The arc melting process is an electrothermal metallurgical method that utilizes an electric arc to generate extremely high temperatures, melting metals without altering their chemical properties. It involves creating an electric arc between an electrode and the material to be melted, or between two electrodes, using an arc melting furnace. The furnace converts high voltage into low voltage and high current, enabling the arc to sustain itself and melt the metal. This process is widely used in industries for melting scrap steel and other metals, and it is particularly effective in vacuum environments for producing high-purity materials.
Key Points Explained:
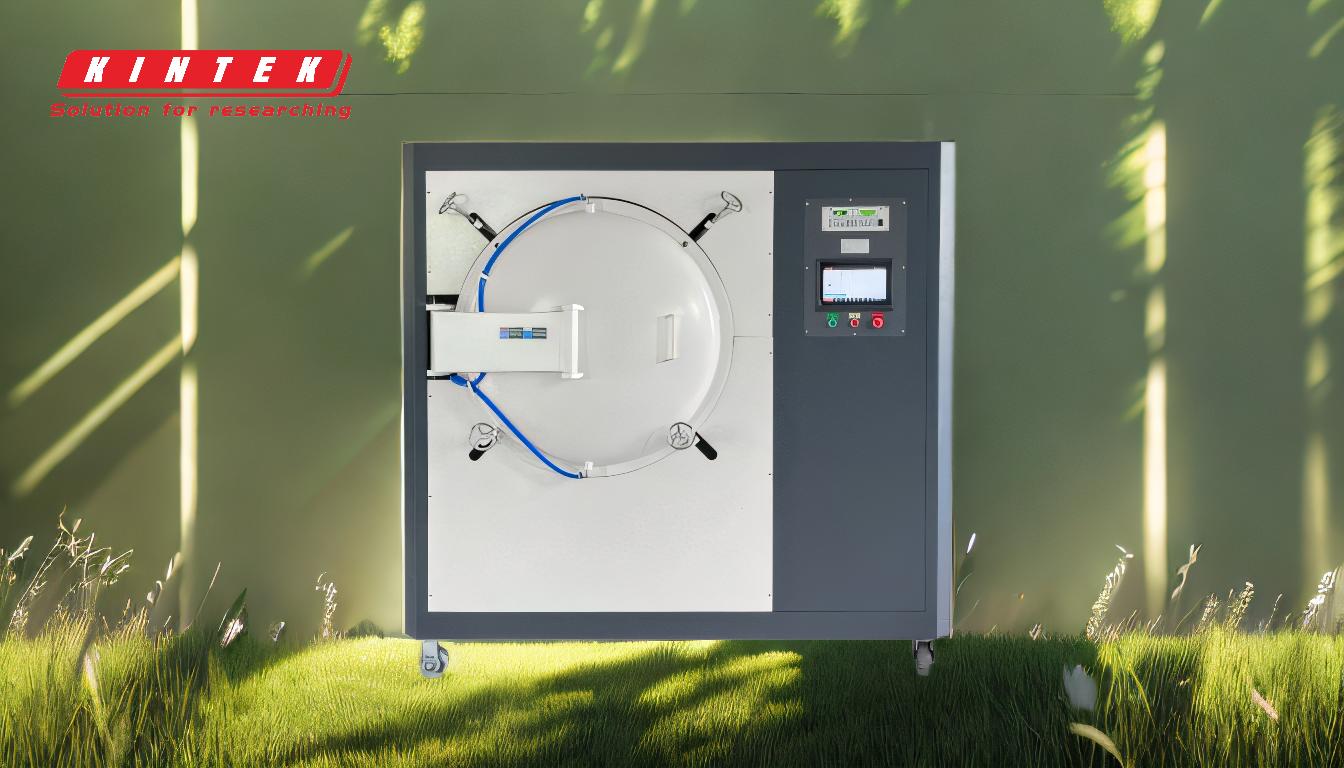
-
Definition and Purpose of Arc Melting:
- Arc melting is an electrothermal process that uses an electric arc to melt metals.
- The primary purpose is to melt metals, such as scrap steel, without changing their chemical composition.
- It is commonly used in metallurgical industries for producing high-quality metals and alloys.
-
Components of an Arc Melting Furnace:
- The main component is the electric welder, which converts standard voltages (220V or 380V) into low voltage and high current.
- The furnace generates an electric arc, which is a self-sustaining discharge phenomenon triggered by the instantaneous short circuit of the positive and negative poles.
- The arc is a thermal plasma with extremely high temperatures, capable of melting metals efficiently.
-
How the Arc Melting Process Works:
- The process begins with the generation of an electric arc between the electrode and the material or between two electrodes.
- The arc produces intense heat, reaching temperatures high enough to melt the metal.
- The molten metal is then collected or further processed, depending on the application.
-
Stages of the Vacuum Arc Melting Process:
- Preparation Stage: The furnace and materials are prepared, and the system is checked for proper functioning.
- Vacuum Stage: The furnace is evacuated to create a vacuum environment, which helps in producing high-purity metals.
- Melting Stage: The electric arc is generated, and the metal is melted under controlled conditions.
- Suction Casting Specimen Stage: The molten metal is cast into molds or specimens for further analysis or use.
- End Stage: The process is concluded, and the furnace is cooled down and cleaned for the next cycle.
-
Advantages of Arc Melting:
- High Purity: The vacuum environment minimizes contamination, resulting in high-purity metals.
- Controlled Melting: The process allows precise control over the melting conditions, ensuring consistent quality.
- Versatility: Arc melting can be used for a wide range of metals and alloys, making it a versatile method in metallurgy.
-
Applications of Arc Melting:
- Scrap Metal Recycling: Arc melting is commonly used to recycle scrap steel and other metals.
- Alloy Production: It is used to produce high-quality alloys with specific properties.
- Research and Development: The process is also used in laboratories for developing new materials and studying metallurgical properties.
-
Comparison with Other Melting Processes:
- Smelting: Unlike smelting, which involves chemical reactions to extract metals from ores, arc melting focuses on melting already extracted metals.
- Induction Melting: Induction melting uses electromagnetic induction to generate heat, while arc melting relies on an electric arc.
- Suspension Melting: Suspension melting involves melting materials in a suspended state, whereas arc melting typically involves a stationary melt pool.
By understanding these key points, one can appreciate the efficiency and versatility of the arc melting process in various industrial and research applications.
Summary Table:
Key Aspect | Details |
---|---|
Definition | Electrothermal process using an electric arc to melt metals. |
Purpose | Melts metals like scrap steel without changing their chemical composition. |
Components | Electric welder, arc generation, and thermal plasma. |
Stages | Preparation, vacuum creation, melting, casting, and cooling. |
Advantages | High purity, controlled melting, and versatility. |
Applications | Scrap recycling, alloy production, and R&D. |
Comparison | Differs from smelting, induction melting, and suspension melting. |
Interested in arc melting solutions? Contact our experts today to learn more!