Hot forging is a widely used manufacturing process due to its ability to produce strong, durable components with excellent mechanical properties. However, like any manufacturing method, it has its limitations. These limitations can impact the design, cost, and feasibility of using hot forging for certain applications. Below is a detailed exploration of the key limitations of hot forging.
Key Points Explained:
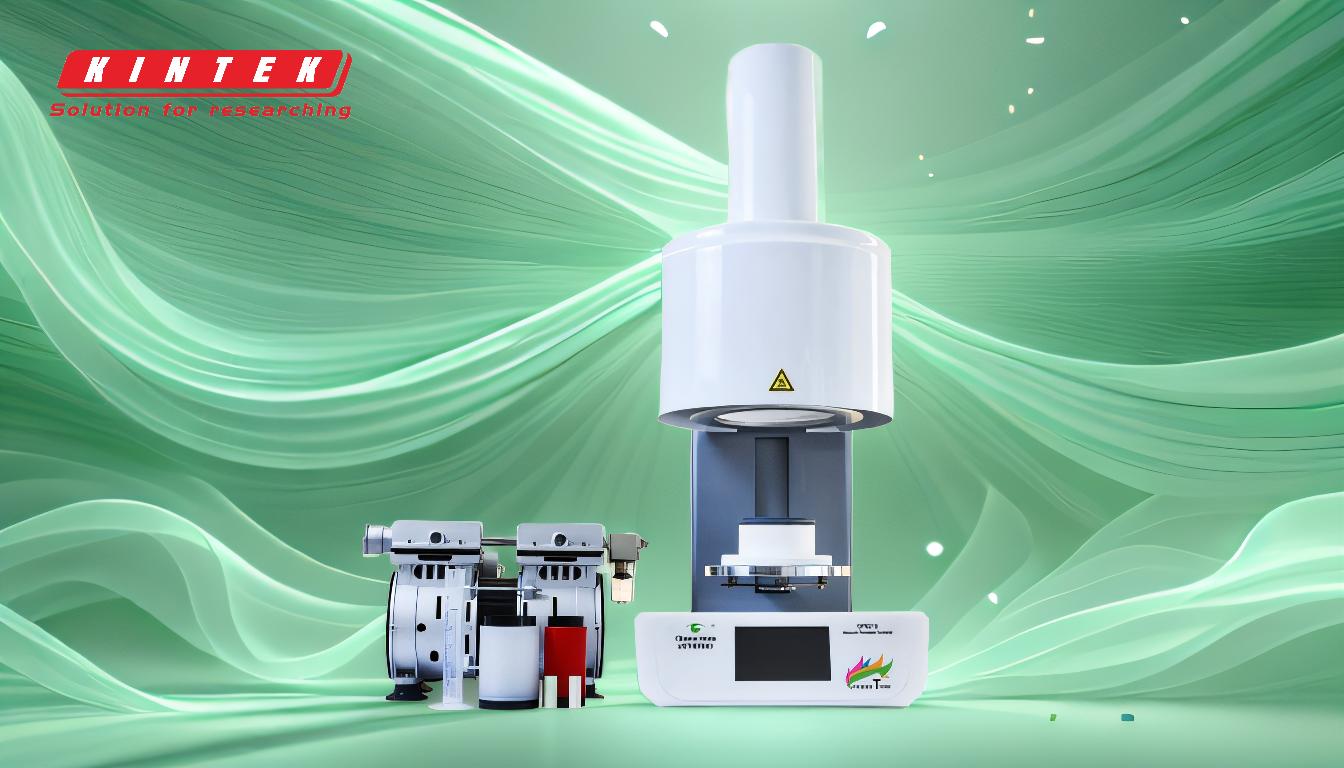
-
High Initial Equipment Costs
- Hot forging requires specialized equipment, such as forging presses, hammers, and furnaces, which can be expensive to purchase and maintain.
- The need for high-temperature furnaces and tooling adds to the overall cost, making it less economical for small-scale production or low-volume manufacturing.
- The initial investment can be a significant barrier for smaller companies or startups.
-
Material Limitations
- Hot forging is primarily suited for metals with good ductility at high temperatures, such as steel, aluminum, and copper alloys.
- Materials that are brittle or have poor high-temperature properties, such as certain titanium alloys or high-carbon steels, may not be suitable for hot forging.
- The process may also lead to grain growth in some materials, which can negatively affect mechanical properties.
-
Dimensional Tolerances and Surface Finish
- Hot forging typically results in lower dimensional accuracy compared to cold forging or machining.
- The high temperatures can cause oxidation and scaling on the surface of the workpiece, leading to a rough surface finish that may require additional post-processing.
- Achieving tight tolerances often necessitates secondary machining operations, increasing production time and cost.
-
Energy Consumption and Environmental Impact
- The process requires significant energy to heat the metal to forging temperatures, which can range from 1,000°C to 1,250°C for steel.
- High energy consumption contributes to increased operational costs and a larger carbon footprint.
- The production of heat and emissions from furnaces can also pose environmental challenges, requiring additional measures for pollution control.
-
Tool Wear and Maintenance
- The high temperatures and pressures involved in hot forging can lead to rapid wear and degradation of forging dies and tools.
- Frequent tool maintenance or replacement is often necessary, adding to operational costs and downtime.
- The design and material of the dies must be carefully selected to withstand the harsh conditions, which can further increase costs.
-
Complexity in Design and Process Control
- Hot forging requires precise control over temperature, pressure, and deformation rates to ensure consistent quality.
- Complex geometries or intricate designs may be difficult to achieve due to the limitations of die design and material flow.
- Process control becomes more challenging as the size and complexity of the workpiece increase, potentially leading to defects such as cracks, voids, or incomplete filling of the die.
-
Limited Suitability for Small or Thin Parts
- Hot forging is less suitable for producing small or thin components, as the high temperatures can lead to excessive material flow and deformation.
- Thin sections may cool too quickly, resulting in inconsistent mechanical properties or defects.
- Cold forging or other manufacturing methods may be more appropriate for such applications.
-
Post-Forging Operations
- Hot-forged parts often require additional processing, such as heat treatment, machining, or surface finishing, to meet final specifications.
- These post-forging operations add to the overall production time and cost, reducing the efficiency of the process.
- The need for secondary operations can also introduce variability in the final product quality.
In summary, while hot forging offers numerous advantages, including the ability to produce strong and durable components, it is not without its limitations. High equipment costs, material constraints, energy consumption, and the need for post-processing are some of the key challenges that must be considered when selecting hot forging as a manufacturing method. Understanding these limitations is crucial for making informed decisions and optimizing the process for specific applications.
Summary Table:
Limitation | Key Details |
---|---|
High Initial Equipment Costs | Expensive specialized equipment and high-temperature furnaces required. |
Material Limitations | Limited to ductile metals; unsuitable for brittle or high-carbon materials. |
Dimensional Tolerances | Lower accuracy; rough surface finish requiring post-processing. |
Energy Consumption | High energy usage and environmental impact due to heating requirements. |
Tool Wear and Maintenance | Rapid wear of dies and tools; frequent maintenance increases costs. |
Complexity in Design | Precise control needed; challenging for intricate designs or large workpieces. |
Limited Suitability for Small Parts | Unsuitable for thin or small components due to excessive deformation. |
Post-Forging Operations | Additional heat treatment, machining, or finishing often required. |
Want to learn more about hot forging limitations? Contact our experts today!