Heat significantly affects the strength of materials, primarily by altering their molecular or atomic structure, which in turn influences their mechanical properties. At elevated temperatures, materials generally experience reduced strength, increased ductility, and changes in other mechanical properties due to thermal expansion, phase transitions, and increased atomic mobility. The extent of these changes depends on the material type, temperature range, and duration of exposure. For example, metals may soften and lose yield strength, while polymers may undergo thermal degradation or melting. Understanding these effects is crucial for selecting materials in high-temperature applications, such as aerospace, automotive, and industrial equipment.
Key Points Explained:
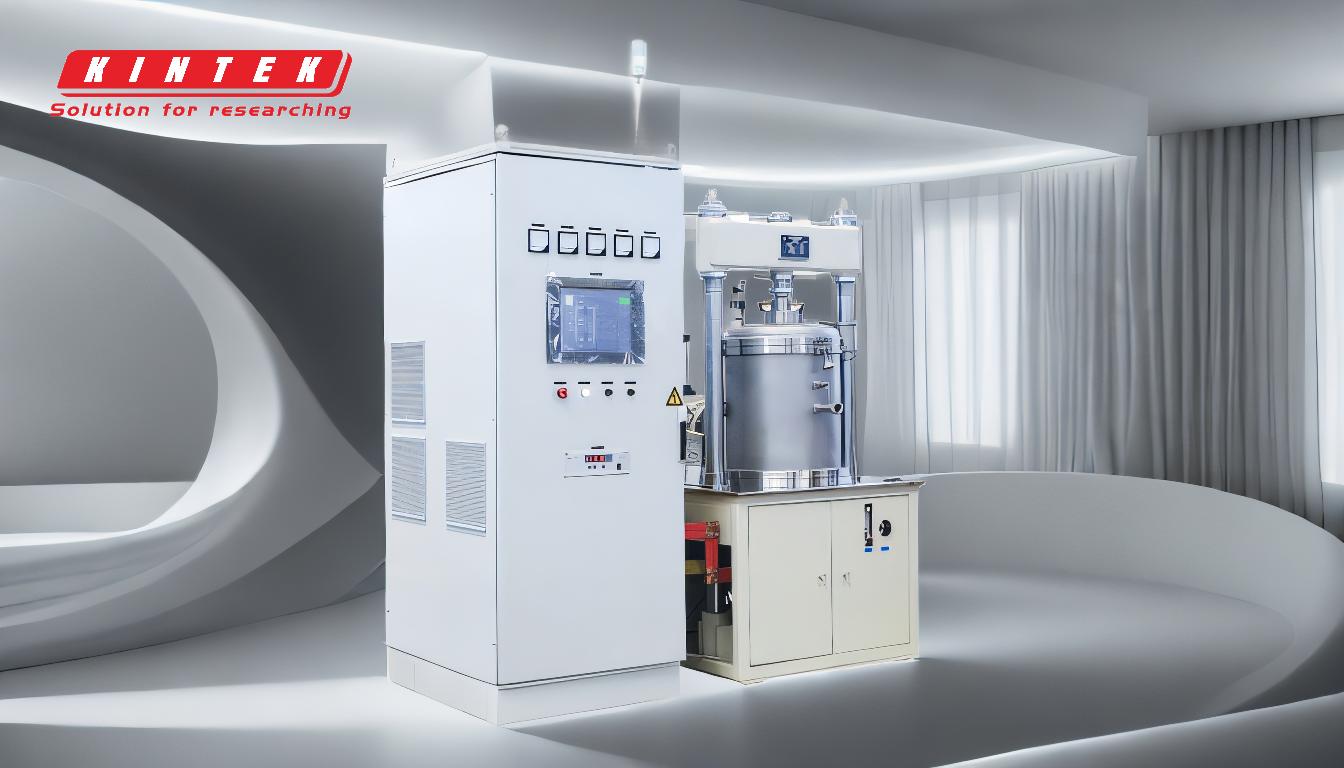
-
Thermal Expansion and Stress:
- When materials are heated, they expand due to increased atomic vibrations. This thermal expansion can lead to internal stresses, especially in constrained systems, potentially causing deformation or failure.
