Brazing is a metal-joining process that involves heating two or more metal pieces to a temperature below their melting points and using a filler metal to create a strong, seamless joint. The filler metal, which has a lower melting point than the base metals, flows into the joint by capillary action, forming a durable bond upon cooling. Brazing is widely used in industries such as automotive, aerospace, and manufacturing due to its ability to join dissimilar metals, produce clean and precise joints, and maintain the integrity of the base materials. The process is influenced by various factors, including the type of materials, joint design, and specific brazing conditions, which must be optimized for each application.
Key Points Explained:
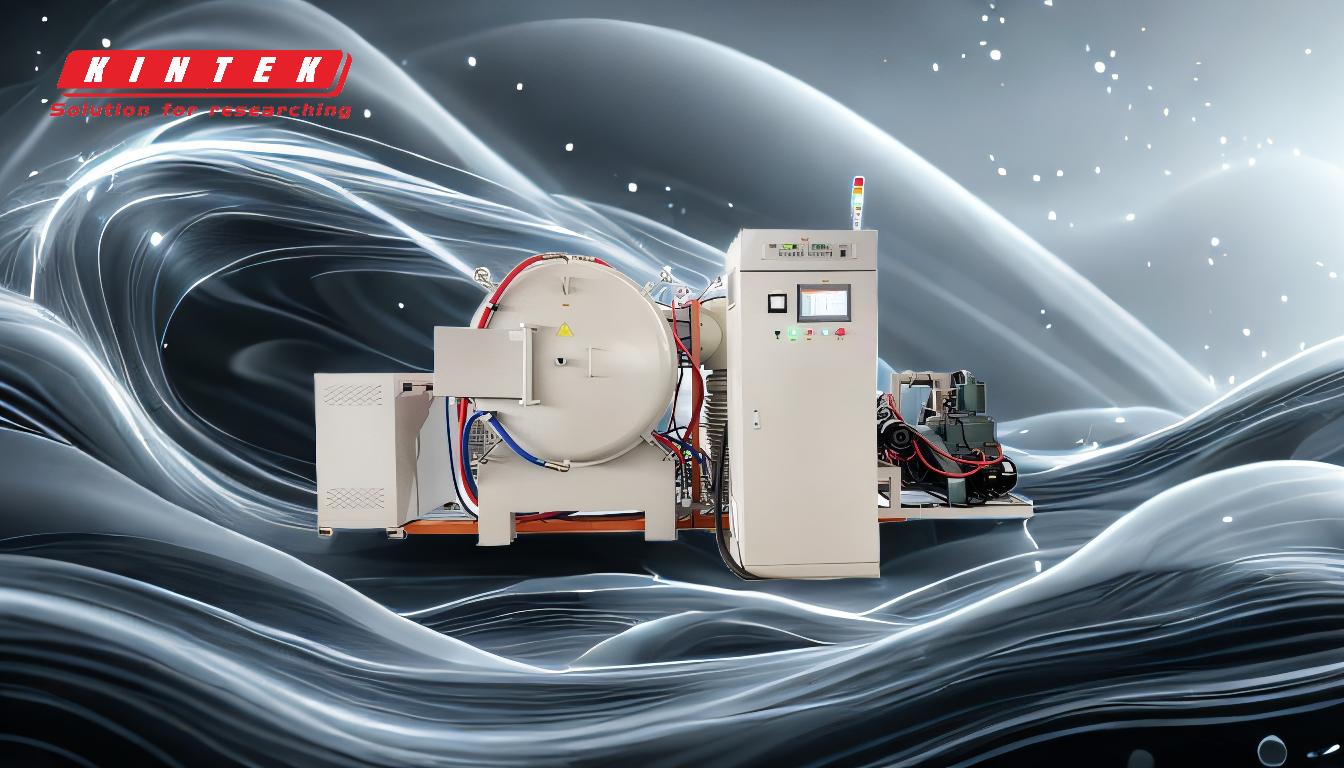
-
Definition of Brazing:
- Brazing is a process that joins metal pieces using a filler metal with a lower melting point than the base metals. The filler metal is heated until it melts and flows into the joint by capillary action, creating a strong bond upon cooling. This method is distinct from welding, as it does not melt the base metals.
-
Key Components of the Brazing Process:
- Filler Metal: Typically an alloy with a melting point lower than the base metals. Common filler metals include silver, copper, and aluminum-based alloys.
- Heat Source: Used to raise the temperature of the filler metal and base metals to the brazing temperature. Heat sources can include torches, furnaces, or induction heating.
- Flux: A chemical agent used to clean the metal surfaces and prevent oxidation during the brazing process. Flux also helps the filler metal flow smoothly into the joint.
-
Factors Influencing Brazing:
- Material Properties: The type of base metals and filler metal used significantly impact the brazing process. For example, brazing cast iron requires a filler metal that melts above 840 °F (450 °C) but does not affect the base metal.
- Joint Design: The shape and size of the parts being joined affect the effectiveness of capillary action. A tight fit-up is essential for optimal filler metal flow.
- Surface Preparation: Cleanliness is critical to ensure proper bonding. Surface oxide films must be removed, often using alkali solutions or mechanical methods.
- Process Parameters: Factors such as heating rate, holding time, cooling rate, and vacuum level (in vacuum brazing) must be carefully controlled to achieve high-quality joints.
-
Applications of Brazing:
- Brazing is used in a wide range of industries, including automotive (e.g., exhaust manifolds), aerospace (e.g., heat exchangers), and manufacturing (e.g., tubing and piping). It is particularly useful for joining dissimilar metals and producing joints that are both strong and aesthetically pleasing.
-
Advantages of Brazing:
- Versatility: Can join a wide variety of metals, including dissimilar materials.
- Precision: Produces clean, precise joints with minimal distortion.
- Strength: Creates strong, durable bonds that can withstand high stress and temperature conditions.
- Cost-Effectiveness: Often more economical than welding, especially for complex assemblies.
-
Challenges and Considerations:
- Parameter Optimization: Achieving the best results requires careful optimization of process parameters, which may involve experimental screening.
- Material Compatibility: Not all metals are suitable for brazing, and some combinations may require specialized techniques or filler metals.
- Environmental Factors: In vacuum brazing, maintaining the correct vacuum level is crucial to prevent oxidation and ensure proper joint formation.
By understanding these key points, equipment and consumable purchasers can make informed decisions about the materials and processes required for successful brazing applications.
Summary Table:
Aspect | Details |
---|---|
Definition | Joins metals using a filler metal with a lower melting point than base metals. |
Key Components | Filler metal, heat source, and flux. |
Influencing Factors | Material properties, joint design, surface preparation, process parameters. |
Applications | Automotive, aerospace, manufacturing (e.g., heat exchangers, tubing). |
Advantages | Versatility, precision, strength, cost-effectiveness. |
Challenges | Parameter optimization, material compatibility, environmental factors. |
Discover how brazing can enhance your projects—contact our experts today for tailored solutions!