Using an induction heater involves understanding its working principles, selecting the right equipment, and following a structured process to ensure efficient and safe operation. Induction heating is a non-contact method that uses electromagnetic induction to generate heat within conductive materials, making it ideal for applications like metal melting, alloy creation, and industrial heating. The process requires selecting the appropriate coil size, securing the coil, and applying heat for a controlled duration. Below, we break down the key steps and considerations for using an induction heater effectively.
Key Points Explained:
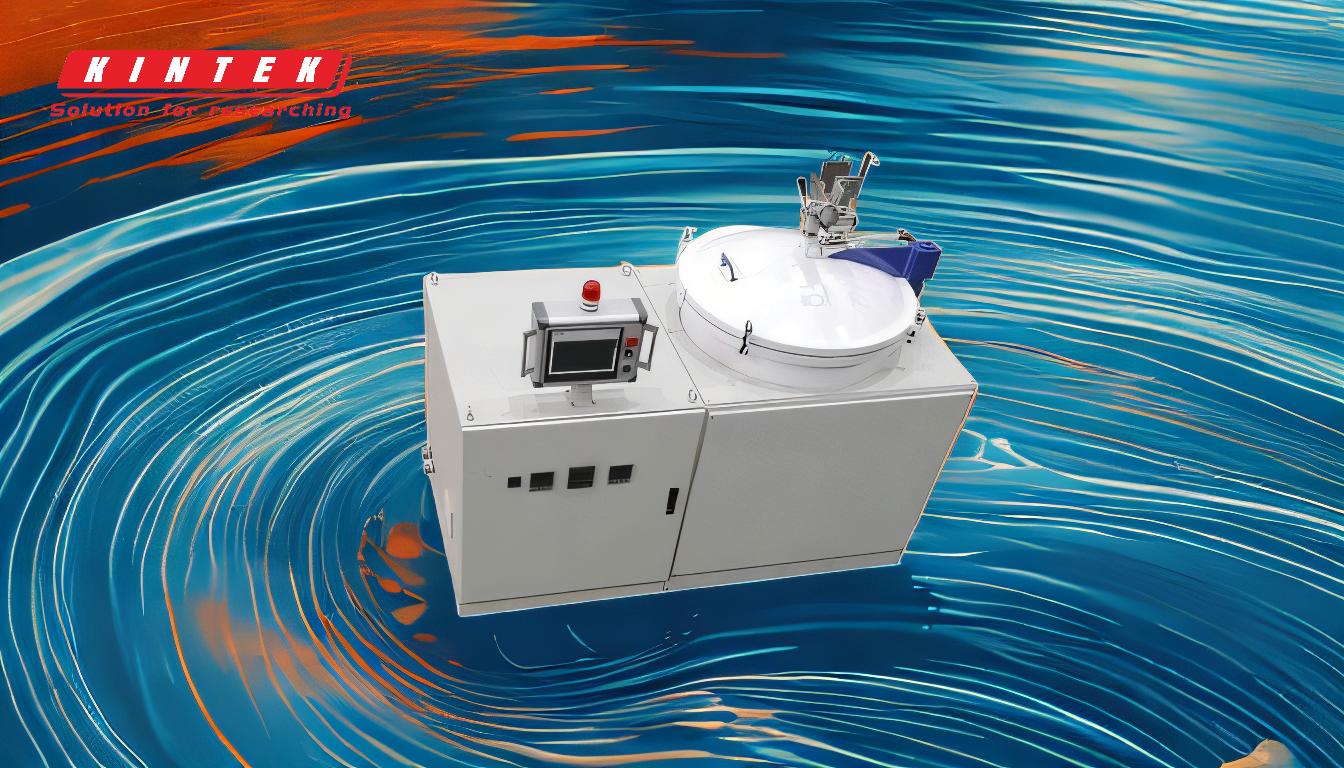
-
Understanding the Working Principle of Induction Heating
- Induction heating relies on electromagnetic induction and Joule heating.
