Coreless furnaces, particularly coreless induction furnaces, offer several advantages that make them highly suitable for various industrial applications, especially in melting and holding ferrous and non-ferrous metals. These advantages include greater alloy flexibility, lower capital and installation costs, longer refractory life, and the ability to use inert gas cover and dross removal. They are ideal for industries requiring quick alloy changes and precise temperature control, such as aerospace and commercial slab and billet casting. Additionally, coreless furnaces can be shut down and started cold, simplifying alloy changes and operations. However, they have lower power efficiency compared to core-type furnaces, and frequent alloy changes may reduce the refractory lining's operating life.
Key Points Explained:
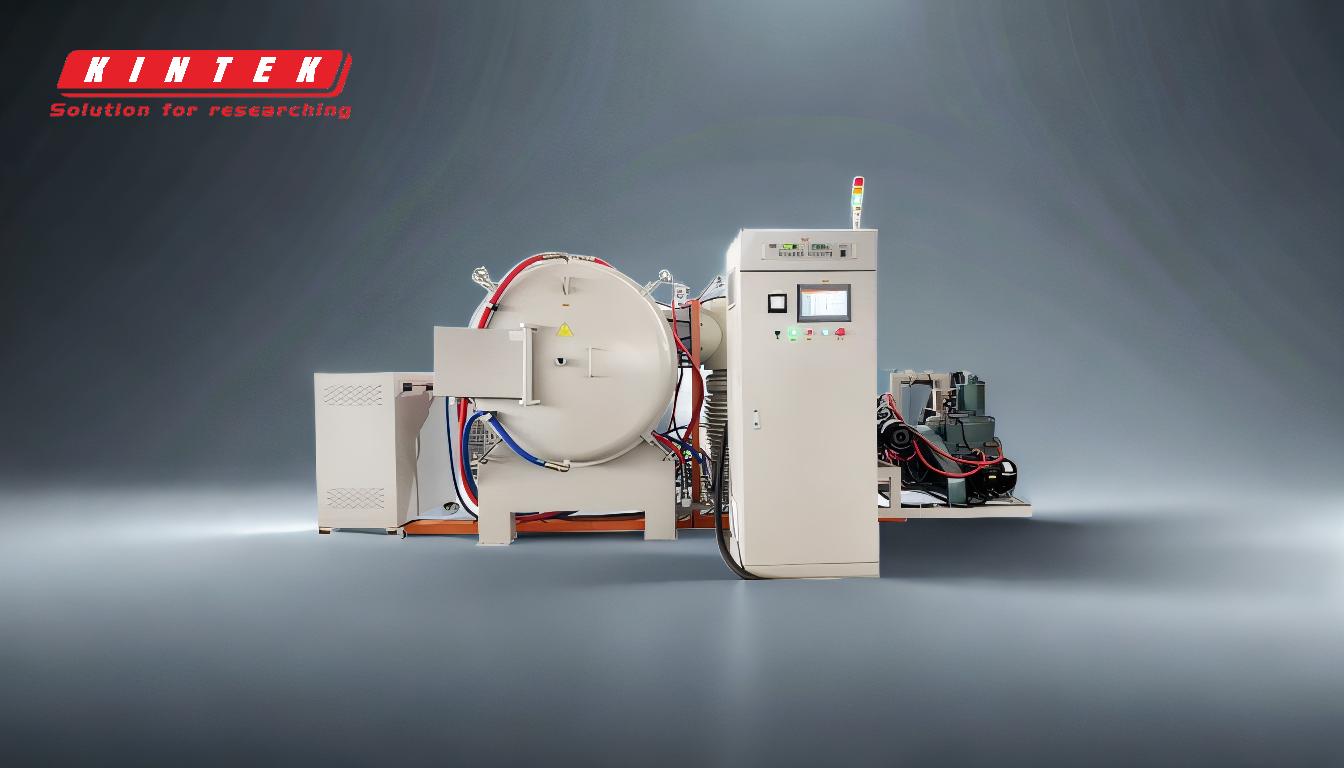
-
Alloy Flexibility:
- Coreless furnaces provide maximum alloy flexibility, allowing for quick and easy alloy changes. This is particularly beneficial in industries like aerospace and commercial casting, where different alloys are frequently required.
- The ability to shut down and start the furnace cold simplifies the process of changing alloys, making it more efficient and less time-consuming.
-
Lower Capital and Installation Costs:
- Coreless furnaces have significantly lower capital and installation costs compared to other types of furnaces. This makes them an attractive option for businesses looking to minimize upfront investments while still achieving high-quality melting and holding processes.
-
Longer Refractory Life:
- The design of coreless furnaces contributes to longer refractory life. This reduces the frequency of maintenance and replacement, leading to lower operational costs and increased uptime.
-
Use of Inert Gas Cover and Dross Removal:
- Coreless induction furnaces can utilize inert gas covers and dross removal systems. These features help in maintaining the purity of the molten metal, reducing oxidation, and improving the overall quality of the final product.
-
Ideal for Specific Applications:
- Coreless furnaces are particularly well-suited for applications requiring precise temperature control and uniform heating, such as in the production of aerospace components and commercial slabs and billets. Their ability to maintain consistent thermal conditions ensures high-quality output.
-
Operational Flexibility:
- The ability to operate across a range of frequencies (50 Hz to 10 kHz) provides operational flexibility, allowing the furnace to be tailored to specific melting and holding requirements. This adaptability is crucial for industries with varying production needs.
-
Energy Efficiency Considerations:
- While coreless furnaces offer many advantages, it's important to note that they have lower power efficiency (approximately 75%) compared to core-type furnaces. This means they may consume more energy for the same amount of work, which could be a consideration for energy-conscious operations.
-
Refractory Lining Life:
- Frequent alloy changes in coreless furnaces may reduce the operating life of the refractory lining. This is an important factor to consider for operations that require frequent alloy switches, as it may lead to increased maintenance and replacement costs.
In summary, coreless furnaces provide a range of advantages that make them highly effective for specific industrial applications. Their flexibility, cost-effectiveness, and ability to maintain high-quality standards are key benefits. However, considerations around energy efficiency and refractory lining life are important to ensure optimal performance and cost management.
Summary Table:
Advantage | Description |
---|---|
Alloy Flexibility | Quick and easy alloy changes, ideal for aerospace and commercial casting. |
Lower Costs | Reduced capital and installation expenses compared to other furnace types. |
Longer Refractory Life | Durable design minimizes maintenance and replacement needs. |
Inert Gas & Dross Removal | Maintains metal purity and reduces oxidation for higher-quality output. |
Precise Temperature Control | Ensures uniform heating, perfect for aerospace and slab/billet production. |
Operational Flexibility | Operates across 50 Hz to 10 kHz frequencies for tailored melting requirements. |
Energy Efficiency | Lower power efficiency (~75%) compared to core-type furnaces. |
Refractory Lining Life | Frequent alloy changes may reduce lining lifespan, increasing maintenance costs. |
Ready to enhance your metal melting process? Contact our experts today to find the perfect coreless furnace for your needs!