The lining of an induction furnace is a critical process that ensures the furnace's efficiency, safety, and longevity. It involves the use of high-quality refractory materials, such as high-purity alumina fiber and vacuum-formed fiber materials, to create a lining that can withstand high temperatures, rapid heating and cooling cycles, and the corrosive nature of molten metals. The lining procedure includes several stages: material selection, preparation, and sintering. The sintering process, which forms the lining into a solid structure, is divided into three stages: baking, semi-sintering, and complete sintering. Proper maintenance and monitoring of the lining are essential to prevent degradation and ensure optimal performance over time.
Key Points Explained:
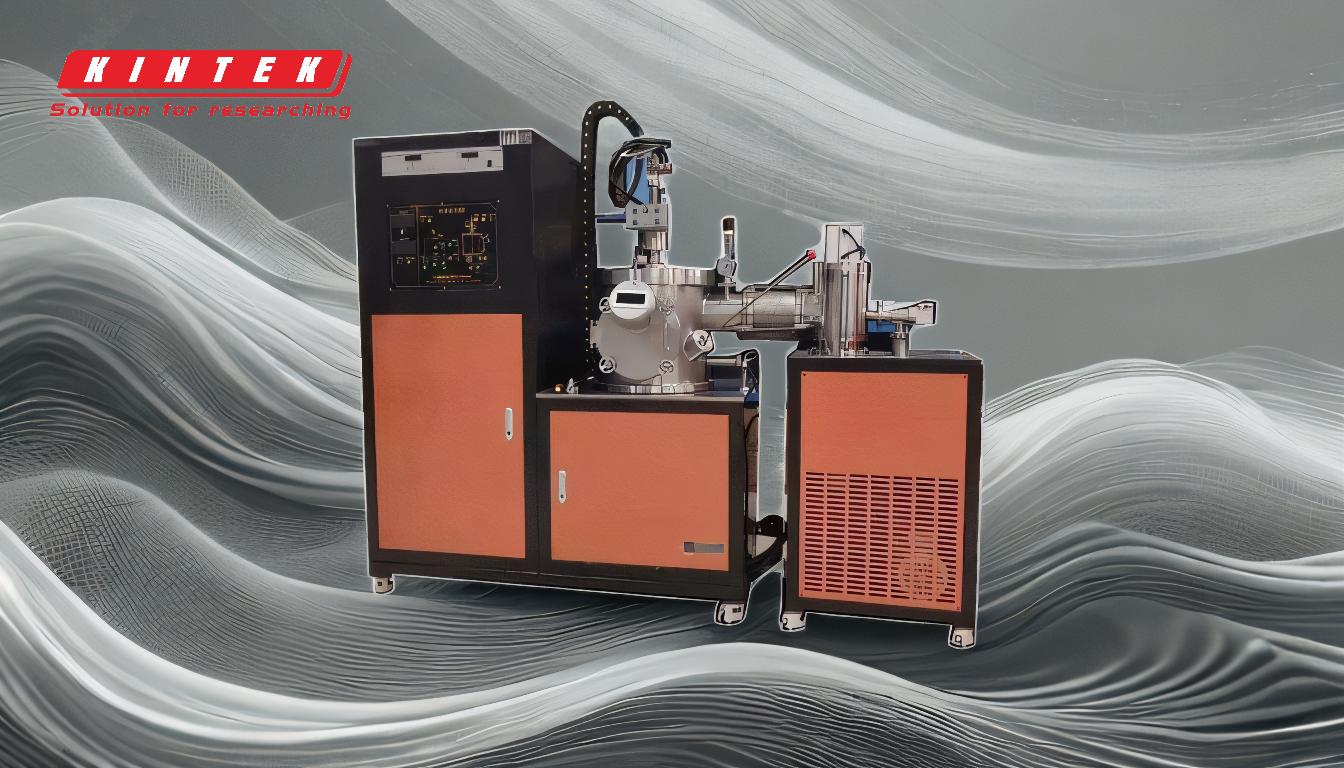
-
Purpose of the Induction Furnace Lining:
- The lining serves to contain molten metal, isolate it from the furnace's outer structure, and protect the furnace body during operation.
- It ensures safety, efficiency, and the quality of the final product by preventing leaks and maintaining thermal insulation.
-
Materials Used in Lining:
- High-purity alumina fiber, vacuum-formed fiber material, and light hollow aluminum oxide plates are commonly used.
- These materials offer high service temperatures, small heat storage capacity, rapid heat and cold resistance, and excellent thermal insulation properties.
-
Lining Procedure:
- Material Preparation: The refractory materials are prepared and shaped to fit the furnace's interior.
- Application: The materials are carefully applied to form a uniform lining layer, ensuring no gaps or weak points.
-
Sintering Process:
- Baking Stage: The lining is heated to 600°C to remove moisture, ensuring the material is dry and stable.
- Semi-Sintering Stage: The temperature is raised to 900°C and then to 1200°C to partially sinter the lining, creating a solid structure.
- Complete Sintering Stage: The final sintering temperature is reached, fully solidifying the lining and ensuring its durability and performance.
-
Importance of Proper Sintering:
- A well-executed sintering process results in a lining with a good microstructure, enhancing its resistance to thermal shock, cracking, and slag formation.
- The sintering temperature and duration significantly impact the lining's service life and overall furnace efficiency.
-
Maintenance and Monitoring:
- Regular inspection and maintenance of the lining are crucial to detect and address any signs of wear or degradation.
- The lining's operational life, or lining life, is determined by the number of heat cycles it can sustain before requiring repair or replacement.
-
Challenges and Considerations:
- Increased lining thickness can lead to higher leakage flux, reducing power, power factor, and electrical efficiency.
- Proper selection of refractory materials and adherence to the sintering process are essential to mitigate these challenges and ensure the lining's longevity.
By following these steps and considerations, the induction furnace lining can be effectively installed and maintained, ensuring optimal performance and safety in metal melting operations.
Summary Table:
Key Aspect | Details |
---|---|
Purpose | Contains molten metal, isolates furnace structure, ensures safety & quality |
Materials | High-purity alumina fiber, vacuum-formed fiber, light hollow aluminum oxide |
Lining Procedure | Material preparation, application, and sintering |
Sintering Stages | Baking (600°C), semi-sintering (900°C–1200°C), complete sintering |
Maintenance | Regular inspection to detect wear, ensure optimal performance |
Challenges | Increased lining thickness reduces power and electrical efficiency |
Optimize your induction furnace lining for peak performance—contact our experts today!