Hot isostatic pressing (HIP) is a manufacturing process that combines high temperature and high pressure to improve the properties of materials, particularly metals and ceramics. It works by applying uniform pressure from all directions using an inert gas, such as argon, within a pressurized vessel. Simultaneously, heat is applied to the material, typically below its melting point, to enhance densification and eliminate porosity. This process is widely used in industries like aerospace, automotive, and medical devices to produce components with high strength, uniformity, and reliability. The steps involved include powder preparation, cladding, degassing, pressing, and post-processing. A related variant, the warm isostatic press, operates at lower temperatures and is often used in battery manufacturing to ensure safety and stability.
Key Points Explained:
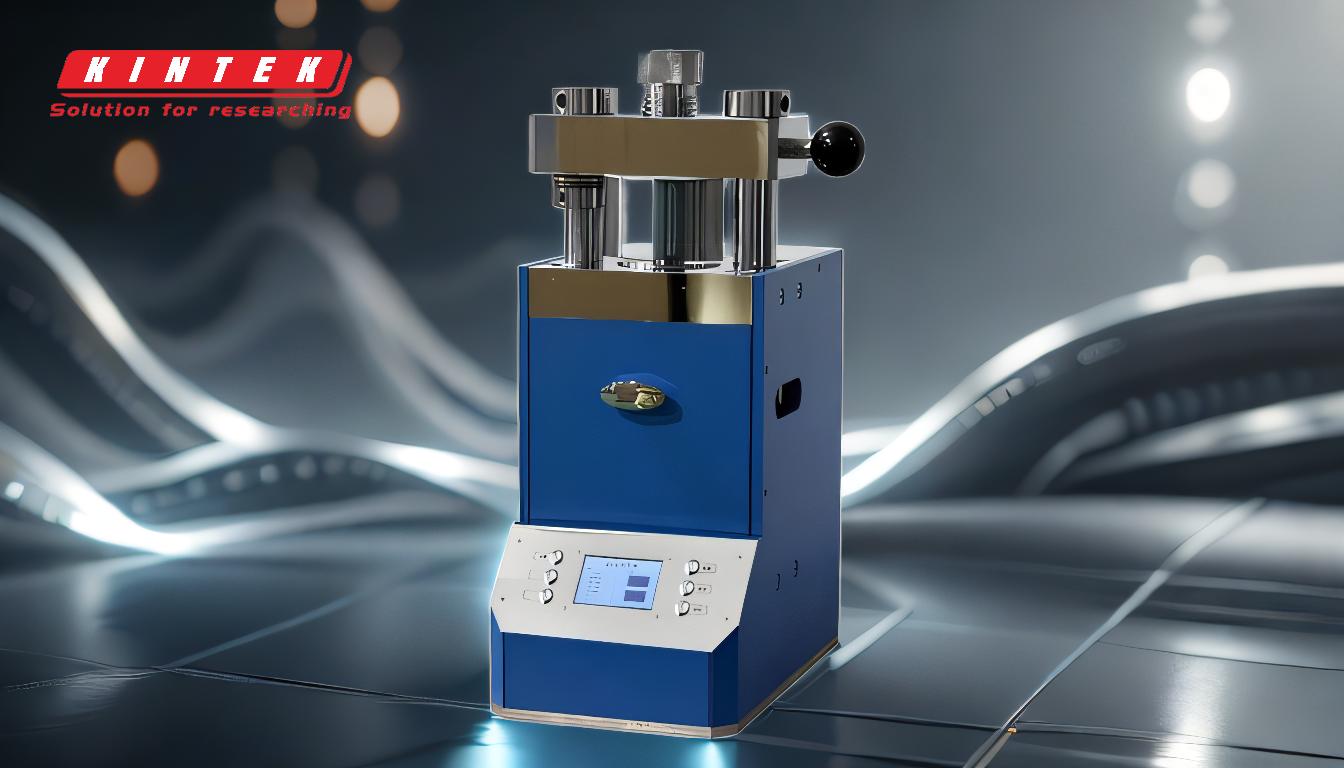
-
Definition and Purpose of Hot Isostatic Pressing (HIP):
- HIP is a process that applies uniform pressure and heat to materials to improve their density, strength, and uniformity.
- It is used to eliminate porosity, enhance mechanical properties, and produce high-performance components in industries like aerospace and medical devices.
-
How HIP Works:
- Pressure Application: A uniform hydrostatic pressure is applied to the material using an inert gas, such as argon, within a pressurized vessel. This pressure is transmitted equally from all directions.
- Heat Application: The material is heated below its melting point to facilitate densification and bonding of particles.
- Simultaneous Action: The combination of heat and pressure ensures the elimination of internal voids (pores) and improves material integrity.
-
Key Steps in the HIP Process:
- Powder Preparation: Raw materials are prepared in powder form.
- Cladding Design and Manufacturing: The powder is enclosed in a flexible mold or cladding to maintain shape during pressing.
- Degassing and Sealing: Air and gases are removed from the mold to prevent defects.
- Hot Isostatic Pressing: The material is subjected to high pressure and temperature in the HIP chamber.
- Post-Processing: After pressing, the cladding is removed, and the material undergoes additional processing, such as machining or heat treatment.
-
Applications of HIP:
- Aerospace: Production of turbine blades and other high-strength components.
- Medical Devices: Manufacturing of implants with high biocompatibility and durability.
- Automotive: Creation of lightweight, high-performance parts.
-
Comparison with Warm Isostatic Pressing:
- A warm isostatic press operates at lower temperatures compared to HIP and is often used in battery manufacturing to ensure safety and stability by controlling internal temperature and pressure.
-
Advantages of HIP:
- Eliminates internal defects and porosity.
- Enhances material density and mechanical properties.
- Produces components with uniform composition and high reliability.
-
Challenges and Considerations:
- High equipment and operational costs.
- Requires precise control of temperature, pressure, and process time.
- Post-processing steps may be necessary to achieve final product specifications.
By understanding these key points, equipment and consumable purchasers can make informed decisions about implementing HIP or related processes like warm isostatic pressing in their manufacturing workflows.
Summary Table:
Key Aspect | Details |
---|---|
Definition | Combines high temperature and pressure to improve material properties. |
Process | Uniform pressure from inert gas + heat below melting point. |
Key Steps | Powder prep, cladding, degassing, pressing, post-processing. |
Applications | Aerospace, medical devices, automotive. |
Advantages | Eliminates porosity, enhances density, improves mechanical properties. |
Challenges | High costs, precise control required, additional post-processing. |
Discover how hot isostatic pressing can optimize your manufacturing process—contact our experts today!