Sintering is a process that significantly enhances the mechanical properties of materials, including hardness. By bonding and densifying particles through controlled heating and diffusion mechanisms, sintering reduces porosity and creates a dense, cohesive structure. This process not only improves strength and durability but also increases hardness, especially when combined with techniques like sinter hardening, which involves accelerated cooling rates to form martensitic microstructures. The resulting material exhibits superior performance characteristics, making sintering a critical step in achieving the desired hardness and overall mechanical integrity of components.
Key Points Explained:
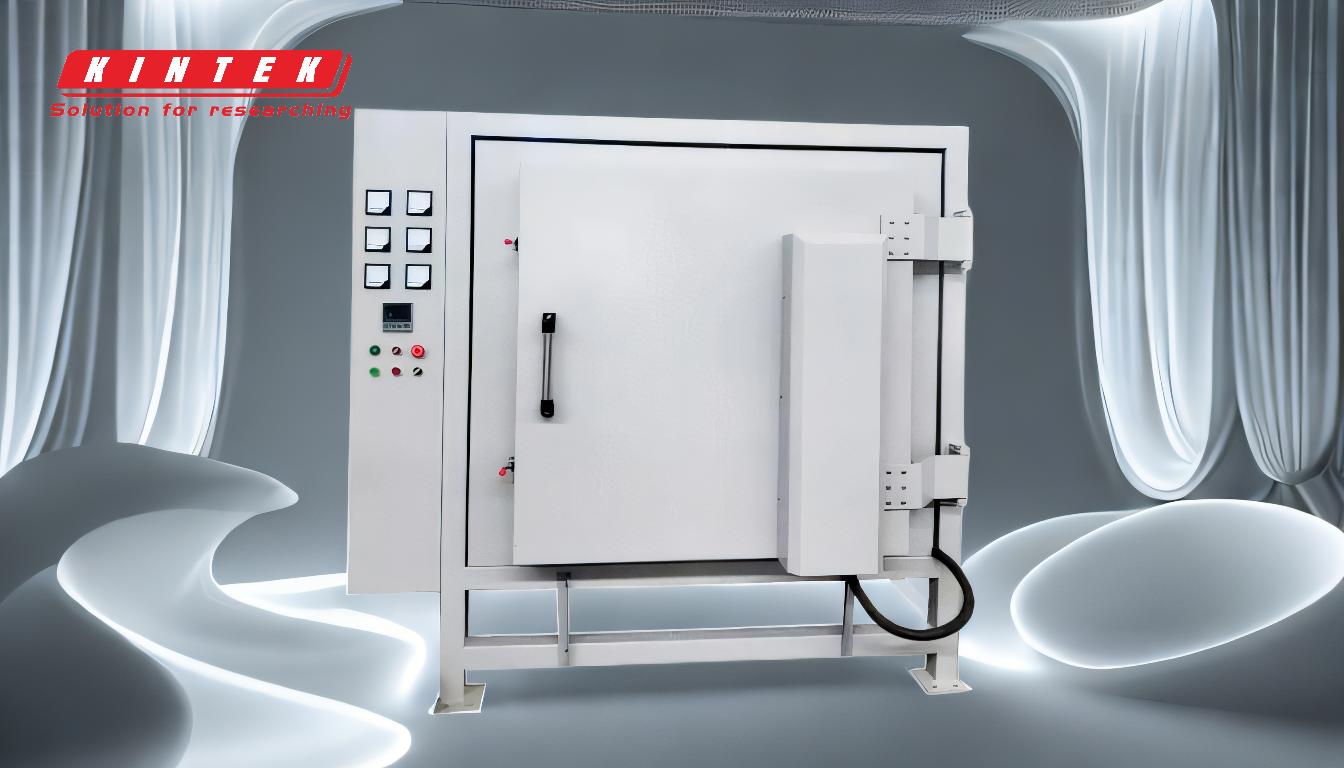
-
Sintering Reduces Porosity and Enhances Density:
- Sintering minimizes the porosity of a material's surface, leading to a denser structure. This reduction in porosity directly contributes to increased hardness, as fewer voids and defects in the material make it more resistant to deformation and wear.
-
Grain Size and Microstructural Changes:
- The sintering process affects the grain size, pore size, and grain boundary distribution in the material's microstructure. Smaller grain sizes and well-distributed grain boundaries generally result in higher hardness due to the increased resistance to dislocation movement within the material.
-
Sinter Hardening and Martensitic Transformation:
- Sinter hardening involves accelerated cooling rates during the sintering process, which promotes the formation of martensitic microstructures. Martensite is a hard, brittle phase that significantly increases the material's hardness. Subsequent tempering treatments can further enhance the material's strength and toughness without sacrificing hardness.
-
Improved Mechanical Properties:
- Sintering enhances not only hardness but also other mechanical properties such as strength, durability, and wear resistance. The bonding and densification of particles during sintering lead to a more cohesive and robust material structure, which is essential for applications requiring high hardness.
-
Energy Efficiency and Environmental Benefits:
- Sintering requires less energy compared to melting the same metal, making it an environmentally friendly option. This energy efficiency does not compromise the hardness or other mechanical properties of the material, making sintering a sustainable choice for enhancing material performance.
-
Consistency and Control in Manufacturing:
- The sintering process allows for greater control over the manufacturing process, resulting in more consistent products. This consistency ensures that the desired hardness and other properties are uniformly achieved across different batches of material, which is crucial for industrial applications.
In summary, sintering is a critical process that increases hardness by reducing porosity, refining microstructure, and enabling techniques like sinter hardening. These changes lead to materials with superior mechanical properties, making sintering an essential step in the production of high-performance components.
Summary Table:
Key Aspect | Impact on Hardness |
---|---|
Reduces Porosity | Minimizes voids and defects, leading to a denser, harder material. |
Refines Microstructure | Smaller grain sizes and well-distributed grain boundaries increase resistance to wear. |
Sinter Hardening | Accelerated cooling forms martensite, significantly boosting hardness. |
Improved Mechanical Properties | Enhances strength, durability, and wear resistance for high-performance applications. |
Energy Efficiency | Requires less energy than melting, making it a sustainable option for hardness enhancement. |
Manufacturing Consistency | Ensures uniform hardness and properties across batches for industrial reliability. |
Learn how sintering can optimize your material's hardness and performance—contact our experts today!