The rate of a vacuum leak is typically measured using specialized techniques and equipment designed to detect and quantify the flow of gas into or out of a vacuum system. This is crucial for maintaining the integrity of vacuum systems, which are widely used in industries such as semiconductor manufacturing, aerospace, and scientific research. The most common methods include pressure rise testing, helium leak detection, and mass spectrometry. These methods rely on principles such as pressure change over time, tracer gas detection, and mass flow analysis. The choice of method depends on factors like the required sensitivity, system size, and the type of gas being detected. Proper measurement of vacuum leak rates ensures system efficiency, safety, and performance.
Key Points Explained:
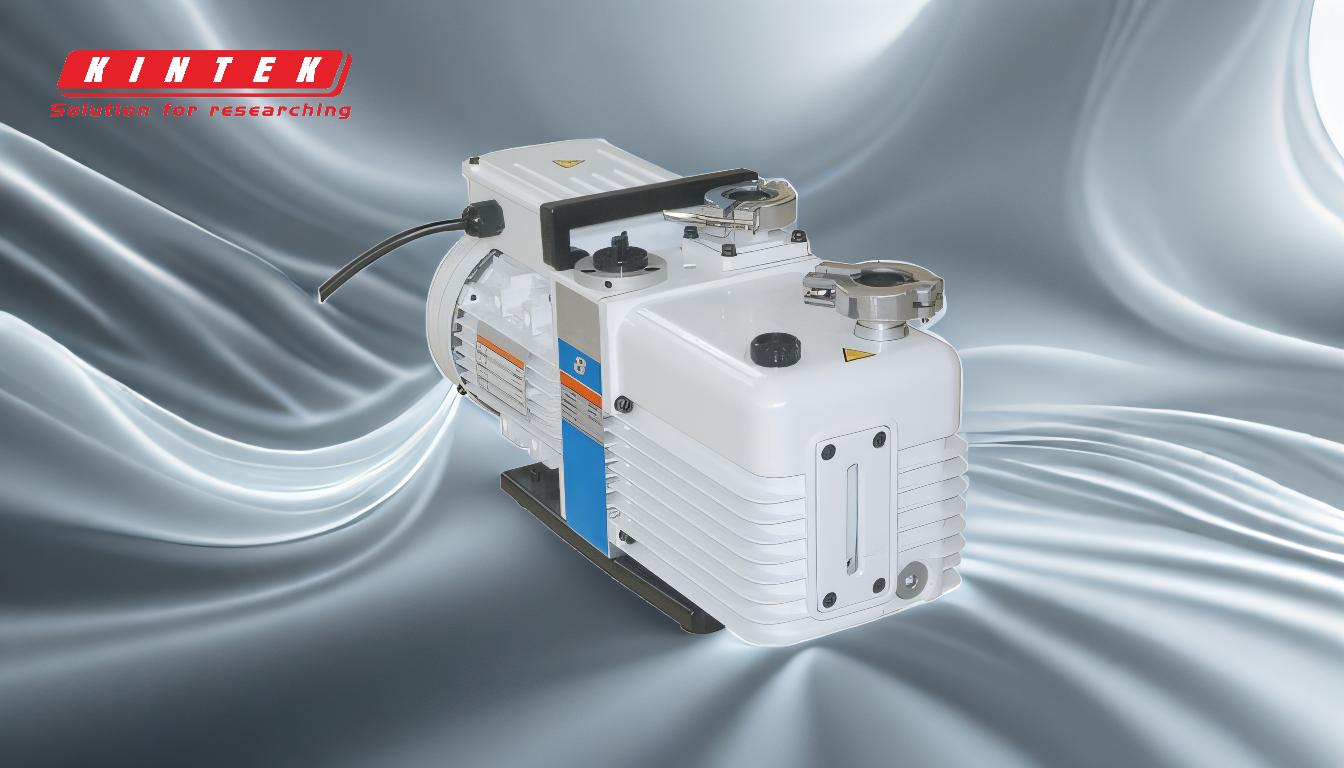
-
Pressure Rise Testing:
- Principle: This method involves isolating the vacuum system and monitoring the pressure increase over time. A leak will cause the pressure to rise as external gas enters the system.
-
Procedure:
- Seal the system and evacuate it to a stable vacuum level.
- Close the vacuum pump valve to isolate the system.
- Measure the pressure increase over a set period using a vacuum gauge.
- Calculate the leak rate based on the pressure rise and system volume.
- Applications: Ideal for large systems where high sensitivity is not required. Commonly used in industrial and laboratory settings.
-
Helium Leak Detection:
- Principle: Helium is used as a tracer gas because it is inert, non-toxic, and easily detectable at low concentrations. A helium leak detector (mass spectrometer) is used to identify and quantify leaks.
-
Procedure:
- Fill the system or suspected leak area with helium.
- Use a helium leak detector to scan the system for traces of helium escaping.
- The detector measures the helium concentration and calculates the leak rate.
- Applications: Highly sensitive and used in industries like semiconductor manufacturing, aerospace, and cryogenics where even tiny leaks can be critical.
-
Mass Spectrometry:
- Principle: Mass spectrometers can detect and quantify specific gases based on their mass-to-charge ratio. This method is highly accurate and can identify the type of gas leaking.
-
Procedure:
- Connect the mass spectrometer to the vacuum system.
- Analyze the gas composition to detect any unexpected gases.
- Quantify the leak rate based on the detected gas concentration.
- Applications: Used in research and high-precision industries where identifying the exact gas and leak rate is essential.
-
Factors Influencing Leak Rate Measurement:
- System Volume: Larger systems may require longer measurement times for accurate results.
- Leak Size: Smaller leaks may require more sensitive detection methods like helium leak detection.
- Gas Type: The type of gas leaking can affect the choice of detection method and equipment.
- Environmental Conditions: Temperature and pressure variations can influence leak rate measurements.
-
Importance of Accurate Leak Rate Measurement:
- System Performance: Leaks can compromise the efficiency and functionality of vacuum systems.
- Safety: In industries like aerospace and cryogenics, leaks can pose significant safety risks.
- Cost Efficiency: Early detection and repair of leaks can prevent costly downtime and equipment damage.
By understanding these methods and factors, equipment and consumable purchasers can select the appropriate tools and techniques for measuring vacuum leak rates, ensuring optimal system performance and reliability.
Summary Table:
Method | Principle | Applications |
---|---|---|
Pressure Rise Testing | Monitors pressure increase over time to detect leaks. | Ideal for large systems; used in industrial and lab settings. |
Helium Leak Detection | Uses helium as a tracer gas and a mass spectrometer to detect leaks. | Highly sensitive; used in semiconductor, aerospace, and cryogenic industries. |
Mass Spectrometry | Detects and quantifies specific gases based on mass-to-charge ratio. | Used in research and high-precision industries for accurate leak identification. |
Ensure your vacuum system's performance and safety—contact our experts today for tailored solutions!