Heat treating is a critical process in metallurgy and materials science, used to alter the physical and sometimes chemical properties of metals and plastics. It involves heating the material to a specific temperature, holding it at that temperature for a set duration, and then cooling it in a controlled manner. This process can enhance properties such as hardness, strength, wear resistance, and ductility, depending on the desired outcome. The effectiveness of heat treating depends on three key variables: temperature, time at temperature, and cooling rate. Common techniques include annealing, case hardening, tempering, and quenching, each tailored to achieve specific material characteristics.
Key Points Explained:
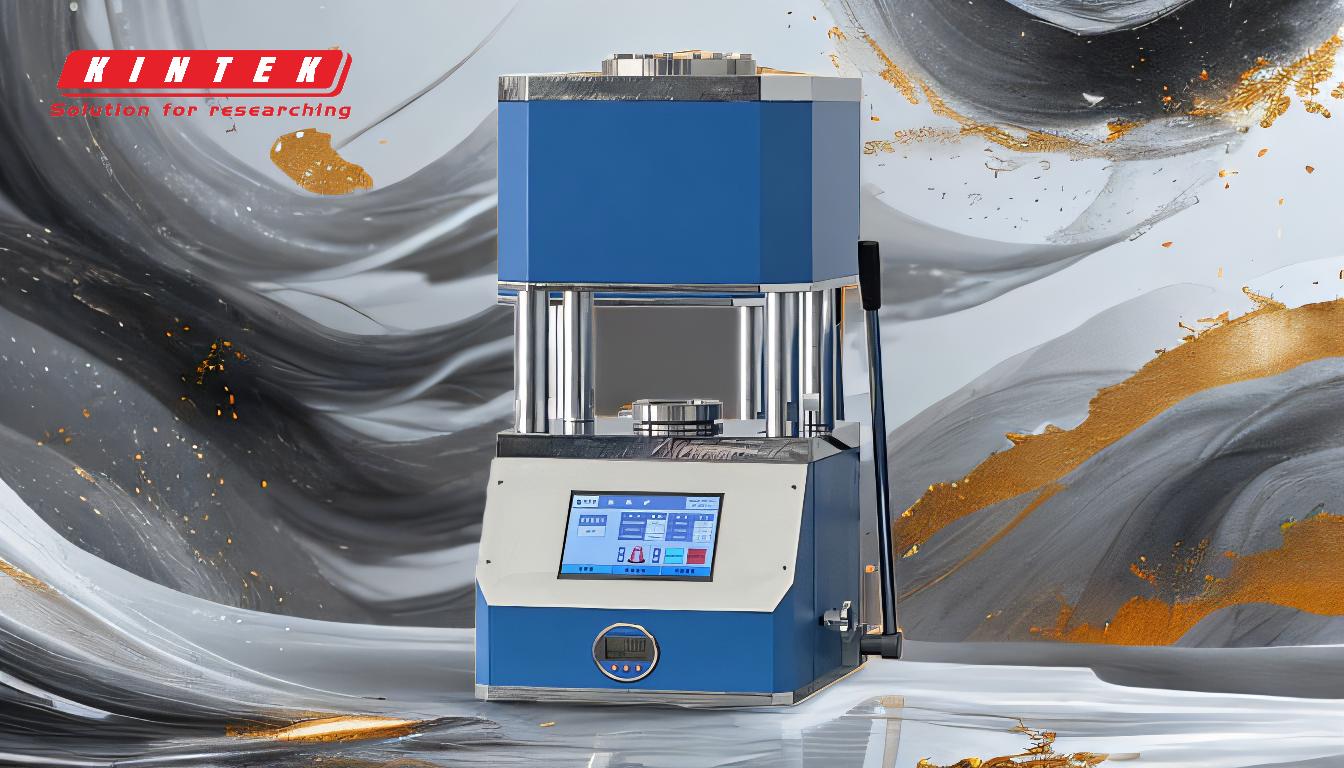
-
Purpose of Heat Treating:
- Heat treating is used to improve the mechanical properties of metals and plastics, such as hardness, strength, and wear resistance. It can also be used to relieve internal stresses, increase toughness, and enhance other material properties.
-
Basic Steps in Heat Treating:
- Heating: The material is heated to a specific temperature, which can range up to 2,400°F depending on the material and the desired outcome.
- Holding: The material is held at the target temperature for a specified period, which can vary from a few seconds to several hours.
- Cooling: The material is cooled according to a prescribed method, which can involve rapid cooling (quenching) or slow cooling (annealing), depending on the desired properties.
-
Key Variables in Heat Treating:
- Temperature: The temperature to which the material is heated is crucial, as it determines the extent of the structural changes in the material.
- Time at Temperature: The duration the material is held at the target temperature affects the uniformity and depth of the treatment.
- Cooling Rate: The method and rate of cooling are critical in determining the final properties of the material. Rapid cooling can increase hardness, while slow cooling can increase ductility.
-
Common Heat Treatment Techniques:
- Annealing: This process involves heating the material to a specific temperature and then allowing it to cool slowly. It is used to soften metals, improve machinability, and relieve internal stresses.
- Case Hardening: This technique hardens the surface of the metal while keeping the core relatively soft. It is often used for parts that require a hard, wear-resistant surface and a tough, ductile interior.
- Tempering: After hardening, tempering is used to reduce brittleness and increase toughness. The material is reheated to a lower temperature and then cooled.
- Quenching: This involves rapidly cooling the material from a high temperature, usually by immersing it in water, oil, or air. Quenching increases hardness and strength but can also make the material more brittle.
- Precipitation Strengthening: This process involves heating the material to dissolve alloying elements and then cooling it to form fine particles that strengthen the material.
-
Applications of Heat Treating:
- Softening or Hardening: Heat treating can be used to either soften or harden a material, depending on the application. For example, annealing softens metal, while through hardening increases its hardness.
- Stress Relief: Heat treating can remove internal stresses caused by machining, forming, or other processes, which helps prevent distortion or cracking.
- Resilience and Spring Properties: Techniques like austempering and marquenching are used to add resilience or spring properties to metals, making them suitable for applications like springs and gears.
- Magnetic Permeability: Certain heat treatments can alter the magnetic properties of materials, making them suitable for use in magnetic applications.
-
Material-Specific Considerations:
- The type of material being treated (e.g., steel, aluminum, plastic) will dictate the specific heat treating process and parameters. For example, steel can be hardened through quenching, while aluminum may require precipitation hardening.
In summary, heat treating is a versatile and essential process in manufacturing and materials science. By carefully controlling the temperature, time, and cooling rate, manufacturers can tailor the properties of metals and plastics to meet specific application requirements. Whether the goal is to increase hardness, relieve stress, or improve toughness, heat treating offers a range of techniques to achieve the desired outcome.
Summary Table:
Key Aspect | Details |
---|---|
Purpose | Improves mechanical properties like hardness, strength, and wear resistance. |
Key Steps | Heating, holding at temperature, and controlled cooling. |
Key Variables | Temperature, time at temperature, and cooling rate. |
Common Techniques | Annealing, case hardening, tempering, quenching, and precipitation hardening. |
Applications | Softening/hardening, stress relief, resilience, and magnetic permeability. |
Material Considerations | Varies by material (e.g., steel, aluminum, plastic). |
Ready to enhance your materials with heat treating? Contact our experts today for tailored solutions!