The synthesis of carbon nanotubes (CNTs) using the arc discharge method is one of the earliest and most well-established techniques. This method involves creating a high-temperature arc between two carbon electrodes in an inert gas environment, leading to the vaporization of carbon atoms and their subsequent condensation into CNTs. While newer methods like chemical vapor deposition (CVD) have become more commercially dominant, the arc discharge method remains significant due to its ability to produce high-quality CNTs, including single-walled and multi-walled varieties. This method is particularly noted for its simplicity and the high crystallinity of the resulting nanotubes.
Key Points Explained:
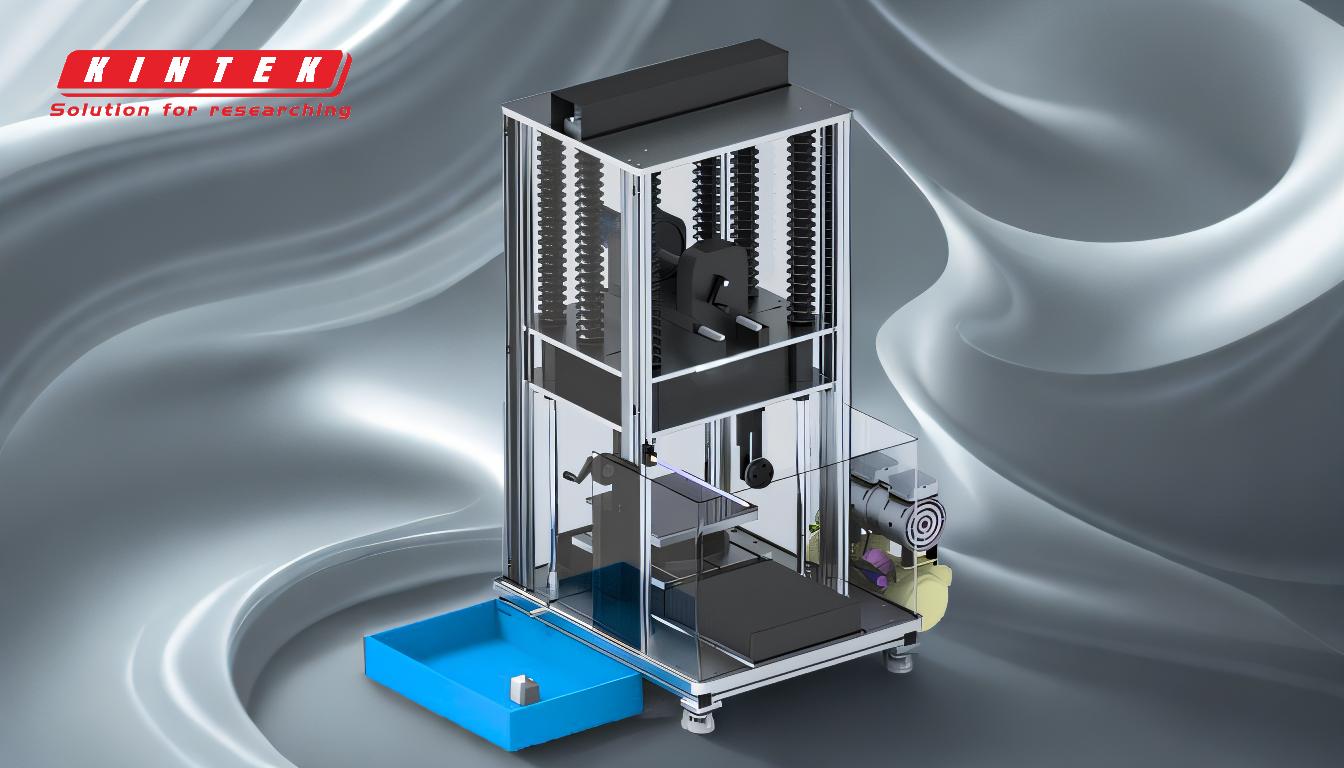
-
Principle of Arc Discharge Method:
- The arc discharge method relies on creating a high-temperature arc between two carbon electrodes. This arc generates temperatures high enough to vaporize carbon atoms from the anode.
