PVD (Physical Vapor Deposition) coating is a process that involves vaporizing a solid material in a vacuum and depositing it onto a substrate to form a thin, durable, and functional layer. The process utilizes various gases, including inert gases like Argon and reactive gases such as oxygen, nitrogen, and methane. These gases play critical roles in creating the desired coating properties. Inert gases like Argon are used to maintain a chemically unreactive atmosphere, while reactive gases interact with metal atoms to form compounds like metal oxides, nitrides, and carbides. This results in coatings with enhanced hardness, wear resistance, and other functional properties. The PVD process is carried out in a vacuum chamber at extremely low pressures, ensuring a clean and controlled environment for high-quality coatings.
Key Points Explained:
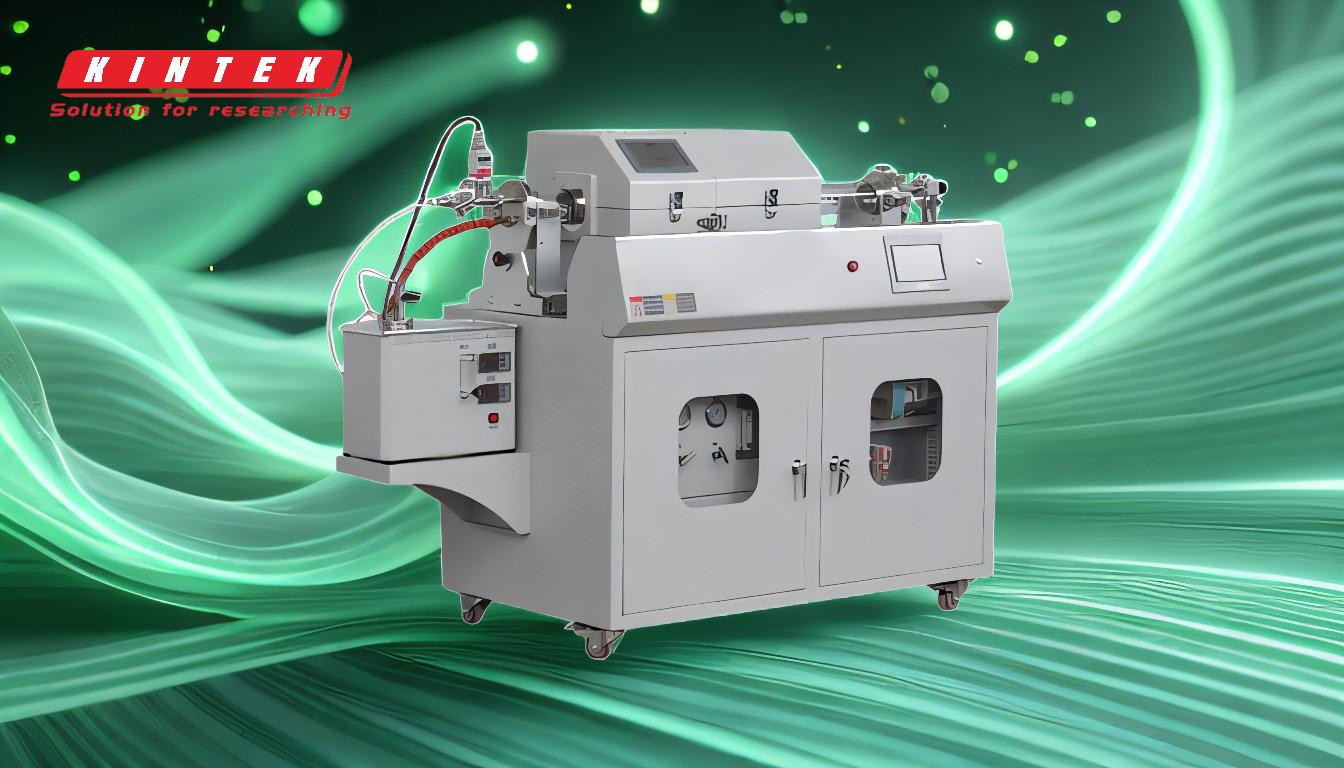
-
Inert Gases in PVD Coating:
- Argon is the most commonly used inert gas in PVD coating.
