High-frequency induction heating is an advanced thermal processing technology that utilizes electromagnetic induction to generate heat within electrically conductive materials. This non-contact method involves passing a high-frequency alternating current through an induction coil, creating a rapidly alternating magnetic field. When a conductive material is placed within this field, eddy currents are induced, generating heat through Joule heating due to the material's electrical resistance. This process is highly efficient, precise, and controllable, making it suitable for applications such as brazing, hot forging of small workpieces, and surface hardening. High-frequency induction heating is particularly effective for small-scale operations requiring shallow heating depths, typically around 1-2mm, and is widely used in industries like metallurgy, automotive, and electronics.
Key Points Explained:
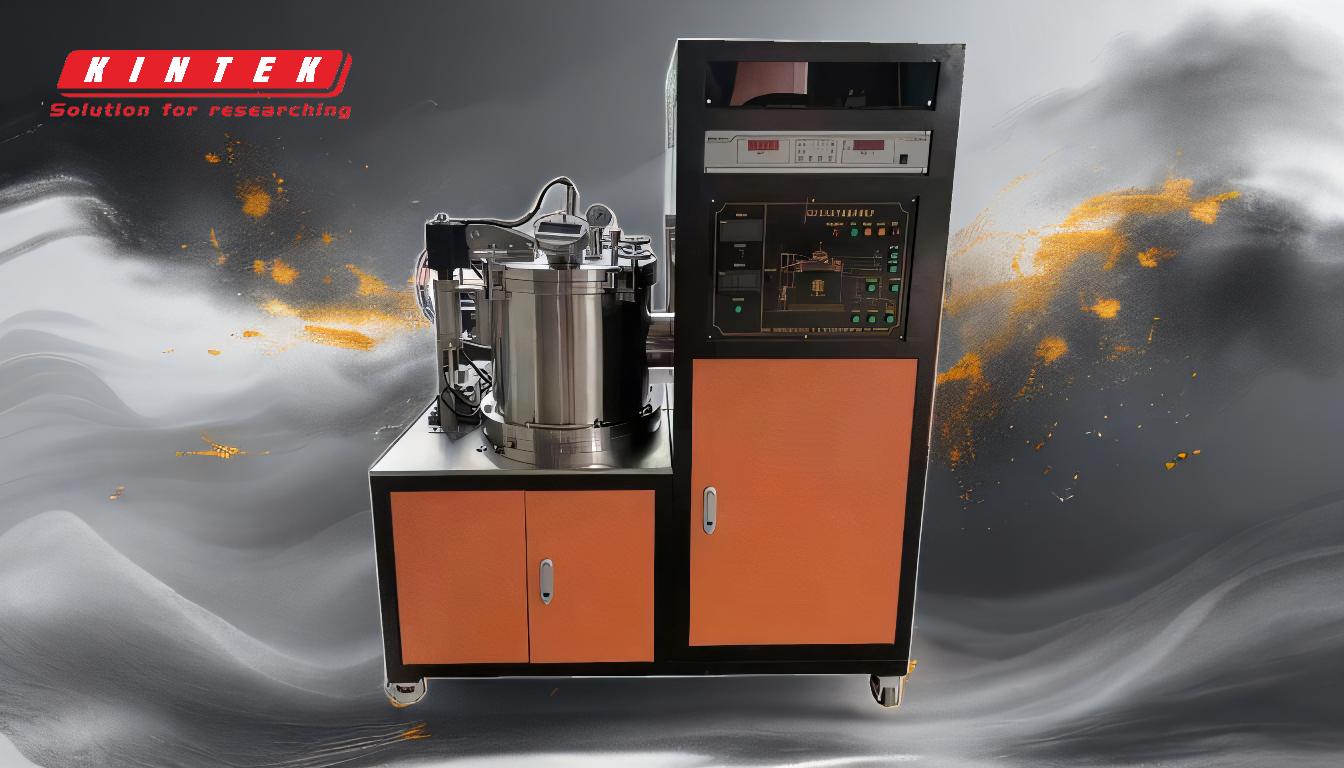
-
Principle of High-Frequency Induction Heating:
- High-frequency induction heating operates on the principles of electromagnetic induction and Joule heating.
- An alternating current in the induction coil generates a rapidly changing magnetic field.
- When a conductive material is placed within this field, eddy currents are induced within the material.
- The flow of these eddy currents against the material's electrical resistance generates heat (Joule heating), which heats the material.
-
Non-Contact Heating Process:
- Unlike traditional heating methods, induction heating does not require direct contact between the heat source and the material.
- This eliminates contamination and allows for precise and localized heating, making it ideal for applications requiring high accuracy and cleanliness.
-
Applications of High-Frequency Induction Heating:
- Brazing: Joining metal parts using a filler material without melting the base metals.
- Hot Forging: Heating small workpieces (typically round bars below 15mm) to make them malleable for shaping.
- Quenching: Rapidly cooling heated metal to achieve desired mechanical properties, often used for surface hardening with shallow layer depths (1-2mm).
- Surface Heating: Targeted heating for applications like tempering, annealing, or hardening of specific areas.
-
Advantages of High-Frequency Induction Heating:
- Efficiency: Direct heating of the material minimizes energy loss, making it highly energy-efficient.
- Precision: The ability to control heating depth and intensity ensures consistent and accurate results.
- Speed: Rapid heating rates reduce processing time, improving productivity.
- Cleanliness: Non-contact heating prevents contamination, making it suitable for sensitive applications like medical devices or electronics.
-
Technical Considerations:
- Frequency Range: High-frequency induction heating typically operates in the range of 50 kHz to several MHz, depending on the application.
- Material Suitability: Works best with electrically conductive materials like metals (e.g., steel, copper, aluminum).
- Heating Depth: The skin effect ensures that heating is concentrated near the surface, making it ideal for shallow-depth applications.
-
Industrial Relevance:
- High-frequency induction heating is widely used in industries such as automotive, aerospace, electronics, and metallurgy.
- It is particularly valuable for small-scale operations requiring precise and localized heating, such as brazing carbide to shafts or sealing tamper-resistant caps on pharmaceuticals.
By leveraging the principles of electromagnetic induction and Joule heating, high-frequency induction heating offers a versatile, efficient, and precise solution for a wide range of industrial thermal processing needs. Its ability to deliver targeted heating with minimal energy loss makes it a preferred choice for applications requiring high accuracy and cleanliness.
Summary Table:
Aspect | Details |
---|---|
Principle | Electromagnetic induction and Joule heating generate heat in conductive materials. |
Non-Contact Process | Eliminates contamination; ensures precise, localized heating. |
Applications | Brazing, hot forging, quenching, and surface hardening. |
Advantages | High efficiency, precision, speed, and cleanliness. |
Frequency Range | 50 kHz to several MHz. |
Material Suitability | Best for conductive metals like steel, copper, and aluminum. |
Industrial Use | Automotive, aerospace, electronics, and metallurgy. |
Ready to explore how high-frequency induction heating can transform your thermal processes? Contact us today for expert guidance!