To control the temperature of a resistance, various methods can be employed depending on the application and design requirements. These methods include adjusting the resistance value, varying the applied voltage, or modulating the power supply's on/off cycles. Each approach has its advantages and limitations, and the choice depends on factors such as power consumption, precision, and system complexity. Below, we explore these methods in detail, focusing on their principles, implementation, and practical considerations.
Key Points Explained:
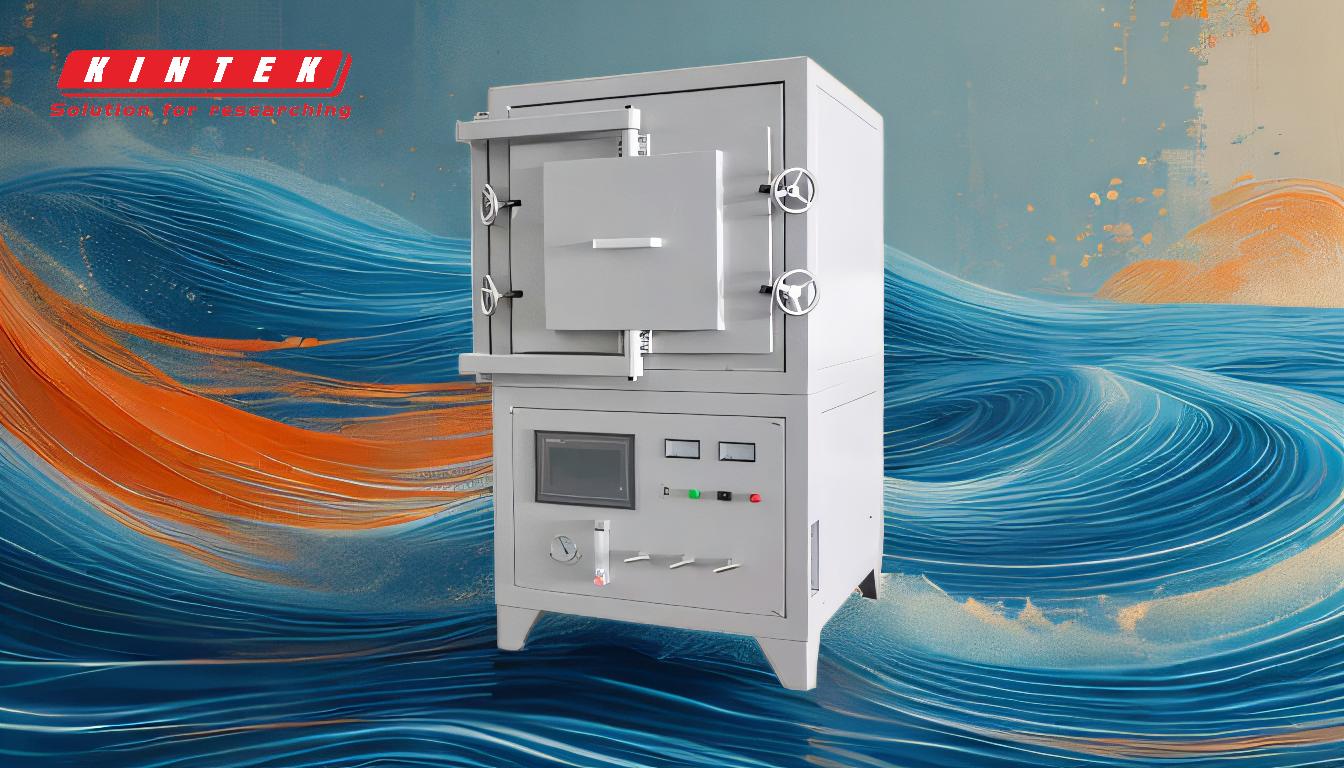
-
Adjusting the Resistance Value:
- Principle: By increasing the resistance value in a circuit, the power dissipated as heat (P = V²/R) can be reduced, thereby lowering the temperature. This is particularly useful in voltage divider circuits where power consumption is a concern.
- Implementation: Use higher-value resistors in the design. For example, in a voltage divider, increasing the resistor values reduces the current flow and, consequently, the heat generated.
-
Advantages:
- Reduces overall power consumption.
- Simplifies temperature control without requiring additional components.
-
Limitations:
- Limited by the maximum resistance value that can be practically used.
- May not provide fine-grained control over temperature.
-
Varying the Applied Voltage:
- Principle: The power dissipated by a resistor is proportional to the square of the voltage (P = V²/R). By adjusting the voltage, the temperature can be controlled.
-
Implementation:
- Use transformer tappings, auto-transformers, or induction regulators to adjust the voltage supplied to the resistance.
- In large systems, such as industrial furnaces, an independent generating set can provide a variable voltage supply.
-
Advantages:
- Provides precise control over temperature.
- Suitable for high-power applications like furnaces and ovens.
-
Limitations:
- Requires additional equipment (e.g., transformers or regulators).
- Increases system complexity and cost.
-
Modulating the Power Supply On/Off Cycles (Pulse Width Modulation - PWM):
- Principle: By varying the ratio of on and off times of the power supply, the average power delivered to the resistance can be controlled, thereby regulating the temperature.
-
Implementation:
- Use a PWM controller to switch the power supply on and off at a high frequency.
- Adjust the duty cycle (percentage of time the power is on) to control the average power.
-
Advantages:
- Highly efficient and precise.
- Reduces energy waste by delivering power only when needed.
-
Limitations:
- Requires a PWM controller and associated circuitry.
- May introduce electrical noise if not properly filtered.
-
Practical Considerations for Temperature Control:
- Thermal Management: Ensure proper heat dissipation to prevent overheating and maintain stable operation.
- Feedback Mechanisms: Use temperature sensors (e.g., thermocouples or RTDs) and feedback loops to monitor and adjust the temperature dynamically.
- System Design: Choose the method that best aligns with the application's power requirements, precision needs, and cost constraints.
-
Applications of Temperature Control in Resistances:
- Resistance Ovens and Furnaces: These systems often use voltage control or PWM to maintain precise temperatures for processes like annealing or heat treatment.
- Electronic Circuits: In voltage dividers or power resistors, adjusting resistance values or using PWM can help manage heat generation.
- Industrial Heating Systems: Large-scale systems may employ independent generating sets or advanced control systems for temperature regulation.
By understanding and applying these methods, you can effectively control the temperature of a resistance in various applications, ensuring optimal performance and energy efficiency.
Summary Table:
Method | Principle | Advantages | Limitations |
---|---|---|---|
Adjusting Resistance Value | Increase resistance to reduce heat (P = V²/R) | Reduces power consumption; simple implementation | Limited by max resistance; less precise control |
Varying Applied Voltage | Adjust voltage to control power (P = V²/R) | Precise control; suitable for high-power applications | Requires additional equipment; increases system complexity |
PWM (On/Off Cycles) | Vary power supply on/off ratio to control average power | Highly efficient; reduces energy waste | Requires PWM controller; may introduce electrical noise |
Need help implementing temperature control for your resistance systems? Contact our experts today for tailored solutions!