- Example: In metals, thermal expansion can lead to warping or cracking if the material is not allowed to expand freely.
-
Reduction in Yield Strength:
- As temperature increases, the yield strength of most materials decreases. This is because higher temperatures reduce the material's resistance to plastic deformation.
- Example: Steel, which is strong at room temperature, becomes softer and more pliable at high temperatures, making it easier to shape but less capable of bearing heavy loads.
-
Increased Ductility:
- Materials generally become more ductile at higher temperatures, meaning they can undergo more plastic deformation before fracturing.
- Example: Aluminum alloys, which are already ductile at room temperature, become even more so when heated, allowing for easier forming processes like extrusion or rolling.
-
Phase Transitions:
- Some materials undergo phase transitions (e.g., solid to liquid or changes in crystal structure) at specific temperatures, which can drastically alter their mechanical properties.
- Example: Polymers may melt or undergo glass transition, leading to a loss of structural integrity.
-
Creep and Stress Relaxation:
- At elevated temperatures, materials may experience creep, a slow, time-dependent deformation under constant stress. Stress relaxation, where stress decreases over time under constant strain, can also occur.
- Example: In turbine blades made of nickel-based superalloys, creep is a critical factor that limits their operational lifespan at high temperatures.
-
Thermal Degradation:
- Prolonged exposure to high temperatures can cause chemical changes in materials, such as oxidation or decomposition, leading to a loss of strength and other properties.
- Example: Polymers like PVC can degrade and release harmful gases when exposed to high temperatures, reducing their mechanical strength and usability.
-
Material-Specific Behavior:
- Different materials respond differently to heat. Metals, ceramics, polymers, and composites each have unique thermal properties and degradation mechanisms.
- Example: Ceramics generally retain their strength at high temperatures better than metals but are brittle and can fracture under thermal shock.
-
Design Considerations for High-Temperature Applications:
- Engineers must consider the thermal properties of materials when designing components for high-temperature environments. This includes selecting materials with high melting points, low thermal expansion coefficients, and good thermal stability.
- Example: In aerospace applications, materials like titanium alloys and carbon-carbon composites are chosen for their ability to withstand extreme temperatures without significant loss of strength.
Understanding how heat affects material strength is essential for ensuring the reliability and safety of components in high-temperature environments. By considering factors like thermal expansion, phase transitions, and material-specific behaviors, engineers can make informed decisions about material selection and design.
Summary Table:
Effect of Heat | Description | Example |
---|---|---|
Thermal Expansion and Stress | Materials expand due to increased atomic vibrations, causing internal stresses. | Metals may warp or crack if not allowed to expand freely. |
Reduction in Yield Strength | Higher temperatures reduce resistance to plastic deformation. | Steel becomes softer and less capable of bearing heavy loads. |
Increased Ductility | Materials become more ductile, allowing more plastic deformation before fracture. | Aluminum alloys become easier to extrude or roll when heated. |
Phase Transitions | Changes in crystal structure or state (e.g., solid to liquid) alter properties. | Polymers may melt or lose structural integrity. |
Creep and Stress Relaxation | Slow deformation under constant stress or reduced stress under constant strain. | Nickel-based superalloys in turbine blades experience creep at high temps. |
Thermal Degradation | Chemical changes like oxidation or decomposition reduce strength. | PVC degrades and releases harmful gases at high temperatures. |
Material-Specific Behavior | Metals, ceramics, polymers, and composites respond differently to heat. | Ceramics retain strength but are prone to thermal shock fractures. |
Design Considerations | Select materials with high melting points, low thermal expansion, and stability. | Titanium alloys and carbon-carbon composites are used in aerospace. |
Need help selecting materials for high-temperature applications? Contact our experts today for tailored solutions!