The melting point of a substance is significantly influenced by the heating rate, as it affects the thermal equilibrium and the accuracy of the measurement. A slower heating rate allows the sample to reach thermal equilibrium, resulting in a more accurate and consistent melting point determination. Conversely, a faster heating rate can lead to an apparent increase in the melting point due to thermal lag, where the external temperature rises faster than the sample can equilibrate. This can cause the melting point to appear higher than it actually is. Additionally, rapid heating may introduce errors such as superheating or incomplete melting, leading to inconsistent results. Therefore, controlling the heating rate is crucial for precise melting point determination.
Key Points Explained:
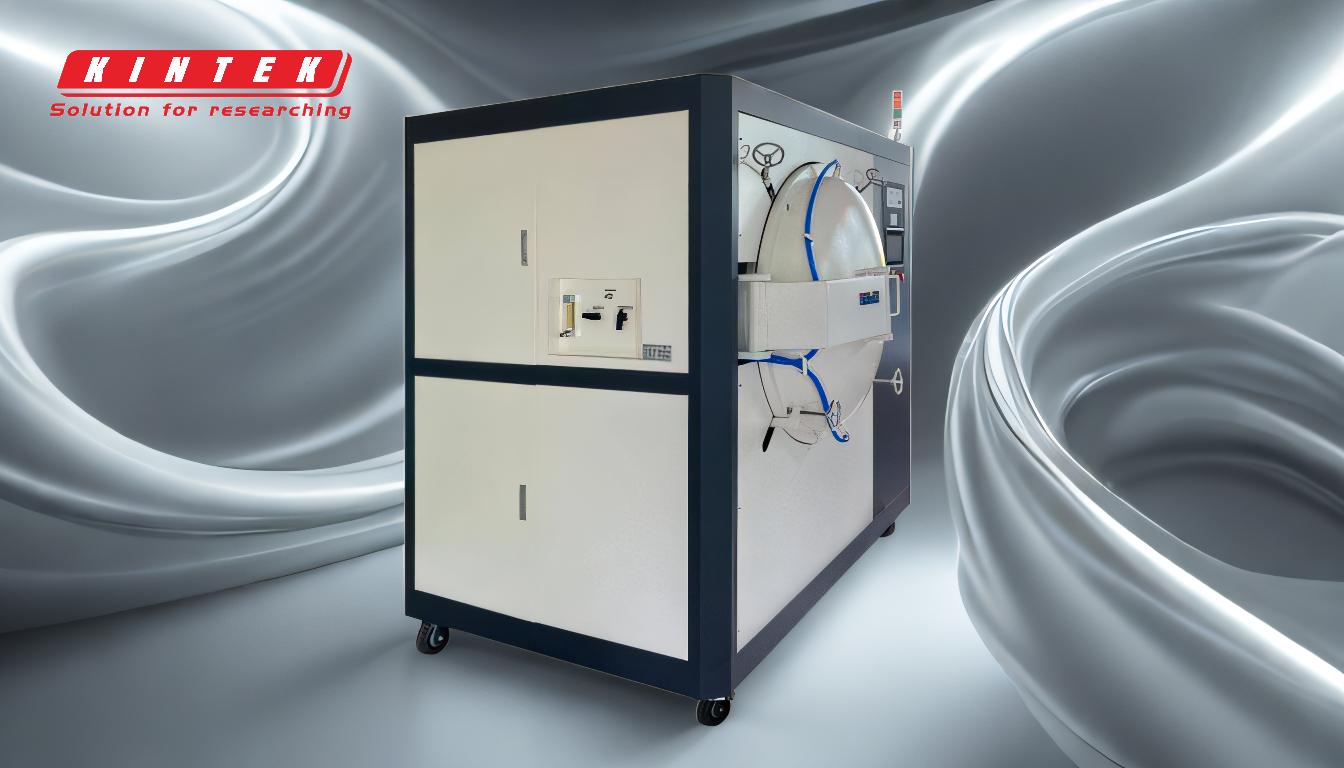
-
Thermal Equilibrium and Heating Rate:
- A slower heating rate ensures that the sample has sufficient time to reach thermal equilibrium with its surroundings. This means the temperature measured by the instrument closely matches the actual temperature of the sample, leading to a more accurate melting point determination.
- In contrast, a faster heating rate can cause the sample to lag behind the instrument's temperature reading, resulting in an apparent increase in the melting point. This thermal lag occurs because the sample cannot absorb heat quickly enough to match the external temperature rise.
-
Impact of Rapid Heating on Melting Point:
- Rapid heating can lead to superheating, where the sample's temperature exceeds its melting point before melting begins. This can cause the melting point to appear higher than it truly is.
- Incomplete melting may also occur with fast heating rates, as the sample does not have enough time to fully transition from solid to liquid. This can result in inconsistent or erroneous melting point readings.
-
Practical Considerations for Melting Point Determination:
- For accurate results, it is recommended to use a controlled and moderate heating rate, typically between 1°C to 2°C per minute. This allows the sample to melt uniformly and minimizes the risk of thermal lag or superheating.
- Instruments such as melting point apparatus or differential scanning calorimetry (DSC) are often used to precisely control the heating rate and ensure reliable measurements.
-
Importance of Heating Rate in Different Applications:
- In research and quality control, precise melting point determination is critical for identifying and characterizing materials. A consistent heating rate ensures reproducibility and reliability in these applications.
- For industrial processes, understanding the relationship between heating rate and melting point can help optimize manufacturing conditions, such as in polymer processing or pharmaceutical production.
-
Potential Errors and Mitigation Strategies:
- Errors such as thermal lag, superheating, or incomplete melting can be mitigated by using appropriate heating rates and ensuring proper calibration of the equipment.
- Regular maintenance and calibration of instruments, along with adherence to standardized protocols, can further enhance the accuracy of melting point measurements.
By carefully controlling the heating rate, users can achieve more accurate and consistent melting point determinations, which are essential for material characterization, quality control, and process optimization.
Summary Table:
Key Factor | Impact on Melting Point |
---|---|
Slow Heating Rate | Ensures thermal equilibrium, leading to accurate and consistent melting point measurements. |
Fast Heating Rate | Causes thermal lag, superheating, or incomplete melting, resulting in higher apparent MP. |
Recommended Heating Rate | 1°C to 2°C per minute for uniform melting and minimal errors. |
Common Instruments | Melting point apparatus, differential scanning calorimetry (DSC). |
Applications | Research, quality control, polymer processing, pharmaceutical production. |
Error Mitigation | Use controlled heating rates, calibrate equipment, and follow standardized protocols. |
Ensure precise melting point measurements—contact our experts today for tailored solutions!