- The process typically occurs in an inert gas atmosphere, such as helium or argon, to prevent oxidation and contamination of the carbon vapor.
- The vaporized carbon atoms then condense on the cooler surfaces, including the cathode, forming carbon nanotubes.
-
Equipment Setup:
- The setup includes a vacuum chamber filled with inert gas, two carbon electrodes (anode and cathode), and a power supply capable of generating a high-current arc.
- The anode is usually made of pure graphite, while the cathode can be made of graphite or a metal catalyst, depending on the desired type of CNTs (single-walled or multi-walled).
-
Process Parameters:
- Current and Voltage: The arc is typically maintained at a current of 50-100 A and a voltage of 20-30 V. These parameters are crucial for controlling the temperature and stability of the arc.
- Gas Pressure: The inert gas pressure is usually maintained between 100-500 Torr. This pressure helps in controlling the condensation rate of the carbon vapor.
- Electrode Distance: The distance between the electrodes is critical and is usually kept at a few millimeters to maintain a stable arc.
-
Formation of Carbon Nanotubes:
- During the arc discharge, carbon atoms are ejected from the anode and form a plasma. These atoms then condense on the cathode or other cooler surfaces.
- The presence of a metal catalyst (such as iron, cobalt, or nickel) on the cathode can facilitate the formation of single-walled carbon nanotubes (SWCNTs) by acting as nucleation sites.
- Without a catalyst, the process tends to produce multi-walled carbon nanotubes (MWCNTs).
-
Advantages of Arc Discharge Method:
- High-Quality CNTs: The arc discharge method is known for producing CNTs with high crystallinity and fewer defects compared to other methods.
- Simplicity: The equipment and process are relatively simple and do not require complex catalysts or precursors.
- Scalability: While not as scalable as CVD, the arc discharge method can still produce significant quantities of CNTs, especially for research purposes.
-
Challenges and Limitations:
- Yield and Purity: The yield of CNTs can be lower compared to CVD, and the product often contains impurities such as amorphous carbon and metal particles.
- Energy Consumption: The method is energy-intensive due to the high temperatures required to maintain the arc.
- Control Over CNT Type: While the method can produce both SWCNTs and MWCNTs, controlling the specific type and chirality of CNTs is more challenging compared to CVD.
-
Comparison with Other Methods:
- Laser Ablation: Similar to arc discharge, laser ablation also produces high-quality CNTs but is less efficient and more expensive due to the high energy requirements of the laser.
- Chemical Vapor Deposition (CVD): CVD is the most commercially dominant method due to its scalability, lower energy requirements, and better control over CNT type and structure. However, CNTs produced by CVD may have more defects compared to those produced by arc discharge.
-
Future Directions:
- Green Feedstocks: There is ongoing research into using alternative feedstocks, such as carbon dioxide captured by electrolysis in molten salts, to produce CNTs in a more environmentally friendly manner.
- Hybrid Products: Combining CNTs with other materials to create hybrid products with enhanced properties is another area of active research.
- Continuous Yarns: Developing methods to produce highly conductive continuous yarns from CNTs could open up new applications in electronics and materials science.
In summary, the arc discharge method remains a valuable technique for synthesizing high-quality carbon nanotubes, particularly for research and specialized applications. While it faces challenges in terms of yield, purity, and energy consumption, its simplicity and the superior quality of the produced CNTs ensure its continued relevance in the field of nanotechnology.
Summary Table:
Aspect | Details |
---|---|
Principle | High-temperature arc vaporizes carbon atoms in an inert gas environment. |
Equipment | Vacuum chamber, carbon electrodes, power supply, and inert gas. |
Process Parameters | Current: 50-100 A, Voltage: 20-30 V, Gas Pressure: 100-500 Torr. |
CNT Formation | Carbon vapor condenses on cooler surfaces, forming SWCNTs or MWCNTs. |
Advantages | High crystallinity, simplicity, and scalability for research. |
Challenges | Lower yield, impurities, high energy consumption, and limited control. |
Comparison | Superior quality vs. CVD and laser ablation but less scalable. |
Future Directions | Green feedstocks, hybrid products, and continuous yarns for new applications. |
Discover how the arc discharge method can enhance your research—contact our experts today for more insights!