- It creates a chemically unreactive atmosphere, which is essential for maintaining the purity of the coating process.
- Argon is also used in the sputtering process, where it ionizes and bombards the target material, causing it to vaporize.
- The use of inert gases ensures that the vaporized material remains uncontaminated during the deposition process.
-
Reactive Gases in PVD Coating:
- Oxygen, Nitrogen, and Methane are the primary reactive gases used in PVD coating.
- These gases react with metal atoms during the transportation stage of the PVD process, forming compounds such as:
- Metal Oxides (e.g., titanium dioxide, aluminum oxide) when oxygen is used.
- Metal Nitrides (e.g., titanium nitride, chromium nitride) when nitrogen is used.
- Metal Carbides (e.g., titanium carbide, tungsten carbide) when methane is used.
- These compounds enhance the functional properties of the coating, such as hardness, wear resistance, and corrosion resistance.
-
Role of Gases in the PVD Process:
- Evaporation: The target material is vaporized using techniques like electron beam, ion bombardment, or cathodic arc. Inert gases like Argon are often used to assist in this step.
- Transportation: The vaporized material is transported through the vacuum chamber. Reactive gases are introduced at this stage to modify the composition of the vaporized material.
- Condensation: The vaporized material condenses on the substrate, forming a thin, adherent coating. The reactive gases ensure the formation of specific compounds (e.g., oxides, nitrides, carbides) that enhance the coating's properties.
-
Vacuum Environment:
- The PVD process occurs in a vacuum chamber at extremely low pressures (typically 10^-3 to 10^-9 Torr).
- This vacuum environment ensures that the vaporized material remains clean and free from contaminants.
- The low-pressure conditions also facilitate the efficient transportation and deposition of the vaporized material.
-
Advantages of Using Gases in PVD Coating:
- Customizable Coatings: By selecting specific reactive gases, the composition and properties of the coating can be tailored to meet specific requirements.
- Enhanced Properties: Reactive gases enable the formation of hard, wear-resistant, and corrosion-resistant coatings.
- Environmental Benefits: PVD is a more environmentally friendly coating technology compared to traditional methods, as it produces minimal waste and emissions.
-
Applications of PVD Coatings:
- Industrial Tools: PVD coatings are widely used to enhance the durability and performance of cutting tools, molds, and dies.
- Aerospace: Coatings with high wear resistance and thermal stability are applied to aircraft components.
- Medical Devices: Biocompatible coatings are used for implants and surgical instruments.
- Decorative Finishes: PVD coatings provide attractive, durable finishes for jewelry, watches, and architectural components.
-
Process Steps Involving Gases:
- Evacuation: The vacuum chamber is evacuated to create a high-vacuum environment.
- Introduction of Gases: Inert and reactive gases are introduced into the chamber as needed.
- Vaporization: The target material is vaporized using energy sources like electron beams or ion bombardment.
- Transportation and Reaction: Reactive gases interact with the vaporized material to form desired compounds.
- Deposition: The vaporized material condenses on the substrate, forming a thin, adherent coating.
- Purging: The chamber is purged with inert gas to remove residual vapors and ensure a clean environment.
By understanding the roles of gases in the PVD coating process, purchasers can make informed decisions about the types of coatings and materials that best meet their needs. The use of inert and reactive gases enables the production of high-performance coatings with tailored properties, making PVD a versatile and valuable technology across various industries.
Summary Table:
Aspect | Details |
---|---|
Inert Gases | Argon maintains a chemically unreactive atmosphere, ensuring coating purity. |
Reactive Gases | Oxygen, Nitrogen, and Methane form compounds like oxides, nitrides, and carbides. |
Key Properties | Enhanced hardness, wear resistance, and corrosion resistance. |
Process Steps | Evaporation, transportation, condensation, and purging. |
Applications | Industrial tools, aerospace, medical devices, and decorative finishes. |
Environmental Benefits | Minimal waste and emissions, making PVD eco-friendly. |
Ready to enhance your products with PVD coatings? Contact us today to learn more!