The quality of pellets is heavily influenced by the characteristics of the raw materials used in their production. Key factors such as the shape, size, and moisture content of the raw materials play a critical role in determining the overall quality of the pellets. These factors not only affect the physical properties of the pellets but also influence the efficiency and effectiveness of the pelletizing process. Understanding and optimizing these variables can lead to higher-quality pellets and a more efficient production process.
Key Points Explained:
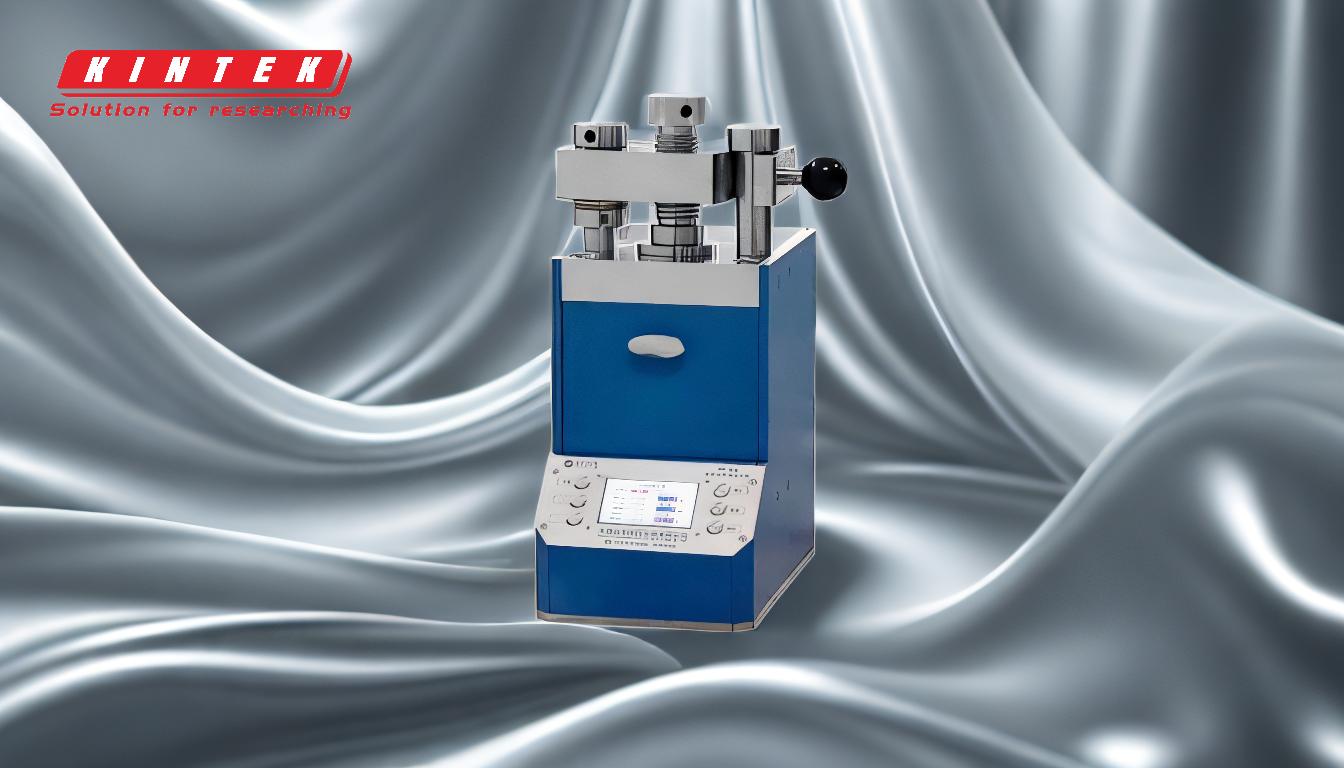
-
Shape of Raw Materials:
- The shape of the raw materials can significantly impact how well they compress and bind together during the pelletizing process. Irregularly shaped materials may not compact as efficiently, leading to weaker pellets that are more prone to breaking.
- Uniformly shaped materials, on the other hand, tend to produce more consistent and durable pellets. This is because they can be more evenly distributed and compressed within the pellet mill.
-
Size of Raw Materials:
- The size of the raw materials is another crucial factor. Materials that are too large may not compress properly, resulting in pellets with poor structural integrity.
- Conversely, materials that are too small may not provide enough surface area for binding agents to work effectively, also leading to weaker pellets.
- Optimal size distribution is key to achieving a balance where the materials can be compressed effectively while still maintaining the necessary structural strength.
-
Moisture Content:
- Moisture content in the raw materials is a critical factor that can make or break the pelletizing process. Too much moisture can cause the materials to become too soft, making them difficult to compress and resulting in pellets that are prone to crumbling.
- On the other hand, materials that are too dry may not bind well, leading to pellets that are too brittle and easily break apart.
- The ideal moisture content varies depending on the type of material being used, but it generally needs to be carefully controlled to ensure optimal pellet quality.
-
Impact on Pelletizing Plan:
- The quality of the raw materials directly influences the pelletizing plan of the pellet mill. If the raw materials are of poor quality, the mill may need to adjust its settings or processes to compensate, which can lead to inefficiencies and higher production costs.
- High-quality raw materials, on the other hand, allow for a more streamlined and efficient pelletizing process, resulting in better-quality pellets and lower production costs.
-
Overall Pellet Quality:
- The combination of shape, size, and moisture content in the raw materials ultimately determines the overall quality of the pellets. High-quality pellets are typically more durable, have a consistent size and shape, and are less likely to break or crumble during handling and transportation.
- Ensuring that these factors are optimized can lead to a more successful pelletizing operation, with higher yields and better-quality end products.
By carefully considering and controlling these factors, producers can significantly improve the quality of their pellets, leading to better performance in their intended applications and greater overall efficiency in the pelletizing process.
Summary Table:
Factor | Impact on Pellet Quality |
---|---|
Shape | Uniform shapes compress better, creating durable pellets. Irregular shapes lead to breakage. |
Size | Optimal size ensures proper compression and structural integrity. |
Moisture Content | Balanced moisture prevents crumbling (too wet) or brittleness (too dry). |
Pelletizing Plan | High-quality raw materials streamline production, reducing costs and improving efficiency. |
Want to improve your pellet quality and production efficiency? Contact our experts today for tailored solutions!