Diamond-like carbon (DLC) coatings are known for their exceptional hardness, low friction, and wear resistance, making them ideal for applications in automotive, machinery, medical, and decorative industries. However, DLC coatings are typically applied to metals, ceramics, and other hard substrates due to their high-temperature deposition process and the need for strong adhesion. Coating plastics with DLC is challenging because most plastics cannot withstand the high temperatures and plasma conditions required for DLC deposition. Additionally, the adhesion of DLC to plastic surfaces is often poor due to the difference in thermal expansion coefficients and surface energy. While there are some specialized techniques and pretreatment methods that may allow DLC coating on certain high-temperature-resistant plastics, it is not a common or straightforward process.
Key Points Explained:
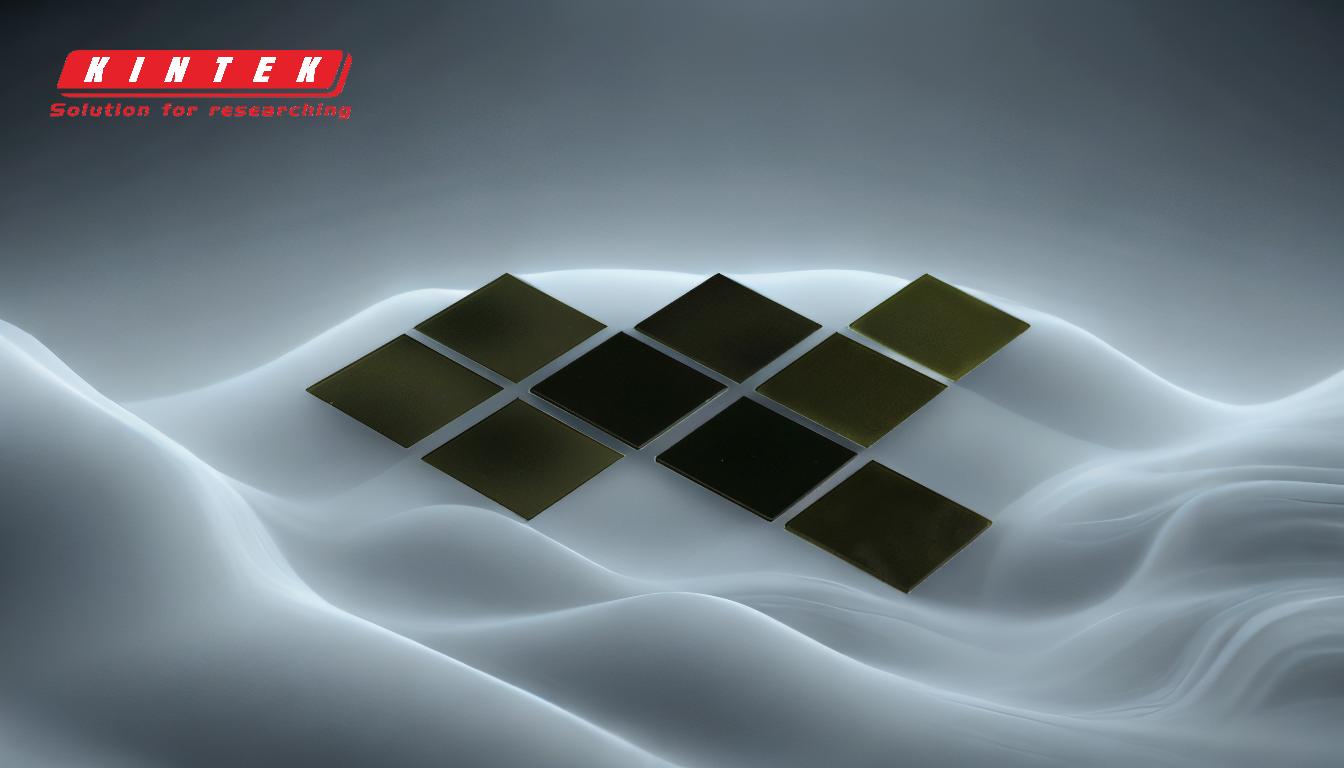
-
What is DLC Coating?
- DLC (Diamond-like Carbon) is an amorphous carbon coating that combines the hardness of diamond with the lubricity of graphite.
- It is characterized by a mix of Sp3 (diamond-like) and Sp2 (graphite-like) carbon bonds, resulting in high hardness (1500–3000 HV), low friction, and excellent wear resistance.
- DLC coatings are used in applications such as automotive components, medical implants, optical components, and decorative finishes.
-
Challenges of DLC Coating on Plastics
- High-Temperature Deposition Process: DLC coatings are typically deposited using plasma-enhanced chemical vapor deposition (PECVD) or physical vapor deposition (PVD) methods, which involve high temperatures. Most plastics cannot withstand these temperatures without deforming or degrading.
- Adhesion Issues: Plastics generally have lower surface energy and different thermal expansion coefficients compared to metals or ceramics, making it difficult for DLC coatings to adhere properly.
- Surface Preparation: Achieving strong adhesion on plastics often requires specialized surface pretreatment, such as plasma activation or the use of adhesion-promoting interlayers, which adds complexity to the process.
-
Potential Solutions for DLC Coating on Plastics
- High-Temperature-Resistant Plastics: Certain high-performance plastics, such as polyetheretherketone (PEEK) or polyimide, can withstand higher temperatures and may be suitable for DLC coating with proper surface treatment.
- Low-Temperature Deposition Techniques: Some advanced deposition methods, such as low-temperature PECVD, have been developed to reduce the thermal load on substrates, making it possible to coat temperature-sensitive materials like plastics.
- Adhesion Promoters: Using intermediate layers or adhesion-promoting materials can improve the bonding between DLC coatings and plastic surfaces.
-
Applications and Limitations
- Limited Applications: DLC coating on plastics is not widely used due to the challenges mentioned above. However, it may be feasible for specialized applications where the benefits of DLC (e.g., low friction, wear resistance) outweigh the difficulties.
- Alternative Coatings: For plastic components requiring similar properties, alternative coatings such as polymer-based or nanocomposite coatings may be more practical and cost-effective.
-
Conclusion
- While DLC coatings offer exceptional performance for hard substrates like metals and ceramics, coating plastics with DLC is complex and limited by material compatibility and process constraints. Specialized techniques and high-temperature-resistant plastics may enable some applications, but it remains a niche area compared to traditional DLC uses. For most plastic components, alternative coatings or surface treatments are more viable solutions.
Summary Table:
Aspect | Details |
---|---|
What is DLC Coating? | Amorphous carbon coating with high hardness, low friction, and wear resistance. |
Challenges on Plastics | High-temperature deposition, poor adhesion, and complex surface preparation. |
Potential Solutions | High-temperature-resistant plastics, low-temperature deposition, adhesion promoters. |
Applications | Limited to specialized uses; alternative coatings often preferred. |
Need expert advice on DLC coatings or alternative solutions for plastics? Contact us today!