The question revolves around understanding the different melting methods, but the provided reference discusses Cold Isostatic Pressing (CIP) and Hot Isostatic Pressing (HIP), which are not directly related to melting techniques. However, based on general knowledge, melting methods are diverse and depend on the material being processed, the desired outcome, and the equipment used. Common melting methods include induction melting, arc melting, vacuum melting, and resistance melting, among others. Each method has specific applications, advantages, and limitations, making them suitable for different industrial and laboratory settings.
Key Points Explained:
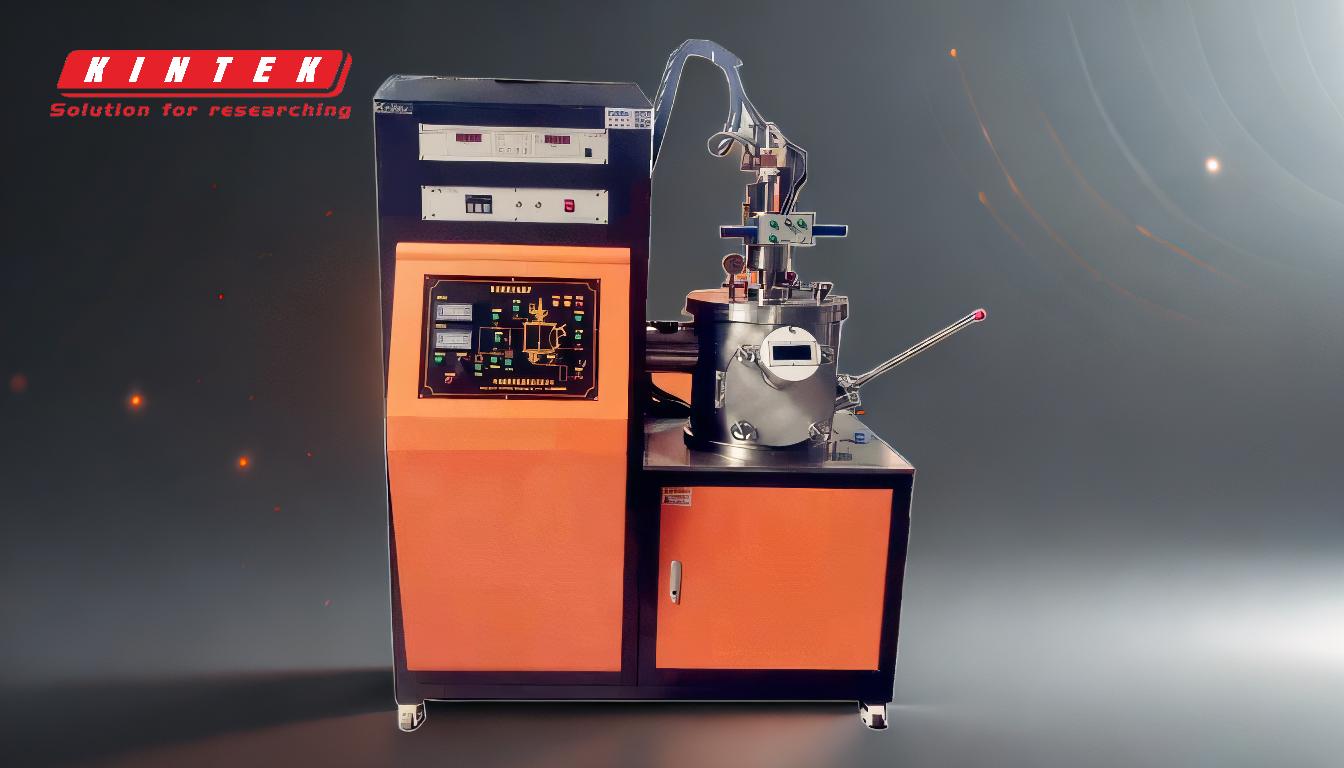
-
Induction Melting
- How it works: Induction melting uses electromagnetic induction to generate heat within the material. An alternating current passes through a coil, creating a magnetic field that induces eddy currents in the conductive material, causing it to melt.
- Applications: Commonly used for melting metals like steel, copper, aluminum, and precious metals.
- Advantages: High energy efficiency, precise temperature control, and minimal contamination.
- Limitations: Requires conductive materials and can be expensive due to equipment costs.
-
Arc Melting
- How it works: Arc melting uses an electric arc to generate intense heat. The arc is created between an electrode and the material, melting it through high-temperature exposure.
- Applications: Used for melting refractory metals like titanium, tungsten, and zirconium.
- Advantages: Capable of melting high-melting-point materials and producing high-purity alloys.
- Limitations: Requires inert gas environments to prevent oxidation, and electrode consumption can be an issue.
-
Vacuum Melting
- How it works: Vacuum melting occurs in a vacuum or controlled atmosphere to prevent oxidation and contamination. The material is heated using induction or resistance heating.
- Applications: Ideal for producing high-purity metals and alloys, such as those used in aerospace and medical industries.
- Advantages: Reduces impurities and gas entrapment, resulting in superior material quality.
- Limitations: High equipment and operational costs, and slower processing times.
-
Resistance Melting
- How it works: Resistance melting uses electrical resistance to generate heat. The material is placed in a crucible, and an electric current passes through it, causing it to melt due to resistance heating.
- Applications: Suitable for melting low-melting-point metals like zinc, lead, and tin.
- Advantages: Simple and cost-effective for small-scale operations.
- Limitations: Limited to materials with lower melting points and less precise temperature control.
-
Other Melting Methods
- Electron Beam Melting (EBM): Uses a high-energy electron beam to melt materials in a vacuum. Ideal for high-purity applications and refractory metals.
- Laser Melting: Employs a focused laser beam to melt materials, often used in additive manufacturing (3D printing).
- Plasma Arc Melting: Utilizes a plasma torch to achieve extremely high temperatures, suitable for melting ceramics and high-performance alloys.
Each melting method has unique characteristics that make it suitable for specific materials and applications. The choice of method depends on factors such as material properties, desired purity, production scale, and cost considerations.
Summary Table:
Melting Method | How It Works | Applications | Advantages | Limitations |
---|---|---|---|---|
Induction Melting | Uses electromagnetic induction to generate heat within conductive materials. | Metals like steel, copper, aluminum. | High energy efficiency, precise control, minimal contamination. | Requires conductive materials; high equipment costs. |
Arc Melting | Uses an electric arc to generate intense heat between an electrode and material. | Refractory metals like titanium, tungsten. | Melts high-melting-point materials; produces high-purity alloys. | Requires inert gas; electrode consumption. |
Vacuum Melting | Melts materials in a vacuum or controlled atmosphere to prevent contamination. | High-purity metals for aerospace and medical. | Reduces impurities; superior material quality. | High costs; slower processing. |
Resistance Melting | Uses electrical resistance to generate heat in a crucible. | Low-melting-point metals like zinc, lead. | Simple and cost-effective for small-scale operations. | Limited to low-melting-point materials; less precise control. |
Other Methods | Includes EBM, laser melting, and plasma arc melting for specialized applications. | High-purity and refractory materials. | High precision and purity; suitable for advanced manufacturing. | High costs; complex setups. |
Need help choosing the right melting method for your application? Contact our experts today for personalized advice!