- An alternating current (AC) passes through a copper coil, creating a powerful electromagnetic field.
- When a conductive material (e.g., metal) is placed within this field, eddy currents are induced within the material.
- These eddy currents flow against the material's resistivity, generating heat through Joule heating.
- This process is non-contact, ensuring efficient and uniform heating without direct flame or physical contact.
- Induction heating relies on electromagnetic induction and Joule heating.
-
Selecting the Right Induction Coil
- The induction coil is a critical component that determines the efficiency and effectiveness of the heating process.
- Coil Size: Choose a coil that fits the size and shape of the material being heated. A properly sized coil ensures optimal heat distribution and minimizes energy loss.
- Coil Shape: Coils can be customized (e.g., helical, pancake, or cylindrical) to match specific applications, such as heating small components or large industrial parts.
- A mismatched coil can lead to uneven heating, energy inefficiency, or damage to the material.
- The induction coil is a critical component that determines the efficiency and effectiveness of the heating process.
-
Securing the Induction Coil
- Properly securing the coil is essential for safety and performance.
- Ensure the coil is firmly attached to the induction heater to prevent movement during operation.
- Use appropriate fixtures or clamps to hold the coil in place, especially for high-power applications.
- A loose coil can cause arcing, uneven heating, or equipment failure.
- Properly securing the coil is essential for safety and performance.
-
Applying Heat for the Correct Duration
- The duration of heat application depends on the material and the desired outcome (e.g., softening, melting, or bonding).
- For most applications, heat is applied for 5 to 20 seconds.
- Monitor the material's response to determine if additional heating is required.
- Overheating can damage the material or the coil, while insufficient heating may not achieve the desired result.
- The duration of heat application depends on the material and the desired outcome (e.g., softening, melting, or bonding).
-
Safety Considerations
- Induction heating involves high temperatures and electromagnetic fields, requiring strict safety measures.
- Wear protective gear, such as heat-resistant gloves and safety goggles.
- Ensure the work area is well-ventilated and free of flammable materials.
- Regularly inspect the coil and equipment for signs of wear or damage.
- Proper safety practices prevent accidents and prolong the lifespan of the equipment.
- Induction heating involves high temperatures and electromagnetic fields, requiring strict safety measures.
-
Applications of Induction Heating
- Induction heaters are versatile and used in various industries:
- Industrial: Melting metals, forging, brazing, and heat treatment.
- Medical: Sterilization of instruments and precision heating for medical devices.
- Domestic: Cooktops and portable heaters.
- The non-contact nature of induction heating makes it ideal for applications requiring precise temperature control and clean heating.
- Induction heaters are versatile and used in various industries:
-
Energy Efficiency and Environmental Benefits
- Induction heating is highly efficient compared to traditional methods like flame or resistance heating.
- Heat is generated directly within the material, reducing energy loss.
- The process produces minimal emissions, making it environmentally friendly.
- These advantages make induction heating a preferred choice for modern industrial and domestic applications.
- Induction heating is highly efficient compared to traditional methods like flame or resistance heating.
By following these steps and understanding the principles of induction heating, users can effectively operate induction heaters for a wide range of applications. Proper coil selection, secure setup, and controlled heat application are key to achieving optimal results while ensuring safety and efficiency.
Summary Table:
Key Step | Description |
---|---|
Understand Induction Heating | Learn how electromagnetic induction and Joule heating generate heat efficiently. |
Select the Right Coil | Choose the correct coil size and shape for optimal heat distribution. |
Secure the Coil | Ensure the coil is firmly attached to prevent movement and ensure safety. |
Apply Heat Correctly | Monitor heat duration (5-20 seconds) to avoid overheating or underheating. |
Follow Safety Measures | Use protective gear and inspect equipment regularly to prevent accidents. |
Explore Applications | Discover uses in industrial, medical, and domestic settings. |
Energy Efficiency | Benefit from reduced energy loss and minimal emissions. |
Ready to optimize your heating process? Contact our experts today for personalized guidance!