Vacuum induction melting (VIM) is a specialized metallurgical process used to melt and refine metals under vacuum conditions. This method employs electromagnetic induction to generate heat within the metal, which is contained in a crucible surrounded by an induction coil. The vacuum environment ensures the removal of gas impurities and volatile elements, leading to high-purity alloys with enhanced mechanical and chemical properties. VIM is particularly useful for producing superalloys, magnetic materials, and other high-performance metals. The process involves precise control of active elements and the elimination of harmful impurities, making it a critical technique in industries requiring high-quality metal products.
Key Points Explained:
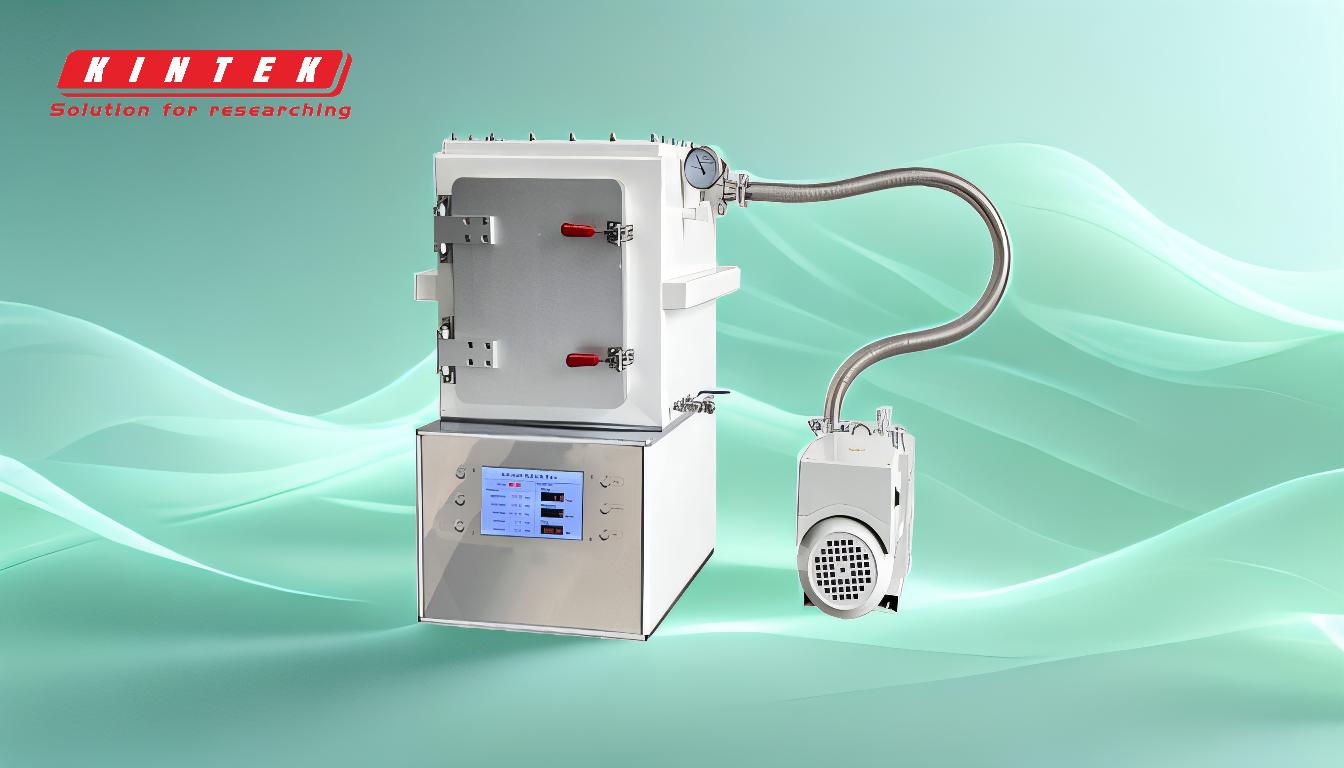
-
Principle of Electromagnetic Induction:
- The process relies on electromagnetic induction to generate heat. An alternating current passes through an induction coil, creating a magnetic field. This field induces eddy currents within the metal charge, which generate heat due to electrical resistance. The heat accumulates until the metal reaches its melting point.
- The induction coil is typically water-cooled to prevent overheating and maintain efficiency.
-
Vacuum Environment:
- The melting occurs in a vacuum, which is essential for removing gas impurities such as oxygen, nitrogen, and hydrogen. These elements can degrade the quality of the metal if not removed.
- The vacuum also facilitates the evaporation of volatile impurities like zinc, lead, and arsenic, further purifying the metal.
-
Furnace Design:
- The furnace is airtight and designed to withstand high vacuum conditions. It is lined with refractory materials that can endure the high temperatures and chemical reactions involved in the melting process.
- A common design is the batch vacuum induction melting furnace, which operates in a single chamber. This design requires breaking the vacuum to remove the ingot mold, making it suitable for cyclic operations.
-
Refining and Composition Control:
- VIM allows for precise control over the composition of the alloy. Active elements like aluminum, titanium, boron, and zirconium can be added in exact amounts to achieve desired properties.
- The process also removes non-metallic inclusions and harmful metal impurities, enhancing the metal's mechanical properties such as toughness, fatigue strength, and corrosion resistance.
-
Applications and Benefits:
- VIM is widely used in the production of superalloys, which are essential for aerospace, power generation, and other high-temperature applications.
- The process improves high-temperature creep properties and the permeability of magnetic alloys, making it indispensable for advanced material science.
- The ability to produce high-purity metals with uniform composition makes VIM a preferred method for critical applications where material performance is paramount.
-
Electromagnetic Stirring:
- The induced currents not only heat the metal but also create electromagnetic stirring. This stirring action ensures a uniform composition throughout the melt, reducing segregation and improving the homogeneity of the final product.
By combining the principles of electromagnetic induction with a controlled vacuum environment, vacuum induction melting offers a powerful method for producing high-quality metals with precise compositions and enhanced properties. This makes it a cornerstone technology in advanced metallurgy and materials engineering.
Summary Table:
Key Aspect | Description |
---|---|
Principle of Induction | Electromagnetic induction generates heat via eddy currents in the metal charge. |
Vacuum Environment | Removes gas impurities (oxygen, nitrogen, hydrogen) and volatile elements. |
Furnace Design | Airtight, refractory-lined chamber for high-temperature melting. |
Refining & Composition | Precise control of active elements; removes harmful impurities. |
Applications | Superalloys, magnetic materials, aerospace, and power generation. |
Electromagnetic Stirring | Ensures uniform composition and reduces segregation. |
Interested in high-purity metals for your industry? Contact our experts today to learn more about VIM solutions!