Brazing is a joining process that involves melting a filler metal to bond two or more metal components together. In terms of safety, brazing requires careful attention to prevent hazards such as burns, inhalation of fumes, and fire risks. Proper safety measures, including the use of protective equipment, adequate ventilation, and adherence to safe handling procedures, are essential to ensure a safe working environment. This process shares similarities with sintering, where safety precautions like wearing protective gear and working in well-ventilated areas are also critical.
Key Points Explained:
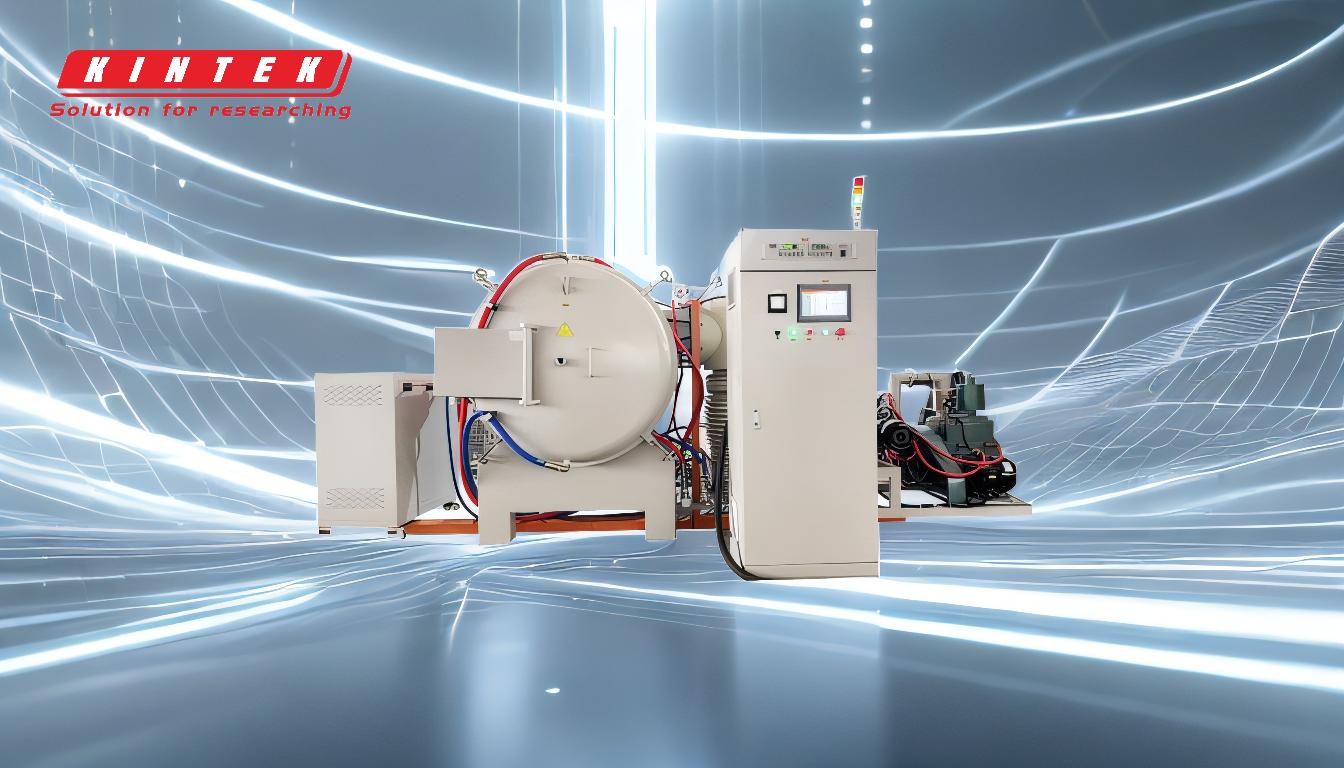
-
Definition of Brazing:
- Brazing is a metal-joining process where a filler metal is melted and flowed into the joint between two or more metal components. The filler metal has a lower melting point than the base metals, allowing it to create a strong bond without melting the components themselves.
-
Safety Hazards in Brazing:
- Heat and Burns: The high temperatures used in brazing can cause severe burns. Operators must wear heat-resistant gloves, face shields, and other protective clothing to minimize the risk of injury.
- Fumes and Gases: The heating of metals and filler materials can release harmful fumes and gases. Proper ventilation or the use of fume extraction systems is necessary to protect workers from inhaling these substances.
- Fire Risks: The open flames or high heat sources used in brazing can ignite flammable materials. Keeping a fire extinguisher nearby and maintaining a clean work area are essential precautions.
-
Protective Equipment:
- Heat-Resistant Gloves: Protect hands from burns caused by hot materials or tools.
- Face Shields and Safety Glasses: Shield the eyes and face from sparks, splashes, and intense light.
- Aprons and Clothing: Wear flame-resistant clothing to protect the body from heat and sparks.
-
Ventilation and Fume Extraction:
- Adequate ventilation is crucial to disperse harmful fumes and gases produced during brazing. Fume extraction systems can be used to capture and remove these substances at the source, ensuring a safer breathing environment.
-
Safe Handling Procedures:
- Material Preparation: Ensure that materials are clean and free from contaminants before brazing to prevent the release of toxic fumes.
- Tool Maintenance: Regularly inspect and maintain brazing equipment to prevent malfunctions that could lead to accidents.
- Work Area Organization: Keep the workspace clean and free of flammable materials to reduce fire hazards.
-
Emergency Preparedness:
- Fire Extinguishers: Always have a fire extinguisher rated for metal fires readily available in the brazing area.
- First Aid Kits: Keep a well-stocked first aid kit nearby to address minor injuries promptly.
- Training: Ensure that all personnel are trained in emergency response procedures, including how to use fire extinguishers and administer first aid.
By following these safety measures, the risks associated with brazing can be significantly reduced, ensuring a safer working environment for all involved.
Summary Table:
Aspect | Details |
---|---|
Definition | A metal-joining process using a filler metal with a lower melting point. |
Safety Hazards | Burns, fumes, gases, and fire risks. |
Protective Equipment | Heat-resistant gloves, face shields, flame-resistant clothing. |
Ventilation | Adequate ventilation or fume extraction systems to disperse harmful fumes. |
Handling Procedures | Clean materials, maintain tools, and organize the workspace. |
Emergency Preparedness | Fire extinguishers, first aid kits, and trained personnel. |
Ensure a safe brazing process—contact our experts today for personalized guidance!