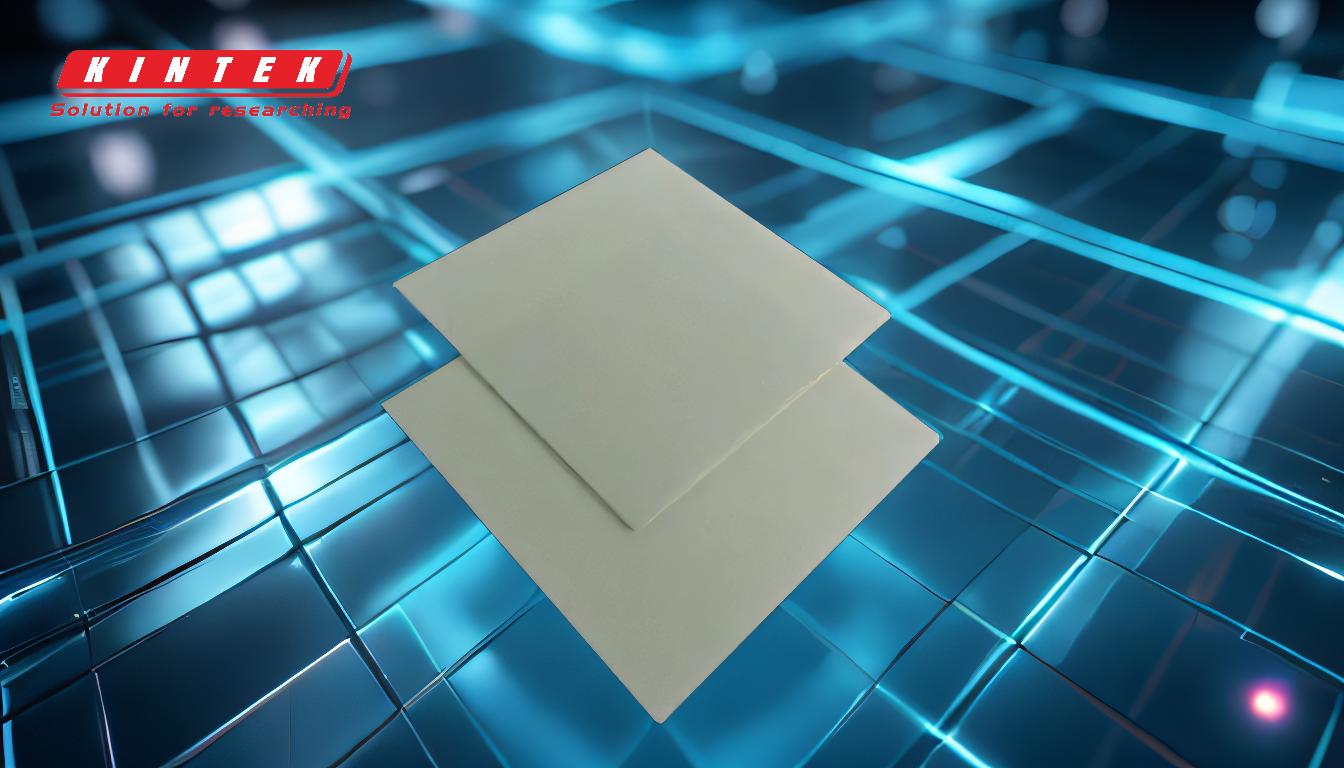
-
Machinability of Sintered Parts:
- Sintered parts, especially those made from powder metals, are inherently less machinable than wrought metals due to their porous structure. This porosity can cause issues such as tool wear, poor surface finish, and dimensional instability during machining.
- The metalworking industry recognizes these challenges and is actively working on improving the machinability of sintered parts to make them more competitive.
-
Challenges in Machining Sintered Parts:
- Tool Wear: The porosity in sintered parts can lead to uneven cutting forces, which accelerates tool wear. This is a significant concern as it increases machining costs and reduces tool life.
- Surface Finish: The porous nature of sintered materials can result in a rougher surface finish compared to wrought metals. This can be problematic for applications requiring high surface quality.
- Dimensional Accuracy: The inherent porosity can also lead to dimensional inaccuracies during machining, as the material may compress or deform under cutting forces.
-
Improvements in Machinability:
- Material Composition: Advances in powder metallurgy have led to the development of sintered materials with improved machinability. Additives such as manganese sulfide (MnS) are often used to enhance machinability by acting as a lubricant during the cutting process.
- Machining Techniques: Specialized machining techniques, such as using sharp cutting tools with appropriate geometries and coatings, can help mitigate some of the challenges associated with machining sintered parts. Additionally, optimizing cutting parameters (speed, feed, and depth of cut) can improve machining outcomes.
- Post-Sintering Treatments: Post-sintering treatments, such as heat treatment or surface densification, can improve the machinability of sintered parts by reducing porosity and increasing material density.
-
Cost Considerations:
- While sintered parts may initially present higher machining costs due to tool wear and other challenges, the overall cost-effectiveness can be improved through advancements in material science and machining techniques. This makes sintered parts a viable option for a wide range of applications, particularly where complex shapes or high-volume production is required.
-
Applications and Competitive Edge:
- Despite the challenges, sintered parts are widely used in industries such as automotive, aerospace, and electronics due to their ability to produce complex shapes with high precision and minimal material waste.
- The ongoing improvements in machinability are helping sintered parts to remain competitive with wrought metals, especially in applications where the benefits of powder metallurgy (such as cost savings in material and production) outweigh the machining challenges.
In conclusion, while sintered parts can be machined, they present unique challenges that require careful consideration of material properties, machining techniques, and cost factors. However, with ongoing advancements in powder metallurgy and machining technology, the machinability of sintered parts is continually improving, making them a competitive option in various industrial applications.
Summary Table:
Key Aspect | Details |
---|---|
Machinability | Less machinable than wrought metals due to porous structure. |
Challenges | Tool wear, surface finish issues, dimensional inaccuracies. |
Improvements | Advanced materials, specialized techniques, post-sintering treatments. |
Applications | Automotive, aerospace, electronics—complex shapes with minimal waste. |
Cost Considerations | Higher initial costs, but improvements enhance overall cost-effectiveness. |
Ready to explore machining solutions for sintered parts? Contact our experts today for tailored advice!