Deposition rate in welding is influenced by several factors, including the type of welding process, equipment settings, material properties, and operational parameters. For instance, in laser cladding, deposition rates depend on laser power, feed rates, and traverse speed. In sputtering, factors like target material properties, current, and beam energy play a role. For wire electrode welding, variables such as wire size, amperage, and welding position significantly impact the deposition rate. Understanding these factors helps optimize welding processes for efficiency and quality.
Key Points Explained:
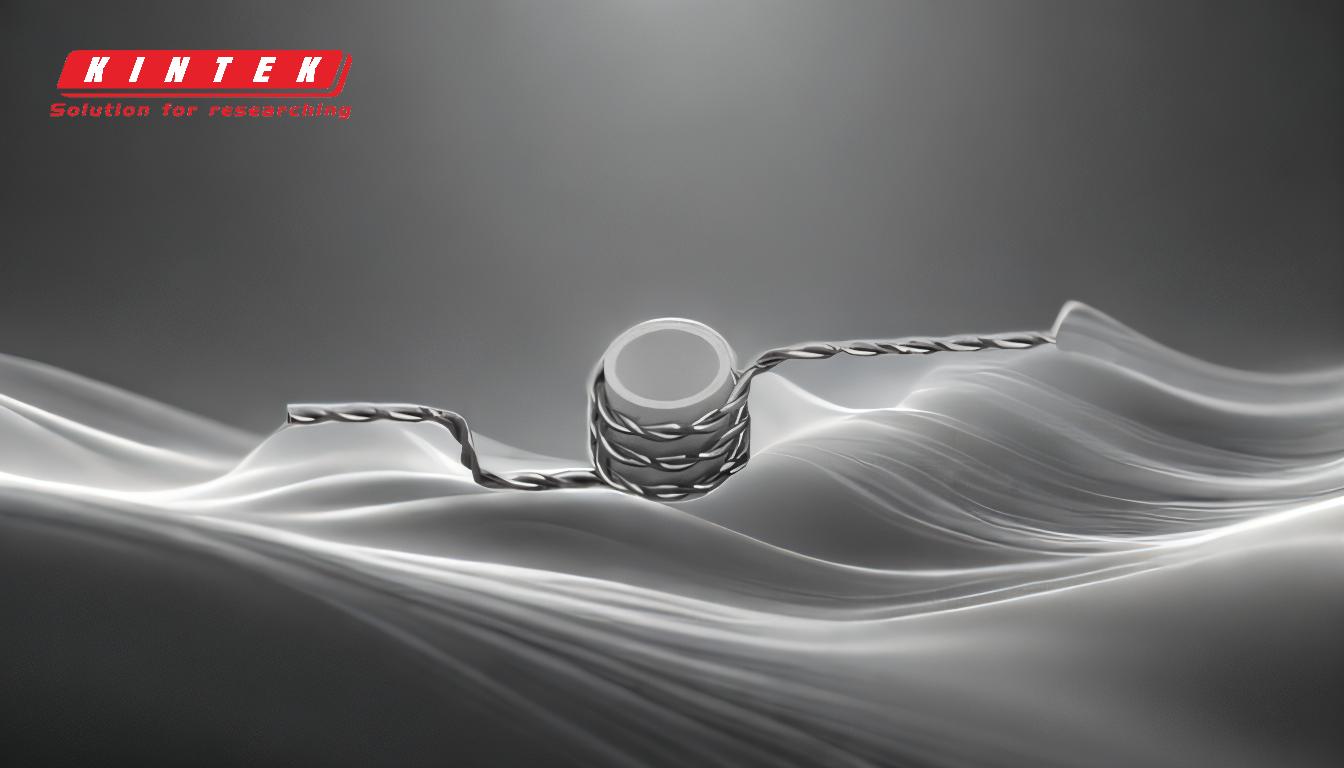
-
Laser Power in Laser Cladding:
- Laser power directly affects the energy input into the material, influencing the melting rate and deposition efficiency.
- Higher laser power generally increases the deposition rate but must be balanced to avoid defects like overheating or warping.
-
Feed Rates in Laser Cladding:
- The rate at which material (e.g., powder or wire) is fed into the welding zone impacts the deposition rate.
- Optimal feed rates ensure consistent material addition without underfeeding or overfeeding, which can lead to defects.
-
Traverse Speed in Laser Cladding:
- Traverse speed determines how quickly the laser moves across the workpiece.
- Faster traverse speeds can reduce deposition rates but improve productivity, while slower speeds increase deposition rates but may lead to excessive heat input.
-
Plasma Characteristics in Plasma Deposition:
- Plasma temperature, composition, and density influence the deposition rate and quality.
- Monitoring these parameters ensures the desired material properties and minimizes contamination.
-
Target Material Properties in Sputtering:
- The physical properties of the target material, such as density and melting point, affect how easily it can be sputtered and deposited.
- Materials with lower melting points and higher sputtering yields generally have higher deposition rates.
-
Current and Beam Energy in Sputtering:
- Higher current and beam energy increase the sputtering rate, leading to higher deposition rates.
- However, excessive energy can damage the target or substrate, so optimization is crucial.
-
Wire Electrode Size in Welding:
- Larger wire electrodes can deposit more material per unit time, increasing the deposition rate.
- For example, a 1.4mm wire electrode at 250 amps has a deposition rate of 3.5 kg/hour in flat or horizontal positions.
-
Amperage in Welding:
- Higher amperage increases the heat input and melting rate, leading to higher deposition rates.
- Proper amperage selection ensures efficient deposition without compromising weld quality.
-
Welding Position:
- The position (e.g., flat, horizontal, vertical, overhead) affects gravity's influence on the molten pool, impacting deposition rates.
- Flat and horizontal positions typically allow for higher deposition rates compared to vertical or overhead positions.
-
Material Composition and Contamination:
- Ensuring the correct elemental composition in the welding process is critical for achieving the desired material properties.
- Contamination can reduce deposition rates and compromise weld integrity, making monitoring essential.
By understanding and optimizing these factors, welders and engineers can achieve higher deposition rates while maintaining weld quality and efficiency.
Summary Table:
Factor | Impact on Deposition Rate |
---|---|
Laser Power (Laser Cladding) | Higher power increases deposition rate but risks overheating or warping. |
Feed Rates (Laser Cladding) | Optimal rates ensure consistent material addition without defects. |
Traverse Speed (Laser Cladding) | Faster speeds reduce deposition rates but improve productivity. |
Plasma Characteristics | Temperature, composition, and density influence deposition quality. |
Target Material Properties | Lower melting points and higher sputtering yields increase deposition rates. |
Current & Beam Energy | Higher energy increases sputtering rates but must be optimized to avoid damage. |
Wire Electrode Size | Larger wires deposit more material per unit time, increasing deposition rates. |
Amperage | Higher amperage increases heat input and melting rate, boosting deposition rates. |
Welding Position | Flat and horizontal positions allow higher deposition rates than vertical or overhead. |
Material Composition | Correct composition ensures desired properties; contamination reduces deposition rates. |
Ready to optimize your welding process? Contact our experts today for tailored